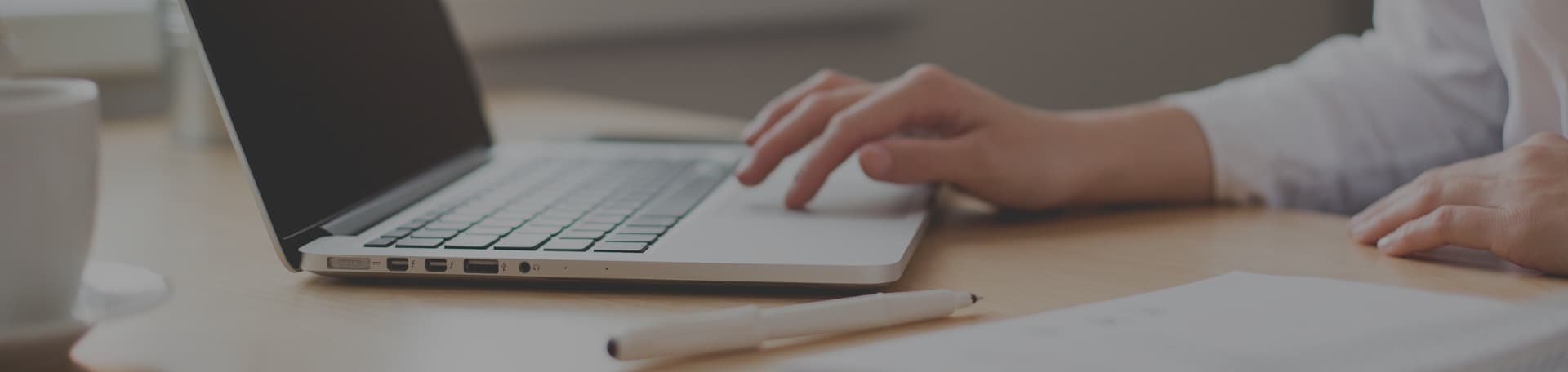
Slewing Bearing with Internal Gear: A Comprehensive Guide
Slewing Bearing with Internal Gear: A Comprehensive Guide
If you are looking for a versatile and robust bearing solution for your application, a slewing bearing with internal gear might be the perfect choice. These bearings have a gear mechanism integrated into their structure, usually on the inner ring. The internal gears engage with a pinion or other driving mechanism to control and drive the bearing’s movement.

Slewing bearings with internal gears are commonly used in applications where precise positioning and power transmission are critical. They are ideal for applications that require high torque, such as cranes, excavators, and wind turbines. These bearings can handle axial, radial, and moment loads, making them suitable for a wide range of applications. Additionally, the internal gear design provides a compact solution that saves space and reduces weight.
One of the main advantages of slewing bearings with internal gears is their ability to handle high loads. The gear mechanism distributes the load evenly across the bearing, reducing stress and increasing the bearing’s overall capacity. This design also allows for smoother operation and better control over the bearing’s movement. Overall, a slewing bearing with internal gear is a reliable and efficient solution for applications that require precise positioning and high torque.
Fundamentals of Slewing Bearings

Design Principles
Slewing bearings are designed to handle axial, radial, and moment loads. They consist of an inner and outer ring, with rolling elements in between. The rings are typically made of high-strength steel, while the rolling elements can be balls, rollers, or cylinders. The rolling elements are separated by a cage, which keeps them evenly spaced and prevents them from coming into contact with each other.
The design of a slewing bearing depends on the application it will be used in. Factors such as load capacity, speed, and operating temperature must be taken into account. Slewing bearings can be designed with internal or external gears, or with no gears at all. Internal gears are integrated into the bearing’s structure, usually on the inner ring. External gears are mounted on the outside of the bearing, and engage with a pinion or other driving mechanism.
Internal Gear Characteristics
Slewing bearings with internal gears have several advantages over those with external gears. Internal gears are more compact, which allows for a smaller overall bearing size. This can be important in applications where space is limited. Internal gears also provide better protection against environmental factors such as dirt and debris, which can cause damage to external gears.
Internal gears can be designed with a variety of characteristics, depending on the specific application. The gear teeth can be straight or helical, and can have different pressure angles and module sizes. The gear teeth can also be ground or hobbed, depending on the required precision. The gear teeth must be designed to provide smooth, reliable operation under a range of loads and speeds.
In conclusion, slewing bearings with internal gears are an important component in many heavy machinery applications. Their design must take into account factors such as load capacity, speed, and operating temperature. Internal gears provide several advantages over external gears, including a more compact size and better protection against environmental factors. The gear teeth must be designed to provide smooth, reliable operation under a range of loads and speeds.
Manufacturing Processes
Slewing bearings with internal gears are an essential component of various industrial applications, including construction, manufacturing, and robotics. These bearings are designed to withstand high loads and provide smooth rotation, making them a crucial element in many machines and equipment.
Forging and Machining
Manufacturing slewing bearings with internal gears involves several processes, starting with forging and machining. The first step is to forge the bearing rings, which involves shaping the metal into the desired shape and size. The forging process ensures that the metal is dense and free of defects, which is crucial for the bearing’s performance.
After forging, the bearing rings undergo machining, where the surfaces are finished to the required tolerances and surface roughness. The machining process involves cutting, drilling, and grinding the bearing surfaces to ensure that they are smooth and accurate. The accuracy of the machining process is critical to ensure that the internal gear fits precisely into the bearing ring.
Heat Treatment
Heat treatment is another critical process in manufacturing slewing bearings with internal gears. The heat treatment process involves heating the bearing rings to a specific temperature and then cooling them at a controlled rate. The heat treatment process helps to increase the bearing’s strength and durability, ensuring that it can withstand high loads and provide a long service life.
After heat treatment, the bearing rings undergo a final machining process to ensure that they meet the required tolerances and surface finish. The internal gear is then fitted into the bearing ring, and the bearing assembly is tested to ensure that it meets the required specifications.
In conclusion, manufacturing slewing bearings with internal gears involves several critical processes, including forging, machining, and heat treatment. These processes ensure that the bearings are strong, durable, and can withstand high loads, making them an essential component of various industrial applications.
Applications of Slewing Bearings with Internal Gears
Slewing bearings with internal gears are used in a variety of applications, including industrial machinery and wind turbines. Here are some examples of how these bearings are used.
Industrial Machinery
Slewing bearings with internal gears are often used in industrial machinery, such as cranes, excavators, and other heavy equipment. These bearings are designed to handle heavy loads and provide smooth, controlled rotation. They are also used in conveyor systems, where they help to transfer materials from one location to another.
In industrial machinery, slewing bearings with internal gears are often used in combination with other types of bearings, such as roller bearings and ball bearings. This helps to distribute the load evenly and reduce wear and tear on the bearings.
Wind Turbines
Slewing bearings with internal gears are also used in wind turbines. These bearings are used to support the weight of the rotor and provide smooth, controlled rotation. They are designed to handle heavy loads and withstand the harsh operating conditions of wind turbines.
In wind turbines, slewing bearings with internal gears are often used in combination with other types of bearings, such as cylindrical roller bearings and tapered roller bearings. This helps to distribute the load evenly and reduce wear and tear on the bearings.
Overall, slewing bearings with internal gears are an important component in many different types of machinery and equipment. They are designed to handle heavy loads and provide smooth, controlled rotation, making them an essential part of many industrial and wind turbine applications.
Installation and Maintenance
Mounting Procedures
When installing a slewing bearing with internal gear, it is important to follow proper mounting procedures to ensure optimal performance and longevity of the bearing. Before mounting the bearing, check for any physical damage and ensure that it is in an unloaded condition. The mounting surfaces must be machined flat after all welding and stress relief treatment on the structures is complete. If subsequent welding is necessary, it must be done before the bearing is mounted.
When lifting the bearing, use eye bolts and ensure that they are fully threaded into the bolt hole. Use a minimum thread engagement of 1.5 times the bolt diameter. The bearing should be lifted evenly and not twisted or dropped during installation. Once the bearing is in place, tighten the bolts to the recommended torque specifications. Do not overtighten the bolts as this can damage the bearing.
Lubrication and Inspection
Proper lubrication is essential for the smooth operation of a slewing bearing with internal gear. Before use, ensure that the bearing is properly lubricated with the recommended lubricant. The lubricant should be applied evenly to all gear teeth and contact surfaces. Check the lubricant level regularly and add more as needed.
Regular inspections are also important for the maintenance of a slewing bearing with internal gear. Inspect the bearing for any signs of wear or damage, such as cracks, corrosion, or pitting. Inspect the gear teeth for any signs of wear, chipping, or cracking. If any damage is found, the bearing should be replaced or repaired as soon as possible.
In summary, proper installation and maintenance are crucial for the optimal performance and longevity of a slewing bearing with internal gear. Follow proper mounting procedures, ensure proper lubrication, and perform regular inspections to ensure the bearing is operating smoothly and efficiently.