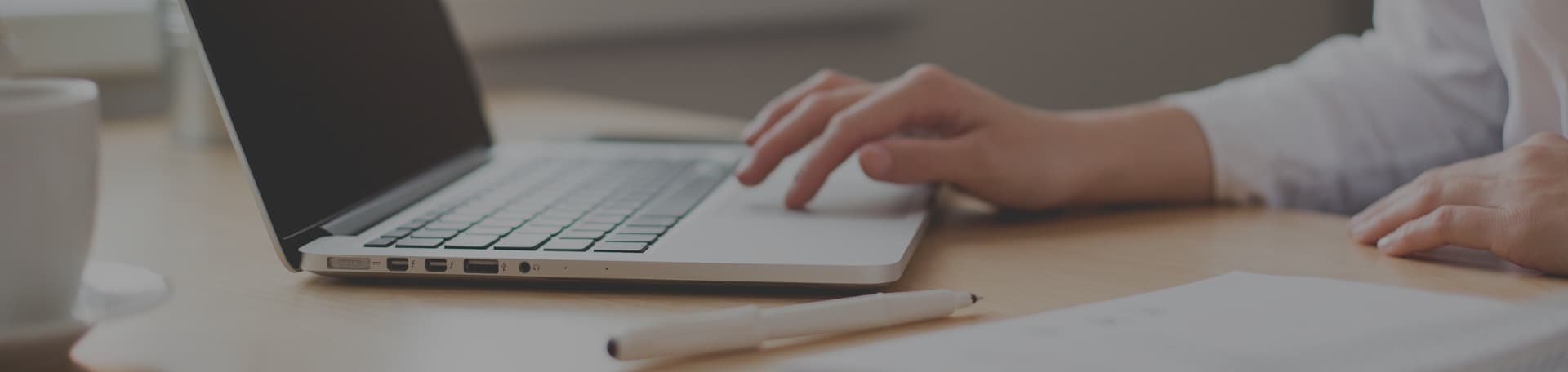
Bearing Ring Manufacturers: A Comprehensive Guide to Choosing the Right Supplier
Bearing Ring Manufacturers: A Comprehensive Guide to Choosing the Right Supplier
If you are in need of bearing ring manufacturers, then you are likely in the market for high-quality bearings that can withstand heavy loads and provide reliable performance. Bearing rings are an essential component of many types of bearings, including ball bearings, roller bearings, and slewing bearings. They serve as the outer raceway for the rolling elements, providing support and guidance for the inner ring and the rolling elements.

When choosing a bearing ring manufacturer, it is important to consider factors such as the quality of the materials used, the precision of the manufacturing process, and the reputation of the manufacturer. High-quality bearing rings should be made from durable materials such as chrome steel or stainless steel, and should be manufactured with precision to ensure optimal performance and longevity. Additionally, a reputable manufacturer will have a track record of producing reliable and high-quality products, and will be able to provide excellent customer service and technical support.
Overview of Bearing Ring Manufacturing

When it comes to bearing ring manufacturing, there are two critical aspects to consider: materials and fabrication processes. In this section, we will provide an overview of both.
Materials and Alloys
Bearing rings are typically made from a variety of materials and alloys, depending on the intended application. Some of the most common materials used include:
- Carbon steel
- Stainless steel
- Chrome steel
- Ceramic
Each material has its own unique properties that make it suitable for specific applications. For example, carbon steel is often used for general-purpose bearings, while stainless steel is ideal for applications that require corrosion resistance.
Fabrication Processes
There are several fabrication processes used in bearing ring manufacturing, including:
- Ring rolling
- Forging
- Turning
- Grinding
Ring rolling is a popular method for producing large-diameter bearing rings. This process involves shaping a heated metal blank between two rollers to create a ring shape. Forging, on the other hand, involves heating a metal blank and then shaping it using a press or hammer.
Turning and grinding are two machining processes that are often used to finish bearing rings. Turning involves rotating the ring against a cutting tool to remove material and create the desired shape, while grinding uses an abrasive wheel to achieve a smooth surface finish.
Bearing ring manufacturing involves carefully selecting the appropriate materials and alloys, as well as utilizing a variety of fabrication processes to create high-quality products.
Global Market Leaders in Bearing Ring Production

When it comes to bearing ring production, there are several global market leaders that dominate the industry. These manufacturers are known for their high-quality products, advanced technology, and extensive distribution networks.
Europe-Based Manufacturers
Some of the top bearing ring manufacturers in Europe include SKF Group, Schaeffler Group, and NTN Corporation. SKF Group, based in Sweden, is one of the largest manufacturers of bearings in the world. They offer a wide range of products, including ball bearings, roller bearings, and plain bearings, and have a strong presence in the automotive and aerospace industries.
Schaeffler Group, based in Germany, is another major player in the bearing ring market. They specialize in the production of precision bearings and have a reputation for innovation and quality. NTN Corporation, based in Japan but with a strong presence in Europe, is also a leading manufacturer of bearings, with a focus on automotive and industrial applications.
Asia-Pacific Manufacturers
The Asia-Pacific region is home to several major bearing ring manufacturers, including NSK Ltd., JTEKT Corporation, and Timken Company. NSK Ltd., based in Japan, is one of the largest manufacturers of bearings in the world, with a focus on automotive and industrial applications. JTEKT Corporation, also based in Japan, specializes in the production of ball bearings and roller bearings, and has a strong presence in the automotive industry.
The Timken Company, based in the United States but with a strong presence in Asia, is another major player in the bearing ring market. They offer a wide range of products, including tapered roller bearings, cylindrical roller bearings, and spherical roller bearings, and have a reputation for quality and reliability.
North American Manufacturers
In North America, some of the top bearing ring manufacturers include SKF USA Inc., Timken Company, and NTN Corporation. SKF USA Inc., based in Pennsylvania, is the North American subsidiary of SKF Group and offers a wide range of products, including ball bearings, roller bearings, and plain bearings.
The Timken Company, based in Ohio, is another major player in the North American bearing ring market. They offer a wide range of products, including tapered roller bearings, cylindrical roller bearings, and spherical roller bearings, and have a strong presence in the aerospace and defense industries. NTN Corporation, based in Japan but with a strong presence in North America, is also a leading manufacturer of bearings, with a focus on automotive and industrial applications.
Overall, these global market leaders in bearing ring production are known for their high-quality products, advanced technology, and extensive distribution networks. Whether you are in the automotive, aerospace, or industrial sector, you can trust these manufacturers to provide reliable and efficient bearing solutions.
Quality Control and Standards
When it comes to bearing ring manufacturers, quality control and standards are of utmost importance. Without proper quality control measures, the bearings produced may not meet industry standards, which can lead to a host of problems down the line. Here are some of the key aspects of quality control and standards that you should be aware of when choosing a bearing ring manufacturer.
ISO Certifications
One of the most important aspects of quality control in bearing ring manufacturing is ISO certification. ISO (International Organization for Standardization) is an independent, non-governmental organization that develops and publishes international standards for various industries. ISO certification ensures that a manufacturer meets specific quality standards and has implemented an effective quality management system.
When choosing a bearing ring manufacturer, it is important to look for one that has ISO certification. This certification ensures that the manufacturer has implemented a quality management system that is designed to meet the needs of customers and regulatory authorities. Some of the key ISO certifications to look for in a bearing ring manufacturer include ISO 9001:2015, which sets out the requirements for a quality management system, and ISO 14001:2015, which sets out the requirements for an environmental management system.
Testing and Inspection Protocols
Another important aspect of quality control in bearing ring manufacturing is testing and inspection protocols. A reputable manufacturer will have a range of testing and inspection protocols in place to ensure that their bearings meet industry standards. Some of the key testing and inspection protocols to look for in a bearing ring manufacturer include:
- Material testing: This involves testing the raw materials that go into the bearings to ensure that they meet industry standards.
- Dimensional testing: This involves testing the dimensions of the bearings to ensure that they meet the required specifications.
- Performance testing: This involves testing the performance of the bearings under a range of conditions to ensure that they meet industry standards.
In addition to these testing and inspection protocols, a reputable bearing ring manufacturer will also have a range of quality control measures in place to ensure that their bearings meet industry standards. These may include:
- Process control measures: These are measures that are put in place to ensure that the manufacturing process is consistent and that the bearings are produced to the required specifications.
- Traceability measures: These are measures that are put in place to ensure that the bearings can be traced back to their source in the event of a problem.
By choosing a bearing ring manufacturer that has ISO certification and a range of testing and inspection protocols in place, you can be confident that the bearings you receive will meet industry standards and perform as expected.
Innovations in Bearing Ring Technology
If you are looking for the latest innovations in bearing ring technology, you have come to the right place. In recent years, there have been significant advancements in the field of bearing ring manufacturing. In this section, we will discuss some of the most notable innovations in this field.
Automation in Manufacturing
One of the most significant advancements in bearing ring manufacturing is the use of automation. With the help of automation, manufacturers can produce bearing rings with greater precision and efficiency. Automated machines can perform tasks such as cutting, grinding, and polishing with a high degree of accuracy, reducing the need for human intervention.
Moreover, automation has enabled manufacturers to produce bearing rings in large quantities, reducing the time and cost of production. This has made bearing rings more affordable and accessible to a wider range of industries.
Advancements in Material Science
Another area where there have been significant advancements is material science. Manufacturers are now using advanced materials such as ceramics, composites, and polymers to produce bearing rings with enhanced properties.
For example, ceramic bearing rings offer several advantages over traditional steel bearing rings. They are more resistant to wear and corrosion, have a higher strength-to-weight ratio, and can operate at higher temperatures. Similarly, composite bearing rings offer improved performance in harsh environments and can withstand high loads and speeds.
In addition to using advanced materials, manufacturers are also developing new coatings and surface treatments to improve the performance and longevity of bearing rings. These coatings can provide better lubrication, reduce friction and wear, and protect against corrosion.
In conclusion, the innovations in bearing ring technology have enabled manufacturers to produce higher quality bearing rings with improved performance and durability. With the continued advancements in automation and material science, we can expect to see even more exciting developments in the future.