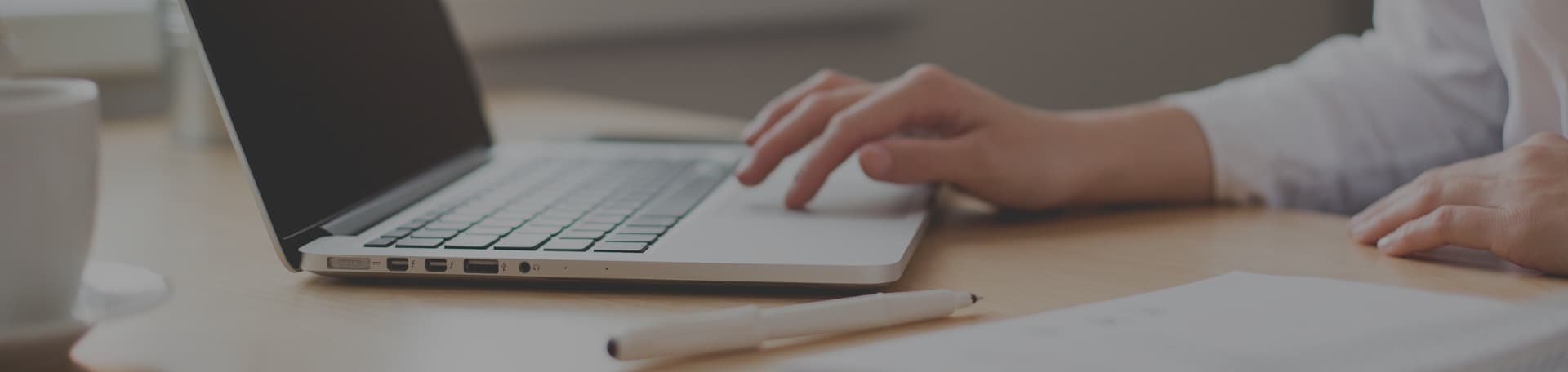
Large Diameter Slewing Bearings: Applications and Advantages
Large Diameter Slewing Bearings: Applications and Advantages
If you’re in the market for large diameter bearings, you may have come across the term “slewing bearings.” These specialized bearings are designed to handle large axial and radial loads while simultaneously enabling rotational movement. They are commonly used in heavy machinery and equipment, such as cranes, excavators, and wind turbines.

Slewing bearings come in a variety of designs and sizes, ranging from small bearings with an outside diameter of 0.1 meters to large bearings with an outside diameter of up to 18 meters. The most common types of slewing bearings are ball and roller bearings, which are designed to accommodate different types of loads and movements. Other types of slewing bearings include crossed roller bearings, which are ideal for applications that require high precision and accuracy, and four-point contact bearings, which are designed to handle both axial and radial loads.
Overall, the choice of slewing bearing will depend on the specific requirements of your application. Factors to consider include the size and weight of the equipment, the type of loads it will be subjected to, and the amount of rotational movement required. By working with an experienced bearing supplier, you can ensure that you select the right type and size of slewing bearing for your needs.
Fundamentals of Large Diameter Slewing Bearings

Large diameter slewing bearings are an essential component of many machines and structures that require rotational movement. These bearings are designed to handle axial, radial, and moment loads in any direction, making them ideal for applications such as cranes, excavators, wind turbines, and more. In this section, we will discuss the design principles, load capabilities, and material selection considerations for large diameter slewing bearings.
Design Principles
The design of large diameter slewing bearings is based on a few fundamental principles. First, the bearing must be able to handle the loads placed upon it while maintaining its structural integrity. This requires careful consideration of the bearing’s geometry, material properties, and manufacturing processes.
Second, the bearing must be able to rotate smoothly and without excessive friction. This requires careful consideration of the bearing’s lubrication system, as well as its sealing and protection mechanisms.
Finally, the bearing must be designed to withstand the environmental conditions in which it will be used. This includes considerations such as temperature, humidity, and exposure to corrosive substances.
Load Capabilities
Large diameter slewing bearings are capable of handling a wide range of loads, including axial, radial, and moment loads. The load capacity of a bearing is determined by its geometry, material properties, and manufacturing processes.
Axial loads are those that act parallel to the axis of rotation, while radial loads act perpendicular to the axis of rotation. Moment loads are those that act at an angle to the axis of rotation. Large diameter slewing bearings are designed to handle all three types of loads simultaneously, making them ideal for applications that require complex movements.
Material Selection
The selection of materials for large diameter slewing bearings is critical to their performance and longevity. The most commonly used materials for these bearings include high-quality steels, such as 42CrMo4, 50Mn, and 55SiMnMo.
These materials offer excellent strength, toughness, and durability, making them ideal for use in demanding applications. Other factors to consider when selecting materials for large diameter slewing bearings include corrosion resistance, fatigue resistance, and machinability.
In conclusion, large diameter slewing bearings are an essential component of many machines and structures that require rotational movement. By understanding the design principles, load capabilities, and material selection considerations for these bearings, you can ensure that your applications are safe, reliable, and efficient.
Types of Large Diameter Slewing Bearings

When it comes to large diameter slewing bearings, there are four main types to consider: Single-Row Ball Type, Double-Row Ball Type, Crossed Roller Type, and Three-Row Roller Type. Each type has its own unique design and features, making it important to understand the differences between them before selecting the right one for your application.
Single-Row Ball Type
Single-Row Ball Type slewing bearings are the most common type and are ideal for applications that require low friction and high precision. They consist of a single row of balls that run in a raceway, providing smooth rotational movement. These bearings are typically used in applications such as cranes, excavators, and wind turbines.
Double-Row Ball Type
Double-Row Ball Type slewing bearings are similar to Single-Row Ball Type bearings, but with two rows of balls running in a raceway. This design provides increased load capacity and stiffness, making them suitable for applications that require heavy loads and high precision. These bearings are commonly used in applications such as tunnel boring machines and mining equipment.
Crossed Roller Type
Crossed Roller Type slewing bearings use rollers that are crossed at right angles to each other, providing a high degree of stiffness and precision. This design allows for greater load capacity than ball-type bearings and is ideal for applications that require high accuracy and stability, such as robotics and machine tools.
Three-Row Roller Type
Three-Row Roller Type slewing bearings consist of three rows of rollers that run in three raceways. This design provides the highest load capacity of all the slewing bearing types and is ideal for applications that require heavy loads and high precision. These bearings are commonly used in applications such as cranes, excavators, and wind turbines.
In conclusion, selecting the right type of large diameter slewing bearing is crucial to ensure the success of your application. By understanding the differences between each type, you can make an informed decision and choose the bearing that best meets your specific needs.
Applications of Large Diameter Slewing Bearings
Large diameter slewing bearings have a wide range of applications, from wind turbines to medical equipment. In this section, we’ll explore some of the most common applications of large diameter slewing bearings.
Wind Turbines
Wind turbines require large diameter slewing bearings to ensure that they can rotate and track the wind. These bearings are typically used in the yaw and pitch systems of the turbine, allowing the blades to rotate and adjust their angle to maximize energy generation. Large diameter slewing bearings are also used in the main bearing of the turbine, which supports the weight of the rotor and nacelle.
Cranes and Excavators
Cranes and excavators require large diameter slewing bearings to support their weight and enable them to rotate. These bearings are typically used in the turntable of the crane or excavator, allowing the machine to rotate 360 degrees. Large diameter slewing bearings are also used in the boom and jib of the crane, allowing it to lift and move heavy loads.
Medical Equipment
Large diameter slewing bearings are used in a variety of medical equipment, including CT scanners, MRI machines, and radiation therapy machines. These bearings are used to support the rotating components of the machines, allowing them to move smoothly and accurately. Large diameter slewing bearings are also used in surgical tables, enabling them to rotate and adjust to the proper position for the procedure.
In conclusion, large diameter slewing bearings are essential components in a wide range of applications, from wind turbines to medical equipment. These bearings are designed to support heavy loads and enable smooth rotation, ensuring that the machines they are used in operate efficiently and effectively.
Manufacturing Processes
Large diameter slewing bearings are critical components used in a wide range of applications, including cranes, excavators, wind turbines, and other industrial machinery. The manufacturing processes used to produce these bearings are complex and require high levels of precision, quality control, and attention to detail.
Forging and Heat Treatment
The first step in the manufacturing process of large diameter slewing bearings is forging. This process involves shaping a piece of metal into the desired shape and size using a hammer or press. The forged ring is then heat treated to improve its strength and hardness. The heat treatment process involves heating the ring to a specific temperature and then cooling it down slowly to ensure the desired properties are achieved.
Precision Machining
Once the ring is forged and heat-treated, it undergoes precision machining to achieve the final dimensions and tolerances required. This process involves using specialized equipment such as lathes, grinders, and milling machines to remove material from the ring and create the necessary features such as raceways, bolt holes, and gear teeth.
Quality Assurance
Quality assurance is a critical aspect of the manufacturing process for large diameter slewing bearings. Every stage of the process is closely monitored and inspected to ensure that the final product meets the required specifications and standards. This includes dimensional checks, material testing, and non-destructive testing such as magnetic particle inspection and ultrasonic testing.
In conclusion, the manufacturing processes used to produce large diameter slewing bearings are complex and require highly skilled personnel, specialized equipment, and stringent quality control measures. By following these processes, manufacturers can produce high-quality bearings that meet the demanding requirements of various industries.
Maintenance and Servicing
Large diameter slewing bearings are critical components in heavy-duty equipment such as cranes, excavators, and tunnel boring machines. Proper maintenance and servicing are essential to ensure the longevity and reliable performance of these bearings. In this section, we will discuss the key aspects of maintenance and servicing of large diameter slewing bearings.
Regular Inspection
Regular inspection is crucial to detect any signs of wear, damage, or misalignment of the slewing bearing. You should inspect the bearing at least once a year or more frequently depending on the operating conditions. During the inspection, you should check for the following:
- Cracks or fractures on the bearing raceways, balls, or rollers
- Wear or pitting on the raceways or rolling elements
- Corrosion or rust on the bearing surfaces
- Misalignment or deformation of the bearing rings
- Loose bolts or fasteners
You should also check the mating components such as the gears, pinions, and shafts for any signs of wear or damage that may affect the performance of the slewing bearing.
Lubrication and Sealing
Proper lubrication and sealing are critical to prevent premature wear and failure of the slewing bearing. You should follow the manufacturer’s recommendations for the type and amount of lubricant to use. Over-lubrication can cause overheating and premature failure, while under-lubrication can cause excessive wear and damage to the bearing surfaces.
You should also check the sealing system to ensure that it is functioning correctly. The seals should prevent the entry of contaminants such as dirt, dust, and water into the bearing. Any damage or wear to the seals should be repaired or replaced promptly to prevent contamination of the lubricant and premature failure of the bearing.
Replacement Procedures
If the slewing bearing shows signs of wear, damage, or misalignment, you should replace it promptly. Replacement procedures may vary depending on the type and size of the bearing and the equipment’s design. You should follow the manufacturer’s recommendations for the replacement procedure, including the torque specifications for the bolts and fasteners.
You should also inspect the mating components such as the gears, pinions, and shafts for any signs of wear or damage that may have caused the failure of the slewing bearing. Any damaged components should be repaired or replaced before installing the new bearing.
In summary, regular inspection, proper lubrication and sealing, and prompt replacement of worn or damaged slewing bearings are essential to ensure the reliable performance and longevity of heavy-duty equipment.