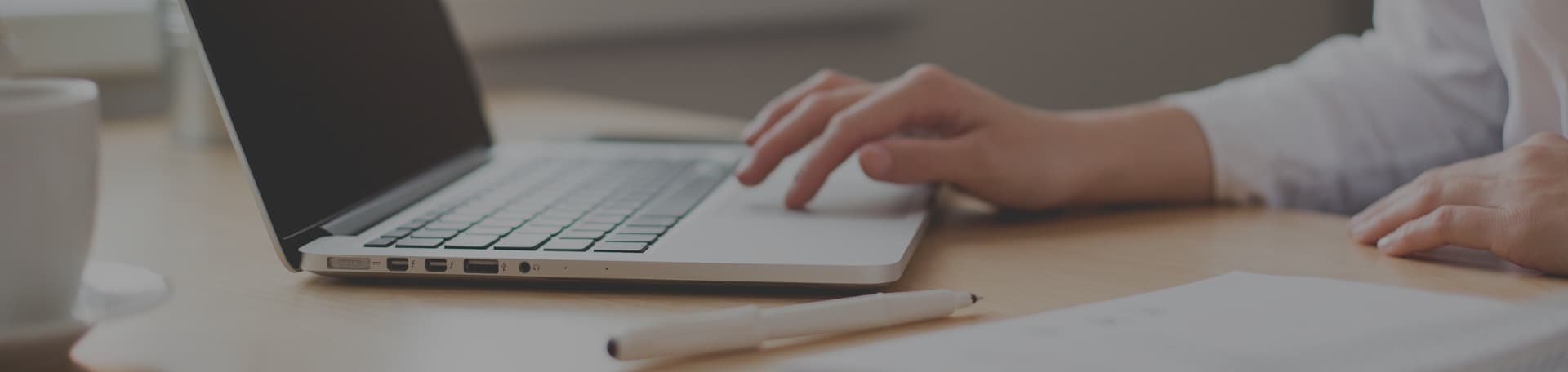
Ball Bearing and Roller Bearing Slewing Ring: What You Need to Know
Ball Bearing and Roller Bearing Slewing Ring: What You Need to Know
Ball Bearing and Roller Bearing Slewing Ring are two types of bearings that are used in various applications. Slewing rings are also known as turntable bearings, and they are used to support the weight of rotating equipment, such as cranes, excavators, and wind turbines. These bearings have two rings that are mounted on top of each other and are designed to accommodate axial, radial, and moment loads.

Ball bearing slewing rings use balls as rolling elements, while roller bearing slewing rings use rollers. Ball bearings are ideal for applications that require high-speed rotation and low friction, while roller bearings are better suited for heavy-duty applications that require high load capacity and durability. Both types of bearings have their advantages and disadvantages, and the choice between them depends on the specific application requirements.
In this article, we will discuss the fundamentals of Ball Bearing and Roller Bearing Slewing Ring, the differences between ball and roller bearings, the materials and manufacturing processes used to make them, installation guidelines, industry applications, and maintenance and servicing. By the end of this article, readers will have a better understanding of the different types of slewing rings and how to choose the right one for their application.
Key Takeaways Ball Bearing and Roller Bearing Slewing Ring
- Ball bearing and roller bearing slewing rings are two types of bearings used in various applications.
- Ball bearings are ideal for high-speed rotation and low friction, while roller bearings are better suited for heavy-duty applications that require high load capacity and durability.
- The choice between ball and roller bearings depends on the specific application requirements.
Fundamentals of Slewing Rings

Design Principles Ball Bearing and Roller Bearing Slewing Ring
Slewing rings are large diameter bearings that facilitate rotational movement while supporting axial, radial, and moment loads. They are commonly used in applications such as cranes, excavators, wind turbines, and medical equipment. The design of slewing rings is based on the principles of rolling element bearings, which include ball bearings and roller bearings.
Ball bearings use balls as the rolling elements and have a point contact with the raceway. On the other hand, roller bearings use cylindrical or tapered rollers and have a line contact with the raceway. The choice of bearing type depends on the specific application requirements such as load capacity, speed, and accuracy.
Slewing rings can be single-row, double-row, or multiple-row designs. The raceway can be internal, external, or both. The internal gear or external gear can be used to transmit torque to the slewing ring. The gear teeth can be straight, helical, or herringbone. The choice of gear type depends on the specific application requirements such as torque transmission, noise level, and efficiency.
Types of Bearings
There are two main types of bearings used in slewing rings: ball bearings and roller bearings. Ball bearings are commonly used in light to medium-duty applications, while roller bearings are used in heavy-duty applications.
Ball bearings can be further classified into four-point contact ball bearings and cross roller bearings. Four-point contact ball bearings have two rows of balls and can support axial, radial, and moment loads. Cross roller bearings have cylindrical rollers arranged in a cross pattern and can support high axial and radial loads.
Roller bearings can be further classified into cylindrical roller bearings, tapered roller bearings, and spherical roller bearings. Cylindrical roller bearings have cylindrical rollers and can support high radial loads. Tapered roller bearings have tapered rollers and can support high radial and axial loads. Spherical roller bearings have barrel-shaped rollers and can support high radial and moderate axial loads.
In summary, slewing rings are important components in various applications that require rotational movement and load support. The design of slewing rings is based on the principles of rolling element bearings, and the choice of bearing type and gear type depends on the specific application requirements.
Ball Bearing Slewing Rings

Ball bearing slewing rings are a type of slewing ring bearing that use ball bearings to support axial and radial loads. They are designed to handle heavy loads and provide smooth rotation. This section will discuss the construction, applications, and maintenance of ball bearing slewing rings.
Construction Ball Bearing and Roller Bearing Slewing Ring
Ball Bearing and Roller Bearing Slewing Ring consist of two rings, an inner ring and an outer ring. The inner ring is attached to the rotating component, while the outer ring is attached to the stationary component. The rings are separated by a series of ball bearings, which allow for smooth rotation.
The ball bearings are housed in a cage, which keeps them evenly spaced and prevents them from rubbing against each other. The cage is typically made of steel or plastic and is designed to withstand the forces generated by the rotating component.
Applications
Ball bearing slewing rings are commonly used in heavy machinery, such as cranes, excavators, and wind turbines. They are also used in turntables, amusement park rides, and other applications that require smooth, precise rotation.
Because of their ability to handle heavy loads, ball bearing slewing rings are ideal for applications where weight is a concern. They are also used in applications where precise positioning is required, such as in telescopes and satellite dishes.
Maintenance
To ensure the longevity of ball bearing slewing rings, proper maintenance is essential. Regular inspection and lubrication can help prevent wear and tear on the bearings and extend the life of the bearing.
When inspecting the bearing, it is important to look for signs of wear, such as pitting or cracking. Lubrication should be done according to the manufacturer’s recommendations, using the appropriate type and amount of lubricant.
In conclusion, ball bearing slewing rings are a reliable and efficient solution for applications that require heavy load capacity and smooth rotation. Proper maintenance can help extend the life of the bearing and ensure optimal performance.
Roller Bearing Slewing Rings
Roller bearing slewing rings are a type of slewing ring bearing that utilizes cylindrical rollers instead of balls. These bearings are designed to handle heavier loads and provide greater stability than ball bearing slewing rings.
Design Features
Roller bearing slewing rings have a unique design that allows them to handle heavy loads while maintaining stability. The rollers are arranged in a cross pattern, which distributes the load evenly across the bearing. This design feature allows the bearing to handle both radial and axial loads.
The rollers in a roller bearing slewing ring are also larger than those in a ball bearing slewing ring. This allows the bearing to handle higher loads and provides greater surface contact between the rollers and the raceway.
Load Handling
Roller bearing slewing rings are designed to handle heavy loads in a variety of applications. These bearings are commonly used in construction equipment, cranes, and wind turbines. They are also used in applications that require high precision and accuracy, such as radar systems and telescopes.
The load capacity of a roller bearing slewing ring depends on several factors, including the size of the bearing, the number of rollers, and the material used to construct the bearing. It is important to select the correct bearing for the application to ensure optimal performance and longevity.
Lubrication
Proper lubrication is essential for the performance and longevity of a roller bearing slewing ring. These bearings require a high-quality lubricant that can withstand heavy loads and high temperatures.
The lubricant should be applied evenly to the bearing to ensure that all rollers are properly lubricated. It is also important to monitor the lubricant level and replace it as needed to prevent damage to the bearing.
Overall, roller bearing slewing rings are a reliable and efficient option for applications that require heavy load handling and stability. By understanding the design features, load handling capabilities, and lubrication requirements of these bearings, users can ensure optimal performance and longevity.
Comparison of Ball and Roller Bearings
When it comes to slewing ring bearings, there are two primary types: ball bearings and roller bearings. While both types serve the same purpose of reducing friction and facilitating smooth motion, there are some key differences in their design and performance that make them better suited for different applications.
Performance Factors
One of the main differences between ball bearings and roller bearings is their performance under different conditions. Ball bearings are generally better suited for high-speed applications, while roller bearings are better suited for heavy loads and shock loads.
Ball bearings have lower friction and can operate at higher speeds than roller bearings. This makes them ideal for applications such as electric motors, assembly lines, and machine tooling equipment. Roller bearings, on the other hand, are better suited for applications that involve heavy loads and shocks, such as automotive engines and construction equipment.
Load Capacities
Another key difference between ball bearings and roller bearings is their load capacities. Roller bearings have a higher load capacity than ball bearings, which makes them better suited for heavy-duty applications.
Roller bearings are designed with cylindrical, spherical, or tapered rollers that distribute the load evenly across the bearing surface. This results in a higher load capacity and better resistance to shock and impact loading. Ball bearings, on the other hand, have a smaller contact area and are better suited for lighter loads.
In summary, when choosing between ball bearings and roller bearings for slewing ring applications, it’s important to consider the specific performance requirements and load capacities of the application. While ball bearings are better suited for high-speed applications, roller bearings are better suited for heavy-duty applications that involve heavy loads and shocks.
Material and Manufacturing
Steel Quality
Slewing ring bearings are made from high-quality steel that is carefully selected to ensure the durability and reliability of the bearing. The steel used in the manufacturing process is typically a high carbon alloy steel, which provides excellent strength and wear resistance. The steel is also heat-treated to further improve its mechanical properties and ensure that it can withstand the high loads and stresses that it will be subjected to during use.
Forging Process
The forging process is a critical step in the manufacturing of slewing ring bearings. The forging process involves heating the steel to a high temperature and then shaping it into the desired shape using a press or hammer. The forging process helps to refine the grain structure of the steel and improve its strength and toughness. It also helps to eliminate any defects or impurities in the steel, which can weaken the bearing and reduce its lifespan.
During the forging process, the steel is carefully shaped into the desired shape, which is typically a ring or a raceway. The shape of the bearing is critical to its performance, as it must be designed to accommodate the rolling elements and provide a smooth and consistent surface for them to roll on. Once the forging process is complete, the bearing is machined to its final dimensions and then heat-treated to further improve its mechanical properties.
Overall, the material and manufacturing process used in the production of slewing ring bearings is critical to their performance and reliability. By using high-quality steel and carefully controlling the forging and machining process, manufacturers can produce bearings that are capable of withstanding the high loads and stresses that they will be subjected to during use.
Installation Guidelines
When it comes to installing ball bearing and roller bearing slewing rings, there are a few guidelines that need to be followed to ensure that the installation is done correctly. This section will cover two important aspects of the installation process: Mounting Procedures and Alignment and Tolerances.
Mounting Procedures
The mounting procedure for a slewing ring bearing is critical to ensure that it is installed correctly and operates efficiently. The process should be carried out in a clean and dry environment. Before installation, the bearing should be inspected for damage or defects. Any damaged or defective parts should be replaced before installation.
When mounting the bearing, it is important to use the correct tools and equipment. A torque wrench should be used to tighten the bolts to the manufacturer’s recommended torque values. Over-tightening the bolts can cause damage to the bearing, while under-tightening can lead to the bearing coming loose during operation.
Alignment and Tolerances
Proper alignment is crucial to ensure that the slewing ring bearing operates efficiently and has a long service life. The bearing should be aligned with the mating components to avoid excessive load, which can cause premature wear and damage to the bearing.
The tolerances for the bearing should be checked during the installation process. The manufacturer’s specifications should be followed carefully to ensure that the tolerances are within the recommended range. Any deviations from the recommended tolerances can lead to premature wear and damage to the bearing.
In summary, proper installation of ball bearing and roller bearing slewing rings is critical to ensure that they operate efficiently and have a long service life. The mounting procedures should be carried out in a clean and dry environment, and the correct tools and equipment should be used. Proper alignment and tolerances should be checked during the installation process to ensure that the bearing operates efficiently.
Industry Applications
Slewing ring bearings are used in a variety of industries due to their ability to support heavy loads and provide smooth rotational movement. In this section, we will discuss two important industries where ball bearing and roller bearing slewing rings are commonly used: wind turbines and marine cranes.
Wind Turbines
Wind turbines generate electricity by converting the kinetic energy of wind into mechanical energy. Slewing ring bearings are used in wind turbines to support the weight of the rotor and allow it to rotate freely. The bearings must be able to withstand high loads and extreme weather conditions, making them a critical component in the operation of wind turbines.
Ball bearing slewing rings are commonly used in wind turbines due to their ability to handle both radial and axial loads. They are also more cost-effective than roller bearing slewing rings. However, roller bearing slewing rings are preferred in some applications due to their higher load capacity and longer service life.
Marine Cranes
Marine cranes are used to lift heavy loads onto and off of ships. Slewing ring bearings are used in marine cranes to support the weight of the load and allow the crane to rotate. The bearings must be able to withstand the harsh marine environment, including saltwater and extreme weather conditions.
Roller bearing slewing rings are commonly used in marine cranes due to their ability to handle heavy loads and provide a longer service life. However, ball bearing slewing rings may be used in some applications where cost is a factor.
In conclusion, ball bearing and roller bearing slewing rings play a critical role in a variety of industries, including wind turbines and marine cranes. The choice between ball bearing and roller bearing slewing rings depends on the specific application and requirements.
Maintenance and Servicing
Inspection Techniques
Regular inspections are important to ensure that the slewing ring bearings are functioning properly. During an inspection, the following items should be checked:
- The condition of the raceways and rolling elements
- The condition of the gear teeth (if applicable)
- The torque required to rotate the bearing
- The amount of axial and radial play
If any of these items are found to be out of specification, the slewing ring bearing should be replaced or repaired.
Replacement Strategies
When replacing a slewing ring bearing, it is important to follow the manufacturer’s recommendations for installation and lubrication. In addition, the following steps should be taken:
- Remove the old bearing carefully, taking care not to damage the mating components.
- Clean the mating surfaces thoroughly to remove any debris or contaminants.
- Install the new bearing carefully, ensuring that it is properly aligned with the mating components.
- Torque the bolts to the manufacturer’s specifications, using a torque wrench to ensure that the correct amount of force is applied.
- Lubricate the bearing according to the manufacturer’s recommendations.
By following these steps, the slewing ring bearing will function properly and provide reliable service for many years.