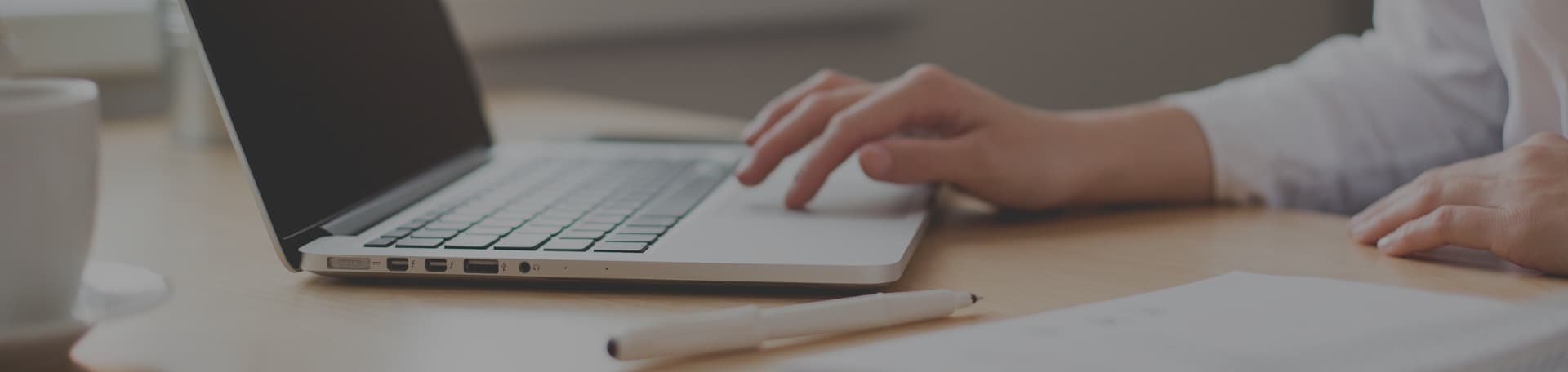
Rolling Contact Bearing Numerical Analysis: Understanding the Basics
Rolling Contact Bearing Numerical Analysis: Understanding the Basics
Rolling contact bearings are machine elements that are designed to support rotating shafts while minimizing friction between the two surfaces. These bearings are used in a wide variety of applications, from automotive engines to industrial machinery. The design of rolling contact bearings has been refined over many decades, resulting in highly efficient and reliable components that are essential for many modern machines.

Numerical analysis has become an increasingly important tool for the design and optimization of rolling contact bearings. By using numerical methods, engineers can simulate the behavior of bearings under different loads, speeds, and other operating conditions. This allows them to optimize the design of the bearings to improve performance, reduce wear and tear, and increase the service life of the components. Numerical analysis can also help engineers to identify potential problems before they occur, allowing for preventative maintenance and reducing the risk of costly downtime.
Fundamentals of Rolling Contact Bearings

Rolling contact bearings are machine elements that support rotating shafts. They are designed to transmit loads between two or more parts of a machine. The essential parts of a rolling bearing are an outer ring (race), an inner ring (race), rolling elements (balls or rollers), and a separator (or retainer or cage). The term rolling contact bearings refers to the wide variety of bearings that use spherical balls or some other type of roller between the stationary and the moving elements.
Bearing Geometry and Contact Mechanics
The geometry of a rolling contact bearing is critical to its performance. The contact between the rolling elements and the races is a complex process that involves deformation of the races and the rolling elements. The contact stress distribution between the rolling elements and the races depends on the geometry of the bearing and the load distribution. The load distribution is affected by the number of rolling elements, the size of the bearing, and the direction and magnitude of the load.
Load Distribution and Contact Stresses
The load distribution in a rolling contact bearing is not uniform. The load is distributed unevenly between the rolling elements due to the curvature of the races. The contact stress between the rolling elements and the races is highest at the point of contact and decreases as the distance from the contact point increases. The maximum contact stress occurs at the point of contact between the rolling element and the race. The contact stress is affected by the geometry of the bearing, the number of rolling elements, the size of the bearing, and the direction and magnitude of the load.
In summary, rolling contact bearings are an essential component of many machines. The geometry of a rolling contact bearing is critical to its performance. The contact between the rolling elements and the races is a complex process that involves deformation of the races and the rolling elements. The load distribution in a rolling contact bearing is not uniform, and the contact stress between the rolling elements and the races is highest at the point of contact.
Numerical Analysis Techniques
Finite Element Method Basics
The Finite Element Method (FEM) is a numerical technique that is commonly used to solve problems in engineering and applied sciences. The method involves dividing a complex structure into smaller, simpler elements, and then solving the equations that govern the behavior of those elements. This approach is particularly useful for solving problems that are too complex to be solved analytically.
In the context of rolling contact bearings, FEM is used to calculate the deformation of the bearing elements under load. This information is then used to calculate the contact stresses and other performance parameters. FEM is a powerful tool for predicting the performance of rolling contact bearings, and can be used to optimize the design of new bearings or to diagnose problems with existing ones.
Computational Modeling of Bearings
Computational modeling of bearings involves creating a virtual model of the bearing and simulating its behavior under various operating conditions. This approach is particularly useful for studying the effects of different design parameters on bearing performance, and for predicting the performance of new designs.
One of the key advantages of computational modeling is that it allows engineers to test a wide range of design options quickly and inexpensively. By simulating the behavior of a bearing under different operating conditions, engineers can identify potential problems and make design changes before the bearing is manufactured.
Computational modeling can also be used to diagnose problems with existing bearings. By comparing the simulated behavior of a bearing to its actual performance, engineers can identify the root cause of problems and develop solutions to improve performance.
Overall, numerical analysis techniques are a powerful tool for designing and optimizing rolling contact bearings. By using FEM and computational modeling, engineers can predict the performance of new designs, diagnose problems with existing bearings, and optimize the performance of rolling contact bearings in a wide range of applications.
Bearing Life Prediction
Rolling contact bearings are an essential component in many machines, and their failure can lead to costly downtime and repairs. Therefore, predicting the bearing’s life is crucial for maintenance planning and cost-effective operation. There are various approaches to predict bearing life, including empirical, analytical, and numerical methods.
Dynamic Load Ratings
Dynamic load ratings are commonly used in bearing life prediction, and they are defined as the maximum load that a bearing can sustain for a specified number of revolutions without failure. The dynamic load rating is based on the assumption that the bearing’s fatigue life is inversely proportional to the cube of the applied load. Therefore, the dynamic load rating is a critical factor in bearing selection and can be used to compare different bearing types and sizes.
Stress-Life Approach
The stress-life approach is another popular method for bearing life prediction. This approach is based on the assumption that the bearing’s fatigue life is inversely proportional to the maximum cyclic stress applied to the material. The stress-life approach involves calculating the maximum cyclic stress in the bearing and comparing it to the material’s endurance limit. The endurance limit is the maximum stress that a material can withstand for an infinite number of cycles without failure.
Numerical methods, such as the finite element method (FEM), have become increasingly popular for bearing life prediction. The FEM can provide detailed stress and strain information throughout the bearing, allowing for more accurate predictions. Additionally, the FEM can account for various factors that affect bearing life, such as material properties, surface roughness, and lubrication.
In conclusion, bearing life prediction is a crucial task in ensuring the reliable and cost-effective operation of machines. There are various approaches to predict bearing life, including empirical, analytical, and numerical methods. The dynamic load rating and stress-life approach are commonly used analytical methods, while numerical methods, such as the FEM, can provide more accurate predictions.
Design Considerations and Optimization
Rolling contact bearings are critical components in many industrial applications. In order to ensure their reliable operation, several design considerations must be taken into account.
Material Selection
The choice of material for rolling contact bearings is crucial for their performance and durability. Common materials used for bearing components include high-carbon chromium bearing steel, stainless steel, and ceramic. Each material has its own strengths and weaknesses, and the selection depends on the specific application requirements.
High-carbon chromium bearing steel is the most commonly used material for bearing components due to its high strength and durability. Stainless steel is used in applications where corrosion resistance is critical. Ceramic bearings are used in applications where high temperature and high speed are required.
Lubrication and Maintenance Strategies
Lubrication is essential for the proper operation of rolling contact bearings. It reduces friction and wear, dissipates heat, and protects against corrosion. Proper lubrication can significantly extend the life of bearings and reduce maintenance costs.
There are several lubrication strategies, including oil lubrication, grease lubrication, and solid lubrication. The choice of lubrication method depends on the specific application requirements. Oil lubrication is used in high-speed applications where heat dissipation is critical. Grease lubrication is used in applications where contamination is a concern. Solid lubrication is used in applications where high temperature and high speed are required.
Maintenance is also critical for the proper operation of rolling contact bearings. Regular inspection and cleaning can prevent premature failure and extend the life of the bearings. The frequency of maintenance depends on the specific application requirements and the operating conditions.
In summary, the design considerations and optimization of rolling contact bearings are critical for their reliable operation. Material selection, lubrication, and maintenance strategies must be carefully considered to ensure the best performance and durability.