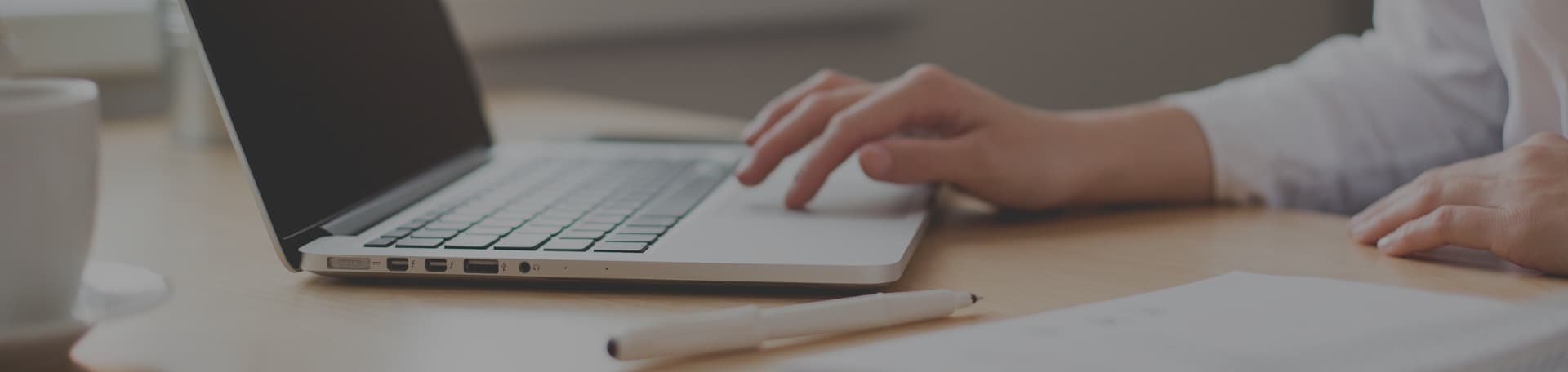
High Precision Slewing Bearing: The Key to Smooth and Accurate Rotational Movement
High Precision Slewing Bearing: The Key to Smooth and Accurate Rotational Movement
If you’re in the market for high precision slewing bearings, you’ve come to the right place. Slewing bearings are an essential component in many types of machinery, and they’re responsible for supporting heavy loads while allowing for smooth and precise rotation. High precision slewing bearings take this a step further, offering unparalleled accuracy and reliability in even the most demanding applications.

One of the key features of high precision slewing bearings is their ability to maintain consistent accuracy even under heavy loads and extreme conditions. This is achieved through careful design and manufacturing processes, which ensure that every component is precisely machined and assembled to exacting standards. As a result, high precision slewing bearings are able to provide reliable performance even in the most challenging environments.
Another important factor to consider when choosing high precision slewing bearings is the level of customization available. Depending on your specific needs, you may require a bearing with a certain size, load capacity, or sealing arrangement. With a wide range of options available, you can find a high precision slewing bearing that meets your exact specifications, ensuring optimal performance and longevity for your machinery.
Fundamentals of High Precision Slewing Bearings

Slewing bearings are a type of rotary bearing that can support large axial and radial loads while allowing for smooth and precise movement. High precision slewing bearings are designed to provide even greater accuracy and control, making them ideal for use in applications such as robotics, machine tools, and aerospace equipment.
Design Principles
The design of high-precision slewing bearings is based on several key principles. First, the bearing must be able to handle high loads without deforming or breaking. To achieve this, the bearing is typically made with a thick outer ring and a thin inner ring, which helps distribute the load evenly across the bearing.
Second, the bearing must be able to rotate smoothly and precisely. This is achieved by using a specialized raceway design that minimizes friction and wear. High precision slewing bearings often use a four-point contact design, which provides greater stability and control than other types of bearings.
Finally, the bearing must be able to maintain its accuracy and precision over time. This requires careful attention to materials, manufacturing processes, and quality control measures.
Material Selection
The materials used in high precision slewing bearings are critical to their performance and longevity. Typically, the outer ring is made from high-strength steel, while the inner ring is made from a lighter, more flexible material such as aluminum or titanium.
Other components of the bearing, such as the raceway and rolling elements, may be made from a variety of materials depending on the specific application. For example, ceramic rolling elements may be used in high-speed applications to reduce friction and wear.
Manufacturing Process
The manufacturing process for high precision slewing bearings is complex and requires a high degree of precision and attention to detail. The process typically involves several steps, including forging, machining, heat treatment, and assembly.
During the forging process, the outer ring of the bearing is formed from a solid piece of steel using a hydraulic press. The inner ring is typically machined from a separate piece of material.
After forging and machining, the bearing components are heat treated to improve their strength and durability. Finally, the components are assembled and tested to ensure that they meet the required specifications for accuracy and performance.
Overall, high precision slewing bearings are an essential component in many types of machinery and equipment. By understanding the design principles, material selection, and manufacturing process behind these bearings, you can make informed decisions about which type of bearing is best suited for your specific application.
Applications and Industry Usage

Slewing bearings are used in a variety of industries and applications that require high precision and accuracy. In this section, we will explore some of the most common applications of high precision slewing bearings.
Robotics and Automation
Slewing bearings play a vital role in robotics and automation systems. They are used in robotic arms, cranes, and other equipment that requires precise movement and positioning. Slewing bearings are designed to handle high axial, radial, and moment loads, making them ideal for heavy-duty robotic applications.
Medical Equipment
High precision slewing bearings are widely used in medical equipment, including CT scanners, MRI machines, and surgical robots. These bearings are designed to provide smooth and accurate movement, which is essential in medical applications where precision is critical.
Aerospace and Defense
Slewing bearings are also used in aerospace and defense applications, including satellite tracking systems, missile launchers, and radar systems. These bearings are designed to withstand extreme temperatures, high speeds, and other harsh conditions.
Overall, high precision slewing bearings are essential components in various industries and applications that require precise movement and positioning. By providing smooth and accurate movement, these bearings help to improve the performance and reliability of equipment and systems.
Performance Characteristics
When it comes to high precision slewing bearings, there are several performance characteristics that are crucial to consider. These bearings are designed to handle heavy loads while maintaining high accuracy and precision. Here are some of the key performance characteristics of high precision slewing bearings:
Accuracy and Precision
One of the most important performance characteristics of high precision slewing bearings is their accuracy and precision. These bearings are designed to provide precise and accurate movement, even under heavy loads. This is achieved through the use of high-quality materials and advanced manufacturing techniques.
Load Handling Capabilities
Another important performance characteristic of high precision slewing bearings is their load handling capabilities. These bearings are designed to handle heavy loads, making them ideal for a variety of applications, including construction equipment, cranes, and wind turbines. They are able to handle both axial and radial loads, as well as moment loads.
Rotational Speed Limits
High precision slewing bearings also have rotational speed limits that must be considered. These limits are determined by the size of the bearing and the materials used in its construction. It is important to choose a bearing that is designed to handle the specific rotational speed required for your application.
In summary, high precision slewing bearings are designed to provide accurate and precise movement, handle heavy loads, and operate within specific rotational speed limits. These performance characteristics make them ideal for a variety of applications where precision and reliability are critical.
Maintenance and Lifespan
When it comes to high precision slewing bearings, proper maintenance is key to ensuring their longevity. In this section, we will discuss the essential maintenance requirements that will help you extend the lifespan of your high precision slewing bearing.
Lubrication Requirements
One of the most critical maintenance tasks for high precision slewing bearings is proper lubrication. Lubrication helps reduce friction, wear, and tear, and prevents premature failure of the bearing. It is essential to use the right lubricant and apply it correctly to ensure optimal performance.
You should follow the manufacturer’s recommendations for lubrication intervals, quantity, and type of lubricant. Over-lubrication can be just as damaging as under-lubrication, so be sure to follow the recommended amounts. Regularly inspect the lubricant for signs of contamination or degradation, and replace it if necessary.
Inspection and Replacement Intervals
Inspection and replacement intervals are another critical aspect of high precision slewing bearing maintenance. Regular inspections can help identify potential problems before they become major issues, and replacements can help prevent catastrophic failures.
You should inspect your high precision slewing bearing at regular intervals, as specified by the manufacturer. Inspections should include a visual examination for signs of wear, damage, or contamination, as well as measurements of critical parameters such as bearing clearance, preload, and torque.
If you detect any issues during your inspection, you should replace the bearing immediately. Do not attempt to repair a damaged bearing, as this can compromise its precision and performance.
Common Failure Modes
Despite proper maintenance, high precision slewing bearings can still fail. Understanding the common failure modes can help you identify potential problems and take corrective action before a catastrophic failure occurs.
Some common failure modes of high precision slewing bearings include:
- Fatigue failure due to excessive loading or overloading
- Wear and tear due to inadequate lubrication or contamination
- Corrosion due to exposure to harsh environments or chemicals
- Misalignment due to improper installation or handling
By understanding these common failure modes and taking proactive measures to prevent them, you can extend the lifespan of your high precision slewing bearing and avoid costly downtime and repairs.
Selection and Customization
When selecting a high precision slewing bearing, there are several factors to consider. In this section, we will discuss the size and load calculations, custom engineering solutions, and mounting and integration of high precision slewing bearings.
Size and Load Calculations
Choosing the right size and load capacity of a high precision slewing bearing is critical for ensuring optimal performance. Before selecting a bearing, it is important to calculate the maximum load that the bearing will be subjected to during its operation. This calculation should take into account both the static and dynamic loads that the bearing will experience.
Once the load capacity has been determined, the size of the bearing can be selected. High precision slewing bearings come in a range of sizes, from small bearings used in precision applications to large bearings used in heavy-duty applications.
Custom Engineering Solutions
In some cases, standard high precision slewing bearings may not meet the specific requirements of an application. In these instances, custom engineering solutions may be required. Custom high precision slewing bearings can be designed to meet specific load, speed, and accuracy requirements.
Custom bearings can also be designed to fit specific mounting configurations, allowing for easier integration into existing systems. When considering custom engineering solutions, it is important to work with a manufacturer that has experience in designing and manufacturing high precision slewing bearings.
Mounting and Integration
Mounting and integration of high precision slewing bearings is critical for ensuring optimal performance. Proper mounting and integration can help to prevent premature bearing failure and ensure accurate positioning.
When mounting a high precision slewing bearing, it is important to ensure that the bearing is properly aligned and securely fastened. The bearing should be mounted on a flat, level surface and aligned to within the manufacturer’s specifications.
Integration of the bearing into the system should also be carefully considered. The bearing should be integrated in a way that minimizes any stress or strain on the bearing and ensures accurate positioning. Proper lubrication and maintenance are also important for ensuring optimal performance and extending the life of the bearing.
Overall, selecting and customizing a high precision slewing bearing requires careful consideration of several factors, including size and load calculations, custom engineering solutions, and mounting and integration. By working with an experienced manufacturer and following best practices for selection and customization, you can ensure optimal performance and long-term reliability of your high precision slewing bearing.