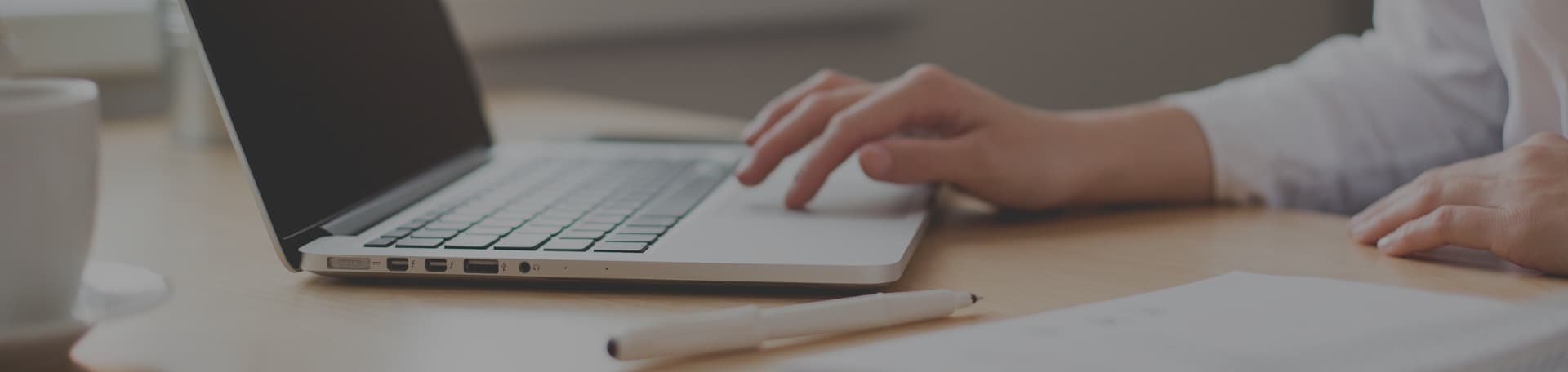
Slewing Bearings: What You Need to Know
Slewing Bearings: What You Need to Know
Slewing bearings are essential components in many industrial applications, such as cranes, excavators, wind turbines, and medical equipment. They allow for smooth and precise rotation of heavy loads, reducing friction and wear between moving parts. Sleeve bearings, also known as plain bearings, are a type of slewing bearing that have a simple design and are easy to install and maintain. In this article, you will learn about the fundamentals of sleeve bearings, the different types available, their applications, and how to install and maintain them.

Sleeve bearings consist of two main components: a stationary sleeve and a rotating shaft. The sleeve is typically made of a low-friction material, such as bronze or plastic, and the shaft is made of a harder material, such as steel. The sleeve and shaft are separated by a thin film of lubricant, which reduces friction and wear between the two surfaces. Sleeve bearings are self-lubricating, which means they do not require external lubrication systems, making them a cost-effective solution for many applications.
Key Takeaways
- Sleeve bearings are a type of slewing bearing that allow for smooth and precise rotation of heavy loads.
- They consist of a stationary sleeve and a rotating shaft separated by a thin film of lubricant.
- Sleeve bearings are self-lubricating and require minimal maintenance, making them a cost-effective solution for many industrial applications.
Fundamentals of Sleeve Bearings

Sleeve bearings are a type of bearing that uses a single ring to house a number of small cylinders filled with oil or grease. They are commonly used in various industrial applications, including pumps, motors, and fans. In this section, we will discuss the design principles and material selection for sleeve bearings.
Design Principles
The design of sleeve bearings is based on the principle of hydrodynamic lubrication. This means that the bearing relies on a thin film of lubricant to separate the moving surfaces and reduce friction. The lubricant is typically oil or grease, which is stored in the small cylinders inside the bearing. When the bearing rotates, the lubricant is drawn into the gap between the shaft and the bearing surface, creating a hydrodynamic wedge that supports the load.
The design of the bearing is critical to its performance. The clearance between the shaft and the bearing surface, the size and shape of the lubricant pockets, and the material properties all play a role in determining the bearing’s load capacity, friction, and wear characteristics. The bearing must be designed to withstand the operating conditions, including the speed, temperature, and load.
Material Selection
The material selection for sleeve bearings is based on the application requirements. The most common materials used for sleeve bearings are bronze, copper, and acetal. Bronze is a popular choice for high-load applications, as it has good wear resistance and can withstand high temperatures. Copper is often used for low-load applications, as it has good thermal conductivity and is easy to machine. Acetal is a plastic material that is used for low-friction applications, as it has good wear resistance and low coefficient of friction.
Other factors that influence the material selection include the chemical compatibility with the lubricant, the cost, and the availability. The material must also be compatible with the shaft material, as dissimilar metals can cause galvanic corrosion.
In summary, sleeve bearings are a critical component in various industrial applications. The design and material selection are key factors in determining the bearing’s performance and reliability. By understanding the fundamentals of sleeve bearings, you can make informed decisions when selecting and designing bearings for your applications.
Types of Sleeve Bearings

When it comes to sleeve bearings, there are several types to choose from depending on your specific needs. In this section, we’ll take a closer look at three common types of sleeve bearings: plain, flanged, and thrust sleeve bearings.
Plain Sleeve Bearings
Plain sleeve bearings, also known as bushings, are the simplest type of sleeve bearings. They consist of a cylindrical metal sleeve that fits around a shaft and provides a sliding surface for the shaft to rotate on. Plain sleeve bearings are commonly made from materials such as bronze, copper, or acetal, and are often used in applications where low friction and high accuracy are required.
Flanged Sleeve Bearings
Flanged sleeve bearings are similar to plain sleeve bearings, but with an added flange on one end. This flange helps to keep the bearing in place and prevents it from sliding out of position. Flanged sleeve bearings are commonly used in applications where the bearing needs to be secured in place, such as in a housing or on a shaft that is not perfectly aligned.
Thrust Sleeve Bearings
Thrust sleeve bearings are designed to handle axial loads, which are loads that act parallel to the axis of the shaft. These bearings consist of a flat washer-like sleeve that fits between two other components, such as a shaft and a housing. Thrust sleeve bearings are commonly used in applications where there is a need to support heavy axial loads, such as in gearboxes or other power transmission systems.
Overall, sleeve bearings are a versatile type of bearing that can be used in a wide range of applications. By choosing the right type of sleeve bearing for your needs, you can ensure that your equipment operates smoothly and efficiently.
Applications
Slewing bearings find a wide range of applications across various industries due to their ability to support controlled rotation and manage heavy loads. Some notable applications include:
Industrial Machinery
Slewing bearings are integral components in cranes, excavators, and concrete pumps, enabling smooth and stable movement of heavy machinery. They are also used in wind turbines, where they support the rotation of the blades. Slewing bearings are also used in tunnel boring machines, where they enable the cutter head to rotate while maintaining a stable position.
Automotive Systems
Slewing bearings are used in various automotive systems, including steering systems, suspension systems, and gearboxes. In steering systems, they allow the steering column to rotate, while in suspension systems, they allow the wheels to rotate while maintaining a stable position. In gearboxes, they support the rotation of gears while maintaining proper alignment.
Aerospace Equipment
Slewing bearings are used in various aerospace equipment, including satellite dishes, radar systems, and telescopes. In satellite dishes, they enable the dish to rotate and track satellites, while in radar systems, they allow the antenna to rotate while maintaining a stable position. In telescopes, they support the rotation of the telescope while maintaining precise alignment.
Overall, slewing bearings are essential components in various industries, enabling controlled rotation and supporting heavy loads.
Installation and Maintenance
Installation Procedures
When installing a slewing bearing, it is important to first check for any physical damage. Lift the bearing with eye bolts, ensuring they are fully threaded into the bolt hole. Use a minimum thread engagement of 1.5 times the bolt diameter. The slew bearings shall be mounted in an unloaded condition. The mounting surfaces must be machined flat after all welding and stress relief treatment on the structures is complete. If subsequent welding is necessary, it must be done before the bearing is installed.
Lubrication and Maintenance
Proper lubrication is essential to ensure the longevity and proper functioning of a slewing bearing. The bearings must be lubricated at regular intervals, as specified by the manufacturer. There are three places which need to be lubricated: the slewing ring raceway, the screw worm, and the bearings. Grease nipples are located on the unit for easy access.
It is important to use the recommended type and amount of lubricant, as specified by the manufacturer. Over-lubrication can lead to overheating and premature failure, while under-lubrication can cause excessive wear and damage to the bearings. Always refer to the manufacturer’s guidelines for proper lubrication and maintenance procedures.
Regular maintenance is also important to ensure the continued performance of the slewing bearing. Check for any signs of wear or damage, and replace any parts as necessary. Keep the bearing clean and free from debris, and inspect it regularly for signs of corrosion or other damage. By following these guidelines, you can ensure that your slewing bearing will provide reliable and long-lasting performance.
Common Issues and Solutions
Slewing bearings are critical components in various applications, including heavy machinery, cranes, excavators, wind turbines, and more. Proper installation, maintenance, and timely problem resolution are essential for ensuring optimal performance and longevity of slewing bearings. Here are some common issues and solutions to keep in mind:
Wear and Fatigue
One of the most common problems with slewing bearings is wear and fatigue. Over time, rolling elements and tracks will show signs of wear and tear due to the constant friction and heavy loads they are subjected to. This can lead to a decrease in performance and, in severe cases, complete failure of the bearing.
To prevent this, it is important to regularly inspect the bearing for signs of wear. If you notice any damage or wear, it is recommended to replace the bearing as soon as possible. Additionally, proper lubrication can help reduce wear and extend the life of the bearing.
Misalignment and Seizure
Another common issue with slewing bearings is misalignment and seizure. This can occur when the bearing is not properly installed or maintained. Misalignment can cause excessive stress on the bearing, leading to premature failure. Seizure occurs when the bearing becomes stuck and cannot move freely.
To prevent misalignment, it is important to follow the manufacturer’s installation instructions carefully. Additionally, regular maintenance, including cleaning and lubrication, can help prevent seizure. If you notice any signs of misalignment or seizure, it is important to address the issue promptly to prevent further damage to the bearing or other components.
By addressing these common issues and following proper installation and maintenance procedures, you can ensure the optimal performance and longevity of your slewing bearings.