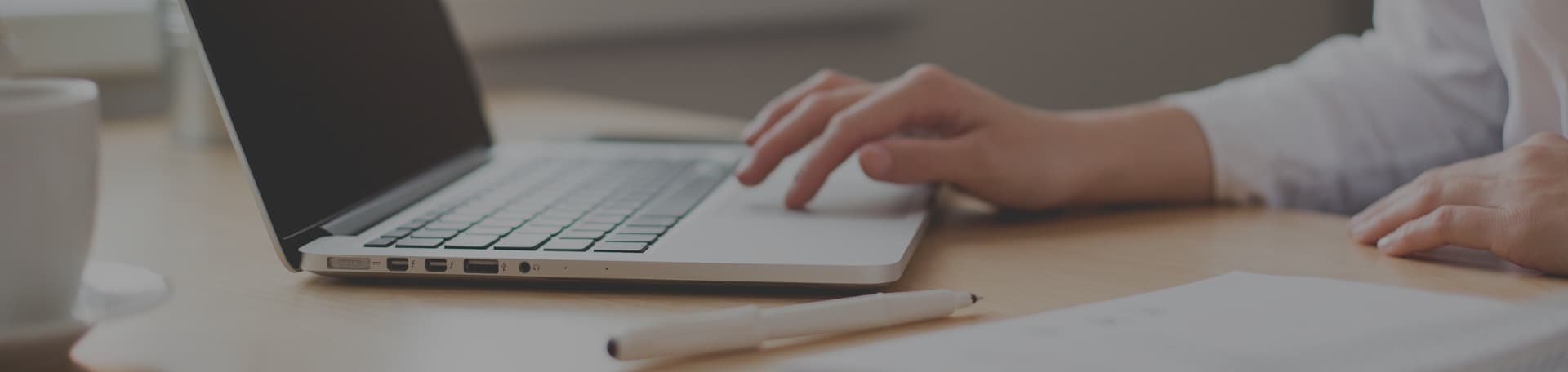
Robot Slewing Bearing: Key Component for Smooth and Precise Rotational Movement
Robot Slewing Bearing: Key Component for Smooth and Precise Rotational Movement
Robot slewing bearings are an essential component in the design of robotic arms and machines. They help to ensure smooth rotation and movement of the arm, making it possible for the robot to perform intricate tasks with precision. The bearings are designed to withstand high loads and provide accurate positioning, making them a critical component in the performance of robotic systems.

Slewing bearings are available in different sizes and designs to meet the specific needs of different robotic applications. They can be customized to fit the specific requirements of a particular robot, taking into account factors such as load capacity, speed, and accuracy. This makes them a versatile component that can be used in a wide range of robotic applications, including industrial, medical, and aerospace.
The use of robot slewing bearings has revolutionized the field of robotics, making it possible to develop machines that can perform complex tasks with precision and accuracy. They have helped to improve the efficiency and reliability of robotic systems, making them an essential component in the design of modern robots. If you are involved in the design or development of robotic systems, it is essential to understand the role of slewing bearings and their importance in ensuring the smooth operation of your robots.
Fundamentals of Robot Slewing Bearings

When it comes to designing robots, one of the most important components to consider is the slewing bearing. Slewing bearings are essential for enabling the smooth and controlled rotation of heavy loads, making them a crucial part of robotics. In this section, we’ll cover the fundamentals of robot slewing bearings.
What is a Slewing Bearing?
A slewing bearing is a type of rolling-element bearing that is designed to support axial, radial, and moment loads. It is also known as a turntable bearing or a rotary bearing. Slewing bearings are typically made up of an inner ring, an outer ring, rolling elements, and a cage. The rolling elements can be balls, rollers, or needles, depending on the application.
Types of Slewing Bearings
There are several types of slewing bearings that are commonly used in robotics. These include:
- Four-point contact ball bearings: These are the most common type of slewing bearing used in robotics. They can support axial, radial, and moment loads, and are designed to handle high thrust loads.
- Crossed roller bearings: These bearings consist of two rows of rollers that are crossed at right angles. They are ideal for applications that require high stiffness and accuracy.
- Three-row roller bearings: These bearings are designed to handle heavy loads and are commonly used in applications such as cranes and excavators.
Benefits of Slewing Bearings
Slewing bearings offer several benefits for robotics applications. These include:
- High load-carrying capacity: Slewing bearings are designed to handle high axial, radial, and moment loads, making them ideal for heavy-duty applications.
- Compact design: Slewing bearings have a compact design, which makes them ideal for applications where space is limited.
- High accuracy: Slewing bearings are designed to provide high accuracy and stiffness, which is essential for robotic applications that require precise positioning.
In summary, slewing bearings are a critical component of robotics, enabling the smooth and controlled rotation of heavy loads. There are several types of slewing bearings available, each with its own unique set of benefits. When designing a robot, it’s essential to choose the right type of slewing bearing for the application to ensure optimal performance.
Design and Material Considerations

When designing a robot slewing bearing, there are several key considerations to keep in mind. These include bearing material selection, design parameters, and sealing and lubrication.
Bearing Material Selection
The material used for the slewing bearing is critical to its performance and longevity. Common materials include chrome steel, stainless steel, and a variety of alloys. The choice of material will depend on factors such as load capacity, operating temperature, and corrosion resistance. Chrome steel is a popular choice for its high load capacity and durability, while stainless steel is often used in applications where corrosion resistance is a concern.
Design Parameters
The design parameters of the slewing bearing will also play a crucial role in its performance. These include factors such as the bearing’s diameter, thickness, and number of rolling elements. The size and shape of the bearing will depend on the specific application and the loads that it will be required to support. It is important to carefully consider these parameters to ensure that the bearing will be able to withstand the stresses it will encounter during operation.
Sealing and Lubrication
Proper sealing and lubrication are also critical to the performance and longevity of a slewing bearing. Seals are used to prevent contaminants from entering the bearing and causing damage, while lubrication is necessary to reduce friction and wear. There are several options for sealing and lubrication, including grease, oil, and dry lubricants. The choice of sealing and lubrication will depend on factors such as the operating environment and the expected service life of the bearing.
In summary, when designing a robot slewing bearing, it is important to carefully consider the material selection, design parameters, and sealing and lubrication options. By selecting the right materials and design parameters, and ensuring proper sealing and lubrication, you can help ensure the longevity and performance of your robot’s slewing bearing.
Manufacturing Processes
The manufacturing process of robot slewing bearings varies depending on the type of bearing. Generally, the process involves several steps that ensure the bearing is durable and robust.
One of the key steps in the manufacturing process is the drilling of the installation hole. Precision drilling is conducted on the end face of the steel ring to facilitate installation. This pivotal step requires careful consideration of the center and cutting angle when drilling the slewing ring bearing. The choice of drilling equipment is also of utmost importance.
Another important step in the manufacturing process is the machining and slip-free induction hardening of bearing raceways. This ensures that the bearing is of high quality and can withstand heavy loads. The gear cutting of the bearing is also crucial as it determines the accuracy and precision of the bearing.
Manufacturers also use unique production processes to ensure that their slewing bearings are of the highest quality. For instance, Liebherr scores high in quality-determining production steps by using a high level of vertical integration. This ranges from the machining and slip-free induction hardening of bearing raceways, through the gear cutting of the bearing, to the final assembly and testing of the slewing bearing.
Overall, the manufacturing process of robot slewing bearings requires precision, attention to detail, and the use of high-quality materials and equipment. By following these steps, manufacturers can produce durable and robust slewing bearings that can withstand heavy loads and provide reliable performance in various applications.
Application in Robotics
Slewing bearings are an essential component of robotic systems as they provide support for the rotating parts of the robot. They are used in various types of robots, from industrial robots to service robots, to ensure smooth and precise rotation of the robot arm. In this section, we will discuss the application of slewing bearings in robotics.
Industrial Robots
Industrial robots are used in manufacturing and production facilities to automate tasks such as welding, painting, and assembly. Slewing bearings are used in the joints of the robot arm to provide smooth and precise movement. They are designed to withstand heavy loads and high speeds, making them ideal for industrial applications.
Slewing bearings used in industrial robots are usually made of high-strength materials such as steel or aluminum. They are designed to be durable and long-lasting, with minimal maintenance requirements. Some manufacturers also offer customized solutions to meet the specific needs of their customers.
Service Robots
Service robots are used in various applications such as healthcare, hospitality, and entertainment. They are designed to interact with humans and provide assistance in various tasks. Slewing bearings are used in the joints of the robot arm to provide smooth and precise movement, enabling the robot to perform tasks with accuracy and precision.
Slewing bearings used in service robots are usually made of lightweight materials such as polymers or composites. They are designed to be compact and efficient, with low friction and minimal noise. Some manufacturers also offer customized solutions to meet the specific needs of their customers.
In conclusion, slewing bearings are an essential component of robotic systems, providing support for the rotating parts of the robot. They are used in various types of robots, from industrial robots to service robots, to ensure smooth and precise rotation of the robot arm. With their durability, precision, and customization options, slewing bearings play a critical role in the success of robotic applications.
Load and Performance Ratings
When selecting a slewing bearing for your robot, it is important to consider its load and performance ratings. Load rating refers to the maximum load that the bearing can withstand without deformation or damage. Performance rating refers to the accuracy and smoothness of the bearing’s rotation.
The load rating of a slewing bearing is determined by its size, design, and materials. It is typically expressed as a maximum axial load, a maximum radial load, or a combination of both. You should choose a bearing with a load rating that exceeds the maximum load that your robot will experience during operation.
In addition to load rating, you should also consider the performance rating of the bearing. This includes factors such as stiffness, precision, and friction torque. A more precise bearing will provide smoother and more accurate rotation, while a stiffer bearing will resist deformation and maintain its accuracy under load.
To ensure that you select the right slewing bearing for your robot, you should consult the manufacturer’s specifications and guidelines. Make sure to consider the specific requirements of your application, such as the weight and size of your robot, the type of loads it will be carrying, and the speed and accuracy of its movements.
Overall, choosing a slewing bearing with the appropriate load and performance ratings is crucial for ensuring the safe and efficient operation of your robot. By taking the time to carefully consider your options and consult with experts, you can select a bearing that will provide the reliability and performance you need for your application.
Maintenance and Life Cycle
Maintenance Strategies
Maintaining your robot slewing bearing is critical to ensure it continues to operate smoothly and efficiently. Regular maintenance can prevent costly breakdowns and extend the service life of your bearing.
One maintenance strategy is to regularly inspect and clean the bearing. You should check for any signs of wear or damage, and clean the bearing to remove any dirt or debris. Another strategy is to regularly lubricate the bearing to ensure it operates smoothly. You should choose the appropriate lubricant and follow the manufacturer’s instructions for application.
In addition to regular maintenance, you should also consider implementing a predictive maintenance program. This involves using sensors and other monitoring tools to track the performance of the bearing and predict when maintenance is required. By identifying and addressing potential issues before they become major problems, you can reduce downtime and extend the service life of your bearing.
Life Cycle Analysis
When selecting a slewing bearing for your robot, it’s important to consider its life cycle. This involves evaluating the environmental impact of the bearing throughout its entire life, from production to disposal.
One factor to consider is the material used to manufacture the bearing. Some materials may be more environmentally friendly than others, and may have a lower impact on the environment during production and disposal. Another factor to consider is the energy required to produce and transport the bearing.
By conducting a life cycle analysis, you can make an informed decision about which slewing bearing to choose for your robot. This can help you reduce your environmental impact and ensure that your robot operates in a sustainable manner.
Installation Guidelines
Installing a robot slewing bearing can be a complex process, but following the proper guidelines can help ensure a successful installation. Here are some general guidelines to follow:
Preparation
Before installing the slewing bearing, make sure to check it for any physical damage. Lift the slewing bearing with eye bolts, ensuring that the eye bolts are fully threaded into the bolt hole. Use a minimum thread engagement of 1.5 times the bolt diameter. The slew bearings shall be mounted in an unloaded condition.
Cleaning
Clean the mounting surfaces of the slewing bearing and the mating components before installation. Use a lint-free cloth and a mild solvent to remove any dirt or debris from the surfaces.
Mounting
When mounting the slewing bearing, make sure to follow the manufacturer’s instructions carefully. Use the correct torque values for the bolts and nuts, and make sure to tighten them in the proper sequence.
Inspection
After installation, inspect the slewing bearing for any signs of damage or wear. Check the bolt torque and make sure that the bearing is properly aligned with the mating components.
Maintenance
Regular maintenance is important to ensure the proper functioning of the slewing bearing. Follow the manufacturer’s recommended maintenance schedule, and make sure to use the correct lubrication and cleaning procedures.
By following these guidelines, you can help ensure a successful installation and long-term performance of your robot slewing bearing.