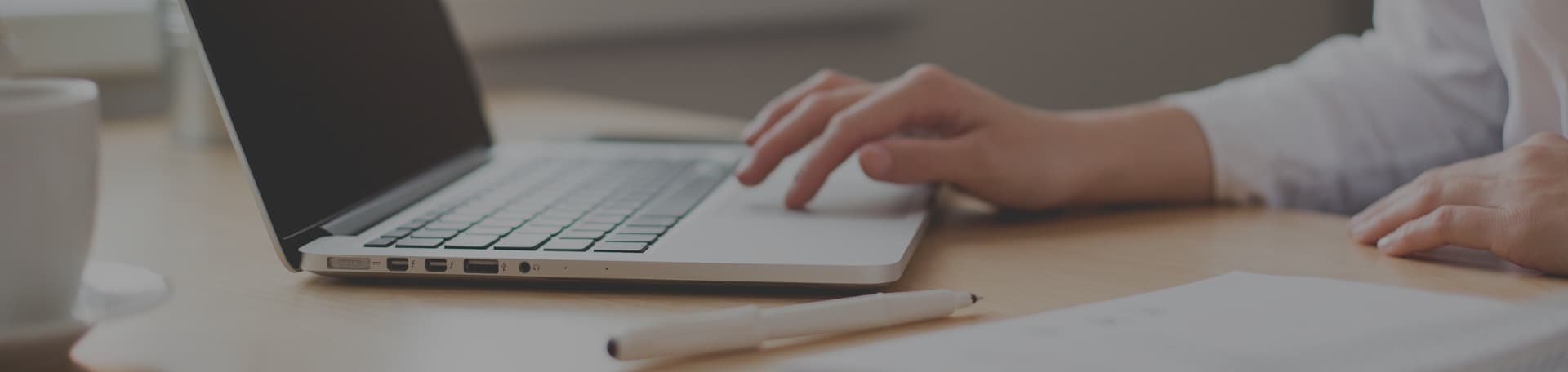
Slewing Bearing Factory: A Comprehensive Guide to Manufacturing and Applications
Slewing Bearing Factory: A Comprehensive Guide to Manufacturing and Applications
If you are in need of slewing bearings for your manufacturing project, you may want to consider purchasing from a slewing bearing factory. These factories specialize in producing high-quality slewing bearings that can withstand heavy loads and provide smooth rotation. With their advanced machinery and experienced technicians, they are able to produce bearings in a wide range of sizes and specifications to meet your specific needs.

When choosing a slewing bearing factory, it is important to consider factors such as their production capacity, quality control measures, and reputation in the industry. You may also want to look for a factory that offers customization options, such as the ability to add gears or other features to your bearings. By working with a reputable slewing bearing factory, you can ensure that your project will have the reliable and durable bearings it needs to operate smoothly and efficiently.
Overall, a slewing bearing factory can be a valuable resource for those in need of high-quality bearings for their manufacturing projects. By doing your research and choosing a factory that meets your specific needs, you can ensure that your project will have the reliable and durable bearings it needs to succeed.
Overview of Slewing Bearings

Slewing bearings are an essential component in machinery, enabling the smooth and controlled rotation of heavy loads. These bearings play a pivotal role in various industries, ranging from construction and manufacturing to renewable energy and robotics.
Design and Functionality
Slewing bearings are large-sized bearings specifically designed to accommodate oscillating movements. They are comprised of an inner ring and an outer ring, one of which usually incorporates a gear. The bearing raceways, in conjunction with the rolling elements (and cages or spacers), are designed to accommodate loads, acting singly or in combination, and in any direction.
Types of Slewing Bearings
There are several types of slewing bearings, including four-point contact ball bearings, double-row ball bearings, cross roller bearings, and three-row roller bearings. Four-point contact ball bearings are the most common type of slewing bearings, and they can handle both axial and radial loads. Double-row ball bearings are suitable for applications requiring high rigidity and precision. Cross roller bearings are best suited for applications requiring high rotational accuracy and rigidity. Three-row roller bearings are used for applications requiring high load-carrying capacity and high axial and radial stiffness.
Applications in Industry
Slewing bearings are used in a wide range of applications, including cranes, excavators, wind turbines, solar trackers, and robotics. In cranes and excavators, slewing bearings are used to rotate the boom and the arm. In wind turbines, slewing bearings are used to rotate the nacelle and the blades. In solar trackers, slewing bearings are used to rotate the solar panels. In robotics, slewing bearings are used to rotate the joints. Slewing bearings are also used in medical equipment, military equipment, and aerospace applications.
In summary, slewing bearings are a critical component in machinery that enables the smooth and controlled rotation of heavy loads. They come in various types and are used in a wide range of applications across different industries.
Manufacturing Process

When it comes to the manufacturing process of slewing bearings, there are several key steps involved. These steps are essential to ensure that the final product is of high quality and meets the required specifications. In this section, we will discuss the various steps involved in the manufacturing process of slewing bearings.
Raw Material Selection
The first step in the manufacturing process of slewing bearings is the selection of raw materials. The choice of raw materials is critical as it determines the quality and durability of the final product. High-quality materials such as alloy steel, carbon steel, and stainless steel are typically used in the manufacturing process of slewing bearings.
Forging and Heat Treatment
The next step in the manufacturing process of slewing bearings is forging and heat treatment. During the forging process, the raw materials are shaped into the desired shape using a hydraulic press. Heat treatment is then carried out to improve the mechanical properties of the materials. This involves heating the materials to a specific temperature and then cooling them in a controlled manner.
Machining and Finishing
After forging and heat treatment, the materials are then machined to the required size and shape. This involves using precision tools such as lathes, milling machines, and grinders. The final step in the manufacturing process is finishing. This involves polishing the surfaces of the materials to improve their appearance and protect them from corrosion.
Quality Control and Testing
Quality control and testing are critical steps in the manufacturing process of slewing bearings. The products are thoroughly inspected to ensure that they meet the required specifications. This involves testing for factors such as load capacity, wear resistance, and corrosion resistance. The products are also subjected to various tests such as ultrasonic testing, magnetic particle testing, and dye penetrant testing to ensure that they are free from defects.
In conclusion, the manufacturing process of slewing bearings involves several key steps, including raw material selection, forging and heat treatment, machining and finishing, and quality control and testing. By following these steps, manufacturers can ensure that the final product is of high quality and meets the required specifications.
Slewing Bearing Factory Infrastructure
When it comes to manufacturing slewing bearings, a well-designed infrastructure is crucial to ensure high-quality products. In this section, we will discuss the key aspects of a typical slewing bearing factory infrastructure.
Production Lines
Slewing bearing factories usually have multiple production lines to meet the demand for different types and sizes of bearings. The production lines are designed to handle the entire manufacturing process, from raw material preparation to final assembly.
Each production line is manned by a team of skilled workers who are responsible for ensuring that the production process runs smoothly. The workers are trained to operate the machinery and equipment used in the production process, as well as to maintain them.
Automation and Robotics
To improve efficiency and reduce costs, many slewing bearing factories are now incorporating automation and robotics into their production processes. This allows for faster and more accurate manufacturing, as well as reducing the need for human intervention.
For example, automated machines can perform tasks such as cutting, drilling, and grinding with greater precision and speed than human workers. Robotics can also be used for tasks such as material handling, assembly, and quality control.
Facility Layout
The layout of a slewing bearing factory is carefully designed to optimize the flow of materials and products through the production process. The layout takes into account factors such as the size and shape of the facility, the location of machinery and equipment, and the movement of workers and materials.
The facility layout is also designed to ensure safety and efficiency. For example, machinery and equipment are positioned to minimize the risk of accidents, and workers are provided with the necessary safety equipment and training.
In conclusion, a well-designed infrastructure is essential for a slewing bearing factory to produce high-quality products efficiently and safely. By incorporating automation and robotics, factories can further optimize their production processes and reduce costs.
Supply Chain and Distribution
Logistics and Transportation
When it comes to logistics and transportation, it is important to ensure that the slewing bearings are transported safely and efficiently. This is why our factory works with reliable logistics partners that have experience in handling heavy and large-sized bearings. We have established a well-organized transportation network that covers both domestic and international shipping. Our logistics team is responsible for coordinating the delivery of our products to our customers’ locations.
We use various modes of transportation, such as sea, air, and land, to ensure that our customers receive their orders on time. Our team tracks the movement of each shipment and provides regular updates to our customers. This helps us to keep our customers informed about the status of their orders and ensures that they receive their products within the promised timeframe.
Inventory Management
At our slewing bearing factory, we understand the importance of inventory management. We have implemented a state-of-the-art inventory management system that allows us to track the movement of our products in real-time. This helps us to maintain accurate inventory levels and avoid stockouts.
We have a large warehouse where we store our products. Our warehouse is organized in a way that allows us to easily locate and retrieve the products when needed. We regularly conduct physical inventory checks to ensure that our inventory levels match our records.
In addition, we work closely with our suppliers to ensure that we receive our raw materials on time. This helps us to avoid any delays in our production process and ensure that we can meet the demand for our products.
Overall, our focus on logistics and inventory management helps us to ensure that our customers receive high-quality slewing bearings on time.
Challenges and Solutions
Maintaining Precision
Maintaining precision in the manufacturing process of slewing bearings is crucial to ensure their proper functioning. However, there are several challenges associated with lubricating slewing bearings that require careful consideration and effective solutions. High loads and torque often lead to increased friction and wear. To mitigate this, proper lubrication and maintenance are essential. You can use a variety of lubricants, including grease, oil, and solid film lubricants. Solid film lubricants are ideal for applications with high loads and low speeds, while grease is best suited for applications with low loads and high speeds.
Customization and Retrofitting
Customization and retrofitting are important to meet the specific needs of different applications. Slewing bearings come in various designs, sizes, and materials. Some common materials used in manufacturing slewing bearings include carbon steel, alloy steel, and stainless steel. When selecting a material, consider the application’s requirements, such as load capacity, corrosion resistance, and environmental factors. Retrofitting is also an important aspect of slewing bearing maintenance, as it can extend the life of the bearing and improve its performance. Retrofitting can include replacing the bearing’s seals, lubrication system, and other components.
Environmental Compliance
Environmental compliance is an important consideration in the manufacturing process of slewing bearings. Compliance with environmental regulations helps to reduce the impact of manufacturing on the environment and ensure the safety of workers. Some common environmental regulations that slewing bearing factories must comply with include waste disposal, air emissions, and water pollution. To comply with these regulations, slewing bearing factories can implement measures such as recycling, waste reduction, and pollution control.
In conclusion, maintaining precision, customization and retrofitting, and environmental compliance are some of the key challenges faced by slewing bearing factories. By addressing these challenges with effective solutions, slewing bearing factories can ensure the optimal performance and longevity of their products while minimizing their impact on the environment.