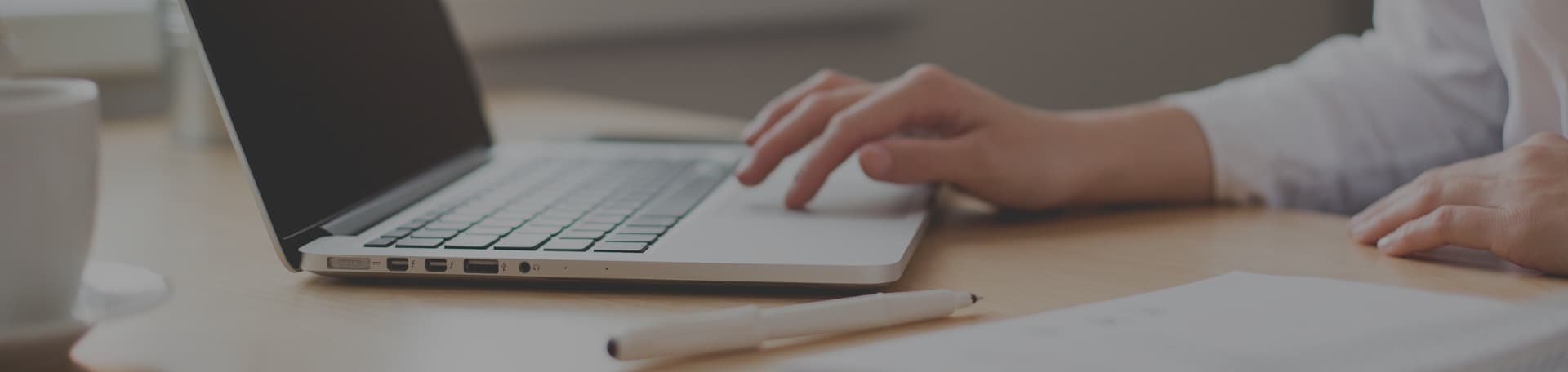
Wind Turbine Slewing Bearing: A Key Component for Efficient Wind Energy Generation
Wind Turbine Slewing Bearing: A Key Component for Efficient Wind Energy Generation
Wind turbines are an increasingly popular source of renewable energy, and they rely on a variety of complex components to function properly. One of the most important of these components is the slewing bearing, which plays a critical role in allowing the rotor blades to rotate and capture wind energy.

Slewing bearings are large, specialized bearings that are designed to support heavy loads and allow for rotational movement. In wind turbines, they are typically used in the yaw and pitch systems, which control the orientation and angle of the rotor blades. Without these bearings, wind turbines would be unable to function properly, and their ability to generate electricity would be severely compromised.
Given the critical importance of slewing bearings in wind turbines, it is essential to understand how they work and how they are designed. By exploring the key features and characteristics of these specialized bearings, you can gain a greater appreciation for the complexity and sophistication of wind turbine technology, as well as the challenges involved in designing and maintaining these powerful machines.
Design and Engineering

Components of a Slewing Bearing
A slewing bearing is a type of rotational bearing that is used to support heavy loads and facilitate movement in wind turbines. It consists of two main components: the outer ring and the inner ring. The outer ring is fixed to the wind turbine tower, while the inner ring is attached to the nacelle. The balls or rollers are sandwiched between the two rings, allowing for smooth rotation. Slewing bearings can be further classified into different subtypes, such as four-point contact ball bearings, double-row ball bearings, and cross-roller bearings, depending on their design.
Slewing Bearing Materials
Slewing bearings are typically made from high-strength materials, such as alloy steels, stainless steels, and non-ferrous metals. The choice of material depends on various factors, such as the operating conditions, load capacity, and durability requirements. For instance, alloy steels are commonly used for high-load applications, while stainless steels are preferred for their corrosion resistance properties. Non-ferrous metals, such as aluminum and bronze, are also used for their lightweight and self-lubricating characteristics.
Engineering Principles
The design and engineering of slewing bearings involve various principles, such as stress analysis, fatigue life calculation, and lubrication. The bearings must be able to withstand the loads and stresses that are generated during operation, while also maintaining their structural integrity over time. Fatigue life calculation is used to estimate the expected lifespan of the bearings under cyclic loading conditions. Lubrication is also critical for ensuring the smooth operation of the bearings and reducing wear and tear. Proper lubrication can help prevent premature failure and extend the lifespan of the bearings.
In summary, slewing bearings are critical components of wind turbines that enable smooth and reliable rotation. The design and engineering of these bearings involve careful consideration of various factors, such as the materials used, the loads and stresses involved, and the lubrication requirements. By understanding these principles, you can ensure that your wind turbine operates efficiently and effectively.
Manufacturing Process

Slewing bearings for wind turbines are manufactured using a series of steps that ensure their quality and durability. The manufacturing process consists of three main stages: forging and machining, heat treatment, and quality control.
Forging and Machining
The first step in the manufacturing process is forging and machining. This involves shaping the raw material into the desired shape and size. The raw material used for slewing bearings is typically high-quality steel, which is heated to a high temperature and then forged into the desired shape using a hydraulic press. Once the forging process is complete, the bearing is machined to achieve the required dimensions and tolerances. This step is critical to ensure that the bearing functions properly and can withstand the forces it will be subjected to.
Heat Treatment
The second step in the manufacturing process is heat treatment. This involves subjecting the bearing to a series of controlled heating and cooling cycles to improve its strength and durability. The heat treatment process is critical to ensure that the bearing can withstand the extreme forces and temperatures it will be subjected to during its lifetime. After the heat treatment process is complete, the bearing is inspected to ensure that it meets the required specifications.
Quality Control
The final step in the manufacturing process is quality control. This involves a series of tests and inspections to ensure that the bearing meets the required specifications and standards. The bearing is inspected for defects such as cracks, inclusions, and other imperfections that could compromise its performance. The bearing is also tested for its load-carrying capacity, stiffness, and other mechanical properties to ensure that it can withstand the forces it will be subjected to during its lifetime.
In conclusion, the manufacturing process for wind turbine slewing bearings is a complex and highly controlled process that involves a series of steps to ensure their quality and durability. The forging and machining, heat treatment, and quality control steps are critical to ensure that the bearings can withstand the extreme forces and temperatures they will be subjected to during their lifetime.
Installation and Maintenance
Installation Procedures
Proper installation of the wind turbine slewing bearing is crucial for the efficient functioning of the wind turbine. The installation process should be carried out by experienced and skilled professionals. The following steps should be taken during installation:
- Inspect the slewing bearing before installation and ensure that it is free from any damage or defects.
- Clean the mounting surface and mating parts thoroughly to remove any dirt or debris.
- Apply a thin layer of lubricant to the mating surfaces to reduce friction during installation.
- Ensure that the mounting bolts are tightened to the recommended torque settings.
- Verify that the slewing bearing is properly aligned and levelled before final tightening of the bolts.
Maintenance Strategies
Regular maintenance of the wind turbine slewing bearing is necessary to ensure its longevity and optimal performance. The following maintenance strategies should be employed:
- Regularly inspect the slewing bearing for any signs of wear, damage, or corrosion.
- Lubricate the slewing bearing according to the manufacturer’s recommendations.
- Monitor the temperature of the slewing bearing during operation to detect any abnormal heating.
- Maintain a log of all maintenance activities performed on the slewing bearing.
Troubleshooting Common Issues
Despite regular maintenance, issues may still arise with the wind turbine slewing bearing. The following are some common issues and their troubleshooting methods:
- Noise: If the slewing bearing produces unusual noise during operation, it may be due to inadequate lubrication or damaged raceways. Lubricate the bearing or replace it if necessary.
- Vibration: Excessive vibration may indicate misalignment or worn-out bearings. Check the alignment and replace the bearings if necessary.
- Overheating: If the temperature of the slewing bearing exceeds the recommended levels, it may be due to inadequate lubrication or excessive load. Lubricate the bearing or reduce the load if necessary.
By following these installation and maintenance procedures, you can ensure the smooth and efficient functioning of the wind turbine slewing bearing.
Performance and Specifications
When it comes to wind turbine slewing bearings, there are certain performance and specification factors that you need to consider. Here are some of the most important ones:
Load Capacity
One of the most critical factors in the performance of a wind turbine slewing bearing is its load capacity. As wind turbines continue to grow in size, the load capacity of the bearings must also increase. Slewing bearings are designed to handle both axial and radial loads, and the load capacity of a bearing is determined by its size, design, and material. The larger the bearing, the higher the load capacity it can handle.
Rotational Speed
Another important factor to consider when it comes to wind turbine slewing bearings is the rotational speed. Wind turbines operate at high rotational speeds, and the bearings must be able to handle these speeds without any issues. The rotational speed of a bearing is determined by its design, size, and lubrication. Bearings with a higher rotational speed rating are typically more expensive, but they are necessary for larger wind turbines.
Service Life
The service life of a wind turbine slewing bearing is another crucial factor to consider. The longer the service life of a bearing, the less maintenance it will require, and the lower the overall cost of ownership. The service life of a bearing is determined by a variety of factors, including its design, size, material, and operating conditions. Generally, the larger the bearing, the longer its service life.
To ensure optimal performance and longevity of your wind turbine slewing bearings, it is important to choose bearings that are designed and manufactured to the highest standards. Be sure to consult with a reputable bearing manufacturer to ensure that you are getting the right bearings for your wind turbine application.
Applications in Wind Turbines
Wind turbines are complex machines that require various components to function effectively. One of the critical components of a wind turbine is the slewing bearing. Slewing bearings are used to transmit the forces of the wind to the entire wind turbine.
Pitch and Yaw Control
Pitch and yaw control are essential for wind turbines to capture the maximum amount of wind energy. Slewing bearings are used in the pitch and yaw control systems of wind turbines. The yaw system allows the nacelle to rotate around the tower and face the wind, while the pitch system adjusts the blade angle to optimize the energy output. Slewing bearings are used to support the yaw and pitch systems and provide the necessary rotation and torque.
Enhancing Energy Efficiency
Wind turbines are designed to capture wind energy and convert it into electricity. Slewing bearings play a crucial role in enhancing energy efficiency by minimizing friction and wear. By reducing friction, slewing bearings help to maximize the energy output of wind turbines, making them more efficient and cost-effective.
In summary, slewing bearings are critical components of wind turbines, supporting the pitch and yaw control systems and enhancing energy efficiency. By transmitting the forces of the wind to the entire wind turbine, slewing bearings help to capture the maximum amount of wind energy and convert it into electricity.