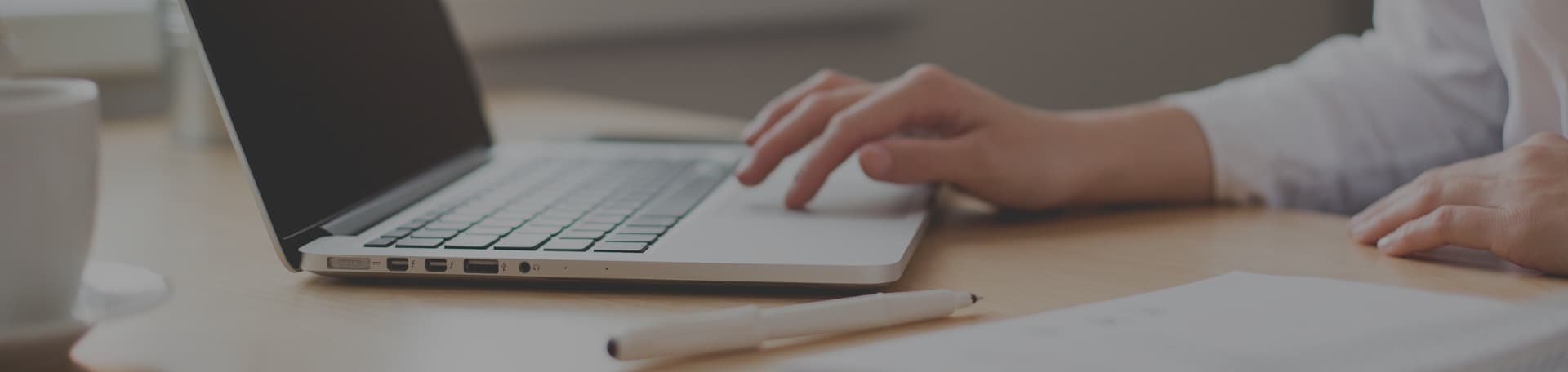
Rocker and Roller Bearings: Suitable for Spans
Rocker and Roller Bearings: Suitable for Spans
Rocker and roller bearings are crucial components of bridge structures, designed to transfer large horizontal movements and resist transverse rotation at supports. They are used in spans of various lengths, depending on the type of bearing and the specific requirements of the bridge. Rocker bearings are made of cast steel or reinforced concrete and are suitable for spans greater than 20 meters, while sliding steel plane or curved bearings are used for shorter spans.

Linear rocker bearings are often suitable at both ends for simply supported spans up to about 20 meters. For rail bridges of span greater than 20 meters, fabricated roller/rocker bearings can be used at the free end. Line rocker bearings are of benefit in some half-through type rail bridges in resisting transverse rotation at supports. At expansion bearings, the spans should be provided with rollers, rockers, or sliding plates. In the case of short spans, the spans may slide on smooth metal plates.
This article will explore the different types of rocker and roller bearings used in bridge structures, their design and behavior, and their suitability for spans of different lengths. It will also discuss the advantages and disadvantages of each type of bearing and provide examples of their applications in various bridge projects. Whether you are a civil engineer, a bridge designer, or simply interested in the mechanics of bridge structures, this article will provide you with a comprehensive understanding of the importance of rocker and roller bearings in bridge construction.
Fundamentals of Rocker and Roller Bearings

Rocker and roller bearings are types of bridge bearings used to accommodate movements in bridge structures. They are designed to allow for rotation and longitudinal movement at the expansion end of the structure while being rigidly attached to a masonry plate at the fixed end.
Types of Rocker Bearings
There are two main types of rocker bearings: steel rocker bearings and elastomeric rocker bearings. Steel rocker bearings consist of a pinned joint to accommodate rotation and a rocker to accommodate longitudinal movement. At the fixed end, there is no rocker, and the bearing is rigidly attached to a masonry plate. Steel rocker bearings do not allow for transverse movement. On the other hand, elastomeric rocker bearings are made of a layer of elastomer sandwiched between two steel plates. They are designed to allow for limited rotation and longitudinal movement and provide a certain level of damping to the structure.
Types of Roller Bearings
Roller bearings are another type of bridge bearings that allow for movement in structures. There are two main types of roller bearings: pot bearings and spherical bearings. Pot bearings consist of a concave pot and a convex disc that allows for limited rotation and longitudinal movement. They are suitable for spans up to 50 meters. Spherical bearings, on the other hand, consist of a steel plate with a concave spherical surface and a matching convex spherical surface. They allow for rotation and longitudinal movement and are suitable for spans up to 150 meters.
In summary, rocker and roller bearings are essential components of bridge structures that allow for movement and accommodate the forces generated by the structure’s traffic and environment. Steel rocker bearings, elastomeric rocker bearings, pot bearings, and spherical bearings are all suitable for different spans and movements in bridge structures.
Design Considerations for Bearings in Bridge Spans
Rocker and roller bearings are commonly used in bridges to provide support and allow for movement due to changes in temperature and other environmental factors. When designing bearings for bridge spans, there are several key considerations to keep in mind.
Load Distribution
One important consideration when designing bearings for bridge spans is load distribution. Bearings must be able to distribute the weight of the bridge evenly across the supporting structure. This is particularly important for longer spans, as uneven weight distribution can cause structural damage and compromise the safety of the bridge.
To ensure proper load distribution, bearings must be designed to accommodate the specific weight and configuration of the bridge. This may involve using different types of bearings, such as rocker or roller bearings, depending on the span length and other factors.
Span Dynamics
Another important consideration when designing bearings for bridge spans is span dynamics. Bridges are subject to a wide range of dynamic forces, including wind, water, and traffic. Bearings must be able to accommodate these forces and allow for movement without compromising the structural integrity of the bridge.
To ensure proper span dynamics, bearings must be designed to allow for controlled movement in response to changes in the environment. This may involve using different types of bearings, such as rocker or roller bearings, depending on the specific dynamics of the bridge.
Overall, designing bearings for bridge spans requires careful consideration of load distribution, span dynamics, and other key factors. By using the right types of bearings and designing them to accommodate the specific needs of the bridge, engineers can ensure that bridges are safe, reliable, and able to withstand the forces of nature and the demands of modern transportation.
Installation and Maintenance Procedures
Installation Best Practices
When it comes to installing rocker and roller bearings, it is important to follow best practices to ensure that they are properly installed and will function as intended. One important consideration is ensuring that the bearings are properly aligned and level. This can be accomplished by using precision leveling instruments and shims as needed.
Another important consideration is ensuring that the bearings are properly anchored to the bridge structure. This can be accomplished by using high-strength anchor bolts and ensuring that they are properly torqued to the manufacturer’s specifications. It is also important to ensure that the bearings are properly greased and that any required protective coatings are applied.
Maintenance and Inspection
Once rocker and roller bearings are installed, it is important to perform regular maintenance and inspections to ensure that they are functioning as intended. This can include visual inspections, as well as more detailed inspections using non-destructive testing methods such as ultrasonic testing.
One important consideration when it comes to maintenance is ensuring that the bearings are properly lubricated. This can be accomplished by using a high-quality lubricant that is recommended by the bearing manufacturer. It is also important to ensure that any protective coatings are properly maintained and that any damage or wear to the bearings is addressed in a timely manner.
Overall, by following best practices for installation and performing regular maintenance and inspections, it is possible to ensure that rocker and roller bearings will function as intended and provide reliable support for bridge spans.
Case Studies and Applications
Historical Uses
Rocker and roller bearings have been used for centuries in various applications, including bridge construction. Historical examples of rocker bearings can be found in the ancient Roman aqueducts, where they were used to support the water channels. Similarly, roller bearings were used in the construction of the Great Wall of China to allow for movement and expansion caused by temperature changes.
Modern Engineering Projects
In modern times, rocker and roller bearings are still widely used in bridge construction. For example, the Washington State Department of Transportation (WSDOT) used steel rocker bearings to replace the existing bearings on a 113.0-m single-span truss bridge built in 1925. The replacement project was designed to restore expansion capability and improve the bridge’s overall safety and reliability [1].
Another example of modern engineering projects that use rocker and roller bearings is the construction of viaducts. Fabricated linear rocker bearings are often suitable for simply supported spans up to about 20 m, while fabricated roller/rocker bearings can be used at the free end for rail bridges of span greater than 20 m [2].
Overall, rocker and roller bearings are versatile and reliable solutions for supporting bridges and other structures that require movement and expansion capabilities. Their historical uses and modern engineering applications demonstrate their effectiveness and durability.