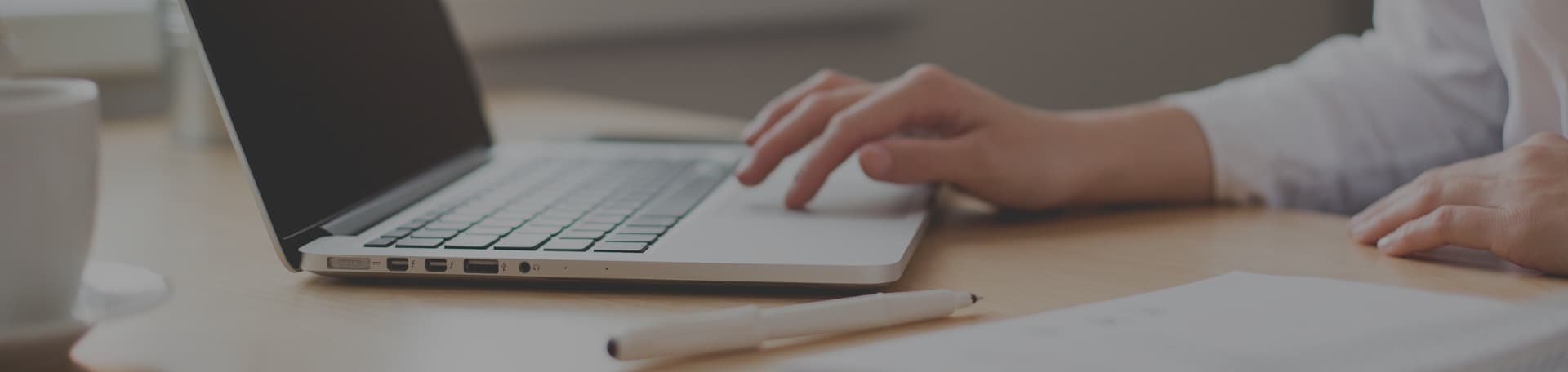
Internal Gear Slewing Bearing: A Comprehensive Guide
Internal Gear Slewing Bearing: A Comprehensive Guide
If you are looking for a bearing that can handle high loads and provide smooth rotation, then an internal gear slewing bearing might be the solution you need. These bearings are designed to accommodate radial, axial, and moment loads, making them ideal for a wide range of applications, including cranes, excavators, wind turbines, and more.

One of the key advantages of internal gear slewing bearings is their ability to transmit torque and power between machine components. This is due to the internal gear design, which allows the bearing to mesh with a driving mechanism and transfer energy efficiently. The gear teeth on the bearing face inward, providing a compact and space-saving solution for power transmission.
Another benefit of internal gear slewing bearings is their versatility. They come in a range of sizes and designs, including ball, roller, wire, and crossed cylindrical bearings, allowing you to choose the right bearing for your specific application. Whether you need a bearing for a small machine or a large industrial application, there is likely an internal gear slewing bearing that can meet your needs.
Fundamentals of Internal Gear Slewing Bearings

Design Principles
Internal gear slewing bearings are mechanical components used in heavy machinery to support axial and radial loads while enabling rotation. They are designed to handle high loads and provide smooth, precise movement. Internal gear slewing bearings are characterized by their integrated gear mechanism, which is usually located on the inner ring. This gear engages with a pinion or other driving mechanism to provide rotation.
The design of internal gear slewing bearings is based on several principles. First, the bearing must be able to handle the loads imposed on it by the machinery. This requires careful consideration of the bearing’s size, shape, and materials. Second, the bearing must be able to provide smooth, precise movement. This requires careful design of the rolling elements and raceways. Finally, the bearing must be able to withstand the harsh operating conditions of heavy machinery, including extreme temperatures, shock, and vibration.
Core Components
Internal gear slewing bearings consist of several core components. These include the inner ring, outer ring, rolling elements, and gear mechanism. The inner ring is the part of the bearing that rotates with the machinery. The outer ring is the stationary part of the bearing that supports the loads imposed on it. The rolling elements are the balls or rollers that enable smooth movement of the bearing. The gear mechanism is the integrated gear system that provides rotation.
The design of these components is critical to the performance of the bearing. The inner and outer rings must be carefully machined to ensure precise movement and load-bearing capacity. The rolling elements must be designed to provide smooth movement while withstanding the loads imposed on them. The gear mechanism must be designed to engage with the driving mechanism while providing reliable, consistent rotation.
In summary, internal gear slewing bearings are critical components of heavy machinery that enable smooth, precise movement while supporting high loads. Their design is based on careful consideration of the loads imposed on them, the need for smooth movement, and the harsh operating conditions of heavy machinery. The core components of internal gear slewing bearings include the inner and outer rings, rolling elements, and gear mechanism, all of which must be carefully designed to ensure reliable performance.
Applications and Use Cases

Slewing bearings with internal gears have a gear mechanism integrated into the bearing’s structure, usually on the inner ring. These gears engage with a pinion or other driving mechanism to control and drive the bearing’s movement. They offer a wide range of applications across various industries. Here are some common use cases for internal gear slewing bearings.
Industrial Machinery
Internal gear slewing bearings are widely used in heavy-duty industrial machinery, such as cranes, excavators, and drilling rigs. They are designed to handle high axial and radial loads and provide smooth rotation for the equipment. These bearings also offer high precision and accuracy, making them ideal for applications that require precise positioning, such as robotics and automated material handling systems.
Renewable Energy Systems
Internal gear slewing bearings are also essential components in renewable energy systems such as wind turbines and solar trackers. They allow the equipment to rotate and track the sun or wind direction, ensuring maximum energy output. These bearings are designed to withstand harsh environmental conditions, including extreme temperatures, high winds, and heavy loads. They also offer low maintenance requirements, which is crucial for remote or offshore installations.
In summary, internal gear slewing bearings are versatile components that offer a wide range of applications in various industries. From heavy-duty industrial machinery to renewable energy systems, these bearings provide high precision, accuracy, and durability, making them an essential component for many critical applications.
Manufacturing Processes
When it comes to manufacturing internal gear slewing bearings, there are a few key processes that are used to ensure the highest quality and precision. These processes include material selection, precision engineering, and more.
Material Selection
One of the most important steps in the manufacturing process of internal gear slewing bearings is material selection. The materials used in the production of these bearings must be strong, durable, and able to withstand heavy loads and extreme conditions. Common materials used for internal gear slewing bearings include alloy steels, stainless steels, and more.
Precision Engineering
Precision engineering is another crucial step in the manufacturing process of internal gear slewing bearings. This involves using advanced technology and machinery to create bearings that are perfectly engineered to meet specific requirements. This includes precision drilling of the installation hole, careful consideration of the center and cutting angle, and the use of high-quality drilling equipment.
Overall, the manufacturing processes used to create internal gear slewing bearings are designed to ensure the highest levels of quality, durability, and precision. By selecting the right materials and using advanced engineering techniques, manufacturers can create bearings that are capable of withstanding even the most extreme conditions and loads.
Installation and Maintenance
When it comes to installing and maintaining internal gear slewing bearings, there are a few key factors to keep in mind. Proper installation and maintenance can help ensure the longevity and reliability of your bearings.
Mounting Techniques
Mounting techniques for internal gear slewing bearings are critical to ensure proper operation. It is important to ensure that the mounting surfaces are flat and machined properly after welding and stress relief treatment on the structures is complete. If subsequent welding is necessary, it must be performed after the bearing is mounted.
During installation, it is important to handle the bearing properly to avoid damage. These bearings are large and heavy, so use lifting equipment and follow safe handling procedures to prevent drops or impacts. Additionally, ensure that the bearing is properly aligned with the mating components to avoid excessive load.
Lubrication and Care
Lubrication is critical to the proper operation of internal gear slewing bearings. Regular lubrication helps to prevent wear and tear on the bearings, which can lead to premature failure. It is important to use the recommended grease for your specific bearing, as outlined in the manufacturer’s instructions.
In addition to proper lubrication, regular inspections and maintenance are important to ensure the longevity of your bearings. Inspect the bearings regularly for signs of wear and tear, such as increased tilting clearance. Replace bearings as needed to prevent further damage to the machinery.
By following proper installation and maintenance techniques, you can help ensure the longevity and reliability of your internal gear slewing bearings.
Performance and Specifications
Load Capacities
Internal gear slewing bearings are designed to accommodate loads acting singly or in combination, and in any direction. The load capacity of a slewing bearing is determined by its size, geometry, and the materials used in its construction. The load carrying capacity of an internal gear slewing bearing is higher than that of an external gear slewing bearing due to the larger diameter of the rolling elements.
The load capacity of a slewing bearing is usually expressed in terms of static and dynamic load ratings. The static load rating refers to the maximum load that a bearing can support without permanent deformation of the rolling elements or the raceways. The dynamic load rating refers to the maximum load that a bearing can support for a specified number of revolutions before fatigue failure occurs.
Accuracy and Efficiency
Internal gear slewing bearings are designed to provide high accuracy and efficiency in rotary applications. The accuracy of a slewing bearing is determined by the tolerances of its components, including the raceways, rolling elements, and gear teeth. The efficiency of a slewing bearing is determined by its frictional losses, which are influenced by the lubrication, the surface finish of the raceways, and the design of the gear teeth.
Internal gear slewing bearings are typically more accurate and efficient than external gear slewing bearings due to the larger diameter of the rolling elements and the more direct transfer of torque between the gear teeth and the raceways. However, internal gear slewing bearings are also more complex to manufacture and assemble, which can increase their cost and lead times.
Overall, internal gear slewing bearings are a reliable and efficient solution for rotary applications that require high load capacity and accuracy. When selecting a slewing bearing, it is important to consider factors such as load capacity, accuracy, efficiency, and cost to ensure that the bearing meets the specific requirements of the application.