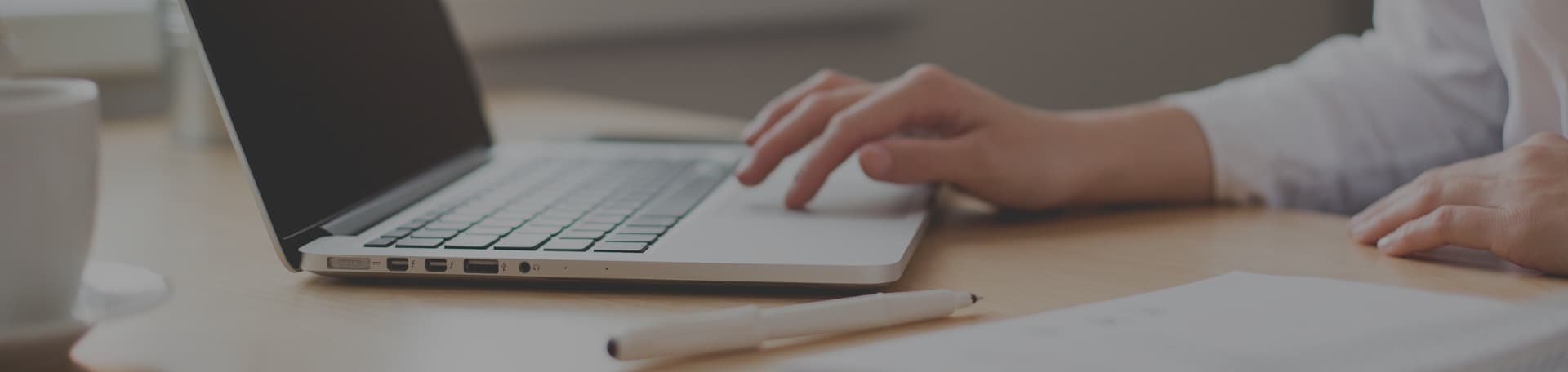
Large Diameter Slewing Bearing: A Comprehensive Guide to its Features and Applications
Large Diameter Slewing Bearing: A Comprehensive Guide to its Features and Applications
If you are in the market for a large diameter slewing bearing, you may be wondering what exactly it is and how it works. A slewing bearing is a type of rotational bearing that is designed to support heavy loads and allow for smooth rotation around a fixed axis. Large diameter slewing bearings, as the name suggests, are used in applications that require a bearing with a large diameter.

These types of bearings are commonly used in construction equipment, cranes, wind turbines, and other heavy machinery. They are designed to withstand extreme loads and operate in harsh environments. Large diameter slewing bearings can be customized to meet specific application requirements, with options for different gear types, sealing options, and materials.
When selecting a large diameter slewing bearing, it is important to consider factors such as load capacity, speed, and operating conditions. By choosing the right bearing for your application, you can ensure optimal performance and longevity of your equipment.
Fundamentals of Large Diameter Slewing Bearings

If you are designing a machine that requires a rotating platform, you will likely need to use a slewing bearing. A slewing bearing is a type of rolling-element bearing that can support axial, radial, and moment loads at the same time. Large diameter slewing bearings are specifically designed to handle heavy loads and high moments. They are used in various applications such as cranes, excavators, wind turbines, and many more.
A large diameter slewing bearing typically consists of an inner ring, an outer ring, rolling elements, and a cage. The inner and outer rings are usually made of high-strength steel and are separated by rolling elements, which can be balls, cylindrical rollers, or tapered rollers. The cage keeps the rolling elements evenly spaced and prevents them from colliding with each other.
One of the most important factors to consider when selecting a large diameter slewing bearing is its load carrying capacity. The load carrying capacity of a slewing bearing depends on various factors such as the diameter of the bearing, the number and size of the rolling elements, and the material properties of the rings and rolling elements. Therefore, it is important to carefully calculate the loads and moments that the bearing will be subjected to during operation.
Another important consideration is the stiffness of the bearing. The stiffness of a slewing bearing determines how much deflection it will experience under load. A more rigid bearing will deflect less than a less rigid bearing, which is important in applications where precise positioning is required.
In summary, large diameter slewing bearings are essential components in many machines that require a rotating platform. They are designed to handle heavy loads and high moments, and their load carrying capacity and stiffness are important factors to consider when selecting a bearing for a specific application.
Design and Engineering Considerations

When considering the design and engineering of large diameter slewing bearings, there are several key factors to take into account. These include material selection, structural integrity, and load distribution.
Material Selection
Choosing the right materials is critical when designing large diameter slewing bearings. Typically, these bearings are made from high-strength steels, such as alloy or carbon steels, which can withstand the high loads and stresses that they will be subjected to. Other materials that may be used include stainless steel, aluminum, and titanium, depending on the specific application.
Structural Integrity
Structural integrity is another important consideration when designing large diameter slewing bearings. The bearings must be able to withstand the loads and stresses that they will be subjected to without deforming or failing. This requires careful design and engineering, including the use of finite element analysis (FEA) and other simulation tools to ensure that the bearings will perform as expected.
Load Distribution
Load distribution is also critical when designing large diameter slewing bearings. These bearings must be able to distribute loads evenly across their surfaces to prevent localized stress concentrations that could lead to failure. This requires careful attention to the design of the bearing raceways, as well as the use of advanced lubrication systems to ensure that the bearings operate smoothly and efficiently.
In summary, designing large diameter slewing bearings requires careful consideration of a range of factors, including material selection, structural integrity, and load distribution. By taking these factors into account and using advanced design and engineering techniques, it is possible to create bearings that are capable of withstanding even the most demanding applications.
Manufacturing Processes
When it comes to manufacturing large diameter slewing bearings, there are several essential processes involved. These processes help to ensure that the final product is of high quality and can withstand the rigors of heavy-duty applications. In this section, we will look at some of the key manufacturing processes involved in producing large diameter slewing bearings.
Forging and Machining
One of the first steps in manufacturing large diameter slewing bearings is forging and machining. This involves taking raw materials such as carbon chromium-bearing steel and shaping them into the desired form. The raw materials are cut to size, heated to a specific temperature, and then forged into the rough shape of the slewing bearing. The bearing is then machined to its final dimensions, ensuring that it meets the required specifications.
Heat Treatment
Heat treatment is another critical process in the manufacturing of large diameter slewing bearings. This process involves subjecting the bearing to high temperatures to improve its strength, durability, and wear resistance. The heat treatment process can vary depending on the specific application of the slewing bearing. Common heat treatment methods include quenching and tempering, carburizing, and nitriding.
Quality Control
Quality control is an essential part of the manufacturing process for large diameter slewing bearings. This involves rigorous testing and inspection to ensure that the final product meets the required standards. Quality control measures can include non-destructive testing, dimensional inspection, and material testing. By implementing strict quality control measures, manufacturers can ensure that their slewing bearings are of the highest quality and can withstand heavy-duty applications.
In conclusion, the manufacturing of large diameter slewing bearings involves several critical processes. These processes ensure that the final product is robust, durable, and can withstand the rigors of heavy-duty applications. By implementing strict quality control measures and using high-quality materials, manufacturers can produce slewing bearings that meet the highest standards of quality and performance.
Applications and Industry Use
Large diameter slewing bearings are used in a wide range of industries and applications due to their ability to handle heavy loads while enabling smooth and controlled rotation. Some of the common industries and applications where large diameter slewing bearings are used include wind turbines, construction machinery, and medical equipment.
Wind Turbines
Wind turbines require large diameter slewing bearings to enable the rotation of the blades and to ensure that the turbines can track the direction of the wind. These bearings need to be able to handle high axial and radial loads, as well as withstand harsh environmental conditions. Large diameter slewing bearings are also used in the yaw and pitch systems of wind turbines.
Construction Machinery
Large diameter slewing bearings are used in various types of construction machinery, such as cranes, excavators, and drilling rigs. These bearings enable the rotation of the machinery and ensure that it can handle heavy loads. In addition, slewing bearings are used in the steering systems of some construction machinery.
Medical Equipment
Large diameter slewing bearings are used in various types of medical equipment, such as CT scanners and MRI machines. These bearings enable the smooth and precise rotation of the equipment, which is essential for accurate imaging. Slewing bearings are also used in other medical equipment such as operating tables and dental chairs.
Overall, large diameter slewing bearings are essential components in many industries and applications where heavy loads need to be handled while enabling smooth and controlled rotation.
Maintenance and Servicing
Large diameter slewing bearings are custom-engineered and manufactured almost exclusively for lifting equipment that requires rotation. These devices typically have a complex load spectrum: the slewing ring bearing can simultaneously handle all combinations of thrust, radial, and moment loads. As a result, proper maintenance and servicing are critical to ensure the longevity and safety of the equipment. In this section, we will discuss the key aspects of maintenance and servicing for large diameter slewing bearings.
Regular Inspection
Regular inspection is crucial to detect any issues early on and prevent costly downtime. You should inspect the slewing bearing for signs of wear, fatigue, and damage. This includes checking for cracks, corrosion, and pitting on the raceways, rolling elements, and gears. You should also check the preload, clearance, and axial/radial runout of the bearing. Regular inspection intervals vary depending on the application and operating conditions. However, a good rule of thumb is to inspect the bearing at least once a year or after every 2,000 hours of operation.
Lubrication and Sealing
Proper lubrication and sealing are essential to prevent premature failure of the slewing bearing. You should follow the manufacturer’s recommendations for the type and frequency of lubrication. Over-lubrication can cause overheating, while under-lubrication can cause excessive wear and failure. You should also inspect the seals regularly for signs of wear or damage and replace them if necessary. Proper sealing prevents contamination and moisture ingress, which can cause corrosion and premature wear.
Replacement Strategies
If you detect any signs of wear or damage during inspection, you should replace the slewing bearing promptly. Replacement strategies vary depending on the application, size, and complexity of the bearing. In some cases, it may be possible to replace the rolling elements or raceways individually. However, in most cases, it is more cost-effective to replace the entire bearing assembly. You should also consider upgrading to a higher-quality bearing or a different type of bearing if the application requirements change.
In summary, proper maintenance and servicing are critical to ensure the longevity and safety of large diameter slewing bearings. Regular inspection, lubrication, and sealing, as well as prompt replacement strategies, are key aspects of maintenance and servicing. By following these guidelines, you can minimize downtime, reduce maintenance costs, and extend the life of your slewing bearing.
Future Trends and Innovations
As technology advances, the future of large diameter slewing bearings looks promising. Here are some of the trends and innovations that you can expect to see in the coming years:
1. Smart Slewing Bearings
Smart slewing bearings will be equipped with sensors that can monitor their performance and detect any potential issues. This technology will enable real-time data analysis, enabling you to predict when maintenance is required, and avoid costly downtime.
2. Improved Materials
The use of advanced materials such as ceramics and composites will improve the strength and durability of large diameter slewing bearings. These materials have superior wear resistance, which will result in longer service life and reduced maintenance costs.
3. 3D Printing
3D printing technology will enable the production of complex geometries, which will be difficult or impossible to achieve with traditional manufacturing methods. This technology will enable the production of bespoke slewing bearings, which will be tailored to meet specific requirements.
4. Increased Automation
Automation will play a significant role in the future of large diameter slewing bearings. Automation will enable the integration of slewing bearings into complex systems, such as robotics and wind turbines, which will result in increased efficiency and productivity.
5. Environmentally Friendly Solutions
The demand for environmentally friendly solutions is increasing, and slewing bearing manufacturers are responding to this demand by developing more sustainable products. For example, the use of biodegradable lubricants will reduce the environmental impact of large diameter slewing bearings.
In conclusion, the future of large diameter slewing bearings looks bright, with new technologies and materials promising to improve their performance and durability. As a result, you can expect to see increased efficiency, reduced maintenance costs, and improved sustainability in the coming years.