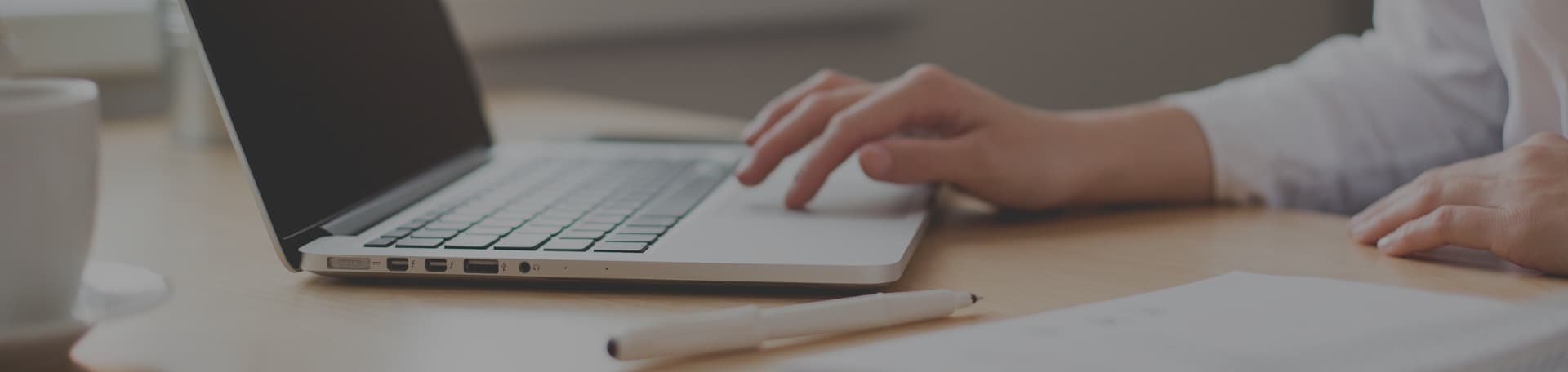
Slewing Bearing for Wind Turbine: A Comprehensive Guide
Slewing Bearing for Wind Turbine: A Comprehensive Guide
If you’re familiar with wind turbines, you may have heard of slewing bearings. Slewing bearings are critical components of wind turbines that allow the nacelle and blades to adjust to optimize aerodynamic power capture. These bearings are designed to withstand high loads and ensure that the rotor can rotate steadily around its own axis.

Slewing bearings are typically found in the blade/yaw bearings of wind turbines. These bearings are responsible for adjusting the angle of the blades to capture the maximum amount of wind energy. If the slewing bearings fail, it can cause serious consequences such as pitching failure, low energy output, and current instability.
In this article, we’ll explore the importance of slewing bearings in wind turbines, how they work, and the different types of slewing bearings available. We’ll also take a look at some of the challenges associated with designing and manufacturing slewing bearings for wind turbines. By the end of this article, you’ll have a better understanding of the role that slewing bearings play in wind energy and the challenges associated with their design and manufacture.
Fundamentals of Slewing Bearings

Slewing bearings are critical components of wind turbines that enable the nacelle and blades to adjust to optimize aerodynamic power capture. These bearings are designed to transmit axial, radial, and moment loads between two or more rotating components. In this section, we will explore the design principles and core components of slewing bearings.
Design Principles
The design of slewing bearings is based on the principles of contact mechanics, which determine the stresses and deformations that occur at the contact points between the rolling elements and raceways. The design process involves selecting the appropriate bearing type, size, and material to meet the specific load and performance requirements of the application.
Slewing bearings can be classified into two main types: ball and roller bearings. Ball bearings are used for light to moderate loads and speeds, while roller bearings are used for heavier loads and higher speeds. The most common types of roller bearings used in wind turbines are cylindrical, tapered, and spherical roller bearings.
Core Components
The core components of slewing bearings include the inner and outer rings, rolling elements, and cage. The inner and outer rings are made of high-strength steel and are designed to support the loads transmitted through the bearing. The rolling elements are placed between the inner and outer rings and are responsible for transmitting the loads. The most common types of rolling elements used in slewing bearings are balls and rollers.
The cage is used to separate and guide the rolling elements, preventing them from coming into contact with each other. It also helps to distribute the load evenly across the rolling elements. The cage is typically made of steel or plastic and is designed to withstand the loads and speeds of the application.
In summary, slewing bearings are critical components of wind turbines that enable the nacelle and blades to adjust to optimize aerodynamic power capture. The design of these bearings is based on the principles of contact mechanics, and their core components include the inner and outer rings, rolling elements, and cage.
Application in Wind Turbines
Slewing bearings are essential components in wind turbines, and they play a crucial role in the energy generation process. They help to transmit the forces of the wind to the entire wind turbine. This section will discuss the application of slewing bearings in wind turbines, focusing on their load handling and rotation functionality.
Load Handling
Slewing bearings are used in wind turbines to handle various loads, including radial, axial, and tilting moment loads. These bearings are designed to withstand high loads and provide reliable performance under harsh conditions. The load handling capacity of a slewing bearing is determined by its size, material, and design.
The yaw bearing, which is a four-point contact ball slewing bearing, is responsible for handling the axial and tilting moment loads. On the other hand, the pitch bearing, which is a double-row ball slewing bearing, is responsible for handling the radial loads. These bearings are designed to rotate smoothly and transmit torque to achieve the wind turbine yaw and pitch movement.
Rotation Functionality
Slewing bearings are also used in wind turbines to provide rotation functionality. The yaw bearing is responsible for rotating the nacelle and the rotor blades. It allows the wind turbine to face the wind and capture the maximum amount of energy. The pitch bearing, on the other hand, is responsible for adjusting the angle of the rotor blades. It allows the wind turbine to optimize its performance and generate more energy.
The rotation functionality of slewing bearings is critical to the operation of wind turbines. They must rotate smoothly and accurately to ensure that the wind turbine operates efficiently. The design of these bearings is crucial in achieving this goal. They must be precisely engineered to provide reliable performance under harsh conditions.
In conclusion, slewing bearings play a critical role in the operation of wind turbines. They are responsible for handling various loads and providing rotation functionality. The design of these bearings is crucial in ensuring that wind turbines operate efficiently and generate the maximum amount of energy.
Manufacturing Process
When it comes to manufacturing slewing bearings for wind turbines, there are two main aspects to consider: materials selection and fabrication techniques.
Materials Selection
The materials used to manufacture slewing bearings for wind turbines must be carefully selected to ensure that they can withstand the harsh operating conditions of wind turbines. Common materials used for slewing bearings include high-strength steels, aluminum alloys, and copper alloys. These materials are chosen for their high strength, durability, and resistance to corrosion.
Fabrication Techniques
The fabrication of slewing bearings for wind turbines is a complex process that involves several different techniques. These techniques include forging, heat treatment, machining, and assembly. The fabrication process begins with the selection of the appropriate materials, which are then forged into the desired shape. After forging, the bearings undergo a heat treatment process to improve their strength and durability.
Once the heat treatment process is complete, the bearings are machined to achieve the required dimensions and tolerances. Finally, the bearings are assembled, which involves the installation of seals, lubrication systems, and other components.
Overall, the manufacturing process for slewing bearings for wind turbines requires a high level of precision and expertise. By carefully selecting materials and using advanced fabrication techniques, manufacturers can produce high-quality bearings that can withstand the extreme operating conditions of wind turbines.
Maintenance and Lifespan
Slewing bearings are critical components of wind turbines that require regular maintenance to ensure their longevity and reliability. Proper maintenance can help extend the lifespan of slewing bearings, reducing the need for costly replacements and downtime.
Regular Inspections
Regular inspections of slewing bearings should be conducted to identify any signs of wear or damage. Inspections should include visual inspections, vibration analysis, and temperature monitoring. Visual inspections can help identify any signs of wear or damage to the bearing, such as cracks, pitting, or corrosion. Vibration analysis can detect any abnormalities in the bearing’s operation, such as excessive vibration or noise. Temperature monitoring can help identify any overheating issues, which can be a sign of bearing failure.
Replacement Strategies
If a slewing bearing is found to be damaged or worn during an inspection, it should be replaced as soon as possible to prevent further damage. Replacement strategies should be based on the condition of the bearing, the severity of the damage, and the expected lifespan of the replacement bearing.
One approach to replacement is to use a predictive maintenance strategy, which involves monitoring the condition of the bearing over time and replacing it before it fails. This approach can help reduce the risk of unexpected downtime and minimize the cost of replacements.
Another approach is to use a preventive maintenance strategy, which involves replacing the bearing at regular intervals, regardless of its condition. This approach can help ensure that the bearing is always in good condition and reduce the risk of unexpected failures.
In conclusion, regular inspections and appropriate replacement strategies are essential for maintaining the lifespan and reliability of slewing bearings in wind turbines. By following these maintenance practices, you can help ensure that your wind turbine operates efficiently and reliably, reducing downtime and maintenance costs.
Innovations and Advancements
Material Improvements
Slewing bearings are an essential component of wind turbines that transmit the forces of the wind to the entire structure. As a result, they are subjected to heavy loads, extreme temperatures, and harsh environmental conditions. Recent innovations in material science have led to the development of new materials that can withstand these challenging conditions more effectively.
For instance, the use of high-performance steels, such as 100Cr6, has significantly improved the wear resistance and fatigue strength of slewing bearings. These steels are also more resistant to corrosion, which is a common problem in offshore wind farms. Moreover, the use of advanced coatings, such as DLC (Diamond-like Carbon), has further enhanced the performance of slewing bearings by reducing friction, wear, and noise.
Engineering Developments
Apart from material improvements, there have been significant advancements in the design and engineering of slewing bearings for wind turbines. One of the most notable developments is the use of segmented slewing bearings, which consist of several smaller rings instead of a single large one. This design allows for easier maintenance and replacement of individual segments, reducing downtime and maintenance costs.
Another important development is the use of integrated sensors and monitoring systems that can detect and diagnose potential problems in real-time. These systems can provide valuable data on the performance and health of the slewing bearings, allowing for predictive maintenance and optimization of the wind turbine’s operation.
Overall, these innovations and advancements in material science and engineering have significantly improved the performance, reliability, and durability of slewing bearings for wind turbines. As a result, they have become an essential component of modern wind turbines, contributing to the growth and sustainability of the renewable energy industry.