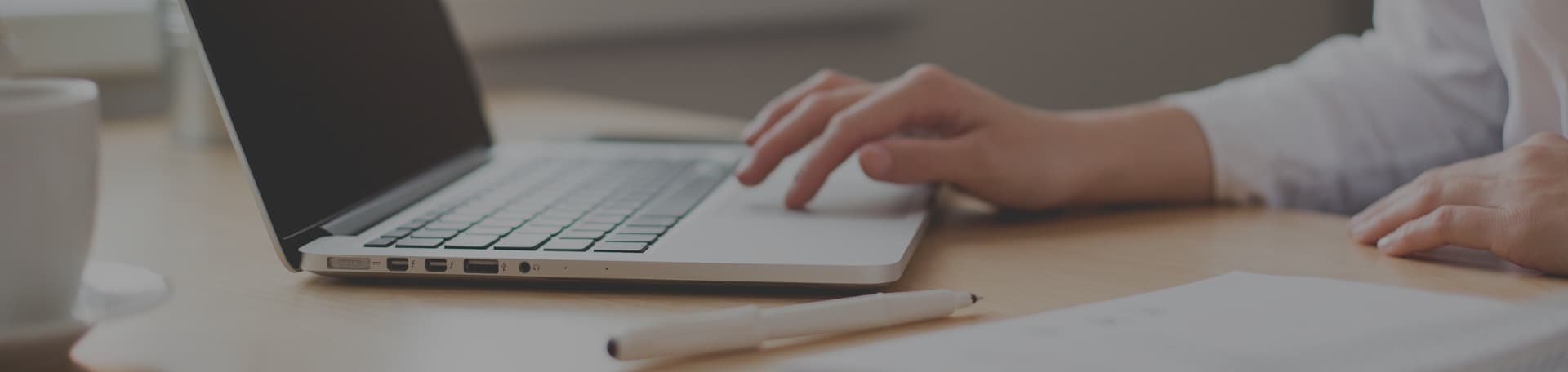
Slewing Bearing: The Basics You Need to Know
Slewing Bearing: The Basics You Need to Know
If you are in the market for a reliable bearing that can handle heavy loads and rotational movements, then you might want to consider a slewing bearing. Slewing bearings, also known as turntable bearings, are designed to support slow-turning or slowly-oscillating loads in combination, such as axial, radial, and moment loads. They are commonly used in various applications, including wind turbines, tunnel boring machines, cranes, and more.

Slewing bearings are essentially large-sized bearings that can accommodate oscillating movements and withstand extreme tilting loads. They are compact, economical, and can replace multi-bearing configurations for continuous casting processes. Slewing bearings come in different designs, with outside diameters ranging from 0.1 to 18 meters, and can be customized to meet specific requirements. If you need advanced engineering and remanufacturing services, then SKF is one of the leading providers of standard and customized slewing bearings on the market.
Whether you are looking for a slewing bearing for a new project or need to replace an existing one, it is important to choose a high-quality product that can withstand the rigors of your application. Emerson Bearing is another provider of top-quality slewing ring bearings that can support heavy loads and power transmission in all directions. To learn more about the types, applications, and features of different series of slewing ring bearings, check out their website.
Fundamentals of Slewing Bearings

Slewing bearings are large-sized bearings that can accommodate axial, radial, and moment loads. They are commonly used in heavy-duty applications, such as cranes, excavators, wind turbines, and industrial machinery.
Design Principles
The design of slewing bearings is based on four main principles: load carrying capacity, stiffness, operational reliability, and ease of installation and maintenance.
Load carrying capacity is the ability of the bearing to support the weight of the equipment and the loads it carries. Slewing bearings are designed to withstand high loads and provide smooth rotation.
Stiffness is the ability of the bearing to resist deformation under load. Slewing bearings are designed to be stiff to ensure accurate positioning and prevent damage to the equipment.
Operational reliability is the ability of the bearing to perform under harsh conditions, such as high temperatures, heavy loads, and vibration. Slewing bearings are designed to be durable and reliable, even in extreme conditions.
Ease of installation and maintenance is important for reducing downtime and maintenance costs. Slewing bearings are designed to be easy to install and maintain, with features such as bolt holes, grease fittings, and seals.
Core Components
Slewing bearings consist of several core components, including the outer ring, inner ring, rolling elements, and cage. The outer ring is fixed to the equipment, while the inner ring rotates with the load. The rolling elements, such as balls or rollers, provide the load carrying capacity and allow for smooth rotation. The cage holds the rolling elements in place and prevents them from colliding with each other.
Slewing bearings can be customized to meet the specific needs of different applications. They come in a variety of sizes, materials, and configurations, such as single-row, double-row, and three-row designs. The choice of slewing bearing depends on factors such as load capacity, stiffness, operating conditions, and installation requirements.
In summary, slewing bearings are an essential component of heavy-duty machinery. They are designed to provide high load carrying capacity, stiffness, operational reliability, and ease of installation and maintenance. The core components of slewing bearings include the outer ring, inner ring, rolling elements, and cage.
Applications of Slewing Bearings

Slewing bearings are used in a wide range of applications across various industries due to their ability to support controlled rotation and manage heavy loads. Here are some of the notable applications:
Industrial Machinery
Slewing bearings are used in various types of industrial machinery, such as excavators, cranes, and robots. They enable rotational movement between two components while supporting heavy loads and providing stability. Slewing bearings are also used in tunnel boring machines, which are used to excavate tunnels for transportation and infrastructure projects.
Wind Turbines
Slewing bearings are crucial components in wind turbines, which are used to generate electricity from wind energy. They enable the rotation of the turbine blades to capture wind energy and convert it into electrical energy. Slewing bearings used in wind turbines are designed to handle high axial and radial loads and provide long service life.
Medical Equipment
Slewing bearings are used in medical equipment, such as CT scanners and X-ray machines, to ensure precise positioning and rotational movement. They enable the precise movement of the equipment, which is crucial for accurate diagnosis and treatment. Slewing bearings used in medical equipment are designed to provide smooth and accurate movement while ensuring patient safety.
Overall, slewing bearings find a wide range of applications across various industries due to their ability to support controlled rotation and manage heavy loads. Understanding their components, applications, and standards is crucial for selecting the right slewing bearing for a specific application. Ensuring proper installation, maintenance, and lubrication is also essential for maximizing the service life of slewing bearings.
Manufacturing Processes
Slewing bearings are complex components that require a highly specialized manufacturing process. In this section, we will discuss the three main manufacturing processes that are involved in creating a high-quality slewing bearing.
Forging and Machining
The first step in creating a slewing bearing is forging the raw materials into the desired shape. This process involves heating the metal to a high temperature and then shaping it using a press or hammer. Once the raw materials have been forged, they are machined to the precise dimensions required for the bearing. This step involves using a lathe, milling machine, or other specialized equipment to remove excess material and create the necessary features.
Heat Treatment
After the raw materials have been forged and machined, they undergo a heat treatment process to improve their strength and durability. This process involves heating the metal to a specific temperature and then cooling it rapidly to create a hardened surface layer. The heat treatment process can also be used to adjust the internal structure of the metal to improve its mechanical properties.
Quality Control
The final step in the manufacturing process is quality control. This step involves inspecting the slewing bearing to ensure that it meets the required specifications and standards. Quality control measures may include visual inspections, dimensional measurements, and non-destructive testing techniques such as ultrasonic testing or magnetic particle inspection.
In summary, the manufacturing process for slewing bearings involves forging and machining the raw materials, heat treating the components to improve their strength and durability, and performing rigorous quality control checks to ensure that the finished product meets the required specifications.
Installation and Maintenance
When it comes to installing and maintaining your slewing bearing, there are some important guidelines to follow. By taking proper care of your slewing bearing, you can ensure that it lasts for a long time and performs optimally. In this section, we will discuss the installation and maintenance of your slewing bearing.
Installation Guidelines
To install your slewing bearing, follow these guidelines:
- Check the bearing for physical damage before installation.
- Lift the bearing with eye bolts and ensure that the eye bolts are fully threaded into the bolt hole.
- Mount the bearing in an unloaded condition.
- Clean the mounting surfaces on the structure and the bearing.
- Ensure that the bearing mounting surfaces are machined flat after all welding and stress relief treatment on the structures is complete.
Maintenance Strategies
To maintain your slewing bearing, follow these strategies:
- Regularly inspect the bearing for signs of wear, damage, or corrosion.
- Lubricate the bearing according to the manufacturer’s recommendations.
- Clean the bearing and its surrounding area to prevent contamination.
- Regularly check the bolts and nuts for proper torque.
- Monitor the bearing’s performance and address any issues promptly.
Troubleshooting Common Issues
If you encounter any issues with your slewing bearing, here are some common problems and their solutions:
- Excessive noise: Check the bearing for damage or contamination. Lubricate the bearing if necessary.
- Vibration: Check the bearing for misalignment or damage. Adjust the mounting if necessary.
- Overheating: Check the lubrication system and ensure that the bearing is properly lubricated. Check for any contamination or damage to the bearing.
- Irregular wear: Check the bearing for misalignment or damage. Adjust the mounting if necessary.
Market Trends and Future Outlook
If you’re interested in the slewing bearing market, you’ll be pleased to know that the market is poised for growth in the coming years. According to a report by The Insight Partners, the global slewing bearing market size demand is expected to reach US$ 5,831.2 million by 2028, expanding at a CAGR of 5.4% from 2021 to 2028. Similarly, a report by Data Bridge Market Research predicts the market will witness a 5.90% CAGR worth $ 6742.80 million by 2030.
One of the key drivers of growth in the slewing bearing market is the increasing demand from the renewable energy sector. As governments around the world commit to reducing carbon emissions and transitioning to clean energy, the demand for wind turbines and solar panels is growing. Slewing bearings are essential components in these systems, and as a result, the demand for slewing bearings is increasing.
Another trend in the slewing bearing market is the growing demand for customized solutions. As companies look to optimize their operations and reduce costs, they are turning to customized slewing bearings that are designed to meet their specific needs. This trend is expected to continue in the coming years, as companies seek to differentiate themselves in an increasingly competitive market.
Finally, the slewing bearing market is also being driven by technological advancements. As new materials and manufacturing techniques are developed, slewing bearings are becoming more durable, efficient, and cost-effective. This is allowing companies to improve the performance of their equipment while reducing maintenance costs.
Overall, the future looks bright for the slewing bearing market, with strong demand from the renewable energy sector, growing demand for customized solutions, and ongoing technological advancements driving growth.