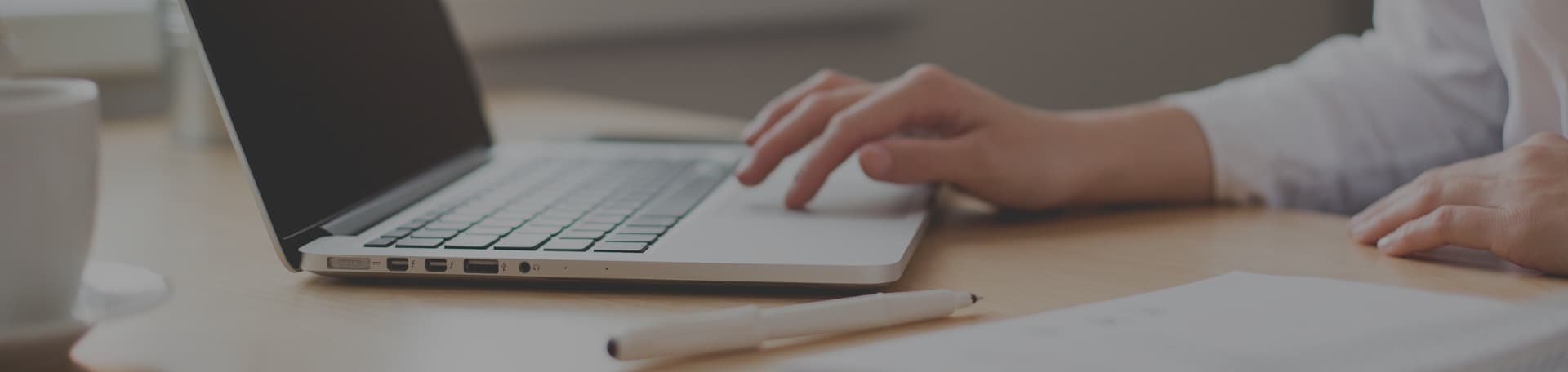
Ball Bearing Slewing Rings: A Comprehensive Guide
Ball Bearing Slewing Rings: A Comprehensive Guide
If you’re in the market for a bearing that can handle heavy loads and provide smooth rotation, then you may want to consider a ball bearing slewing ring. Slewing rings are designed to support axial, radial, and moment loads, making them ideal for applications such as cranes, excavators, and wind turbines. Ball bearing slewing rings are a popular choice due to their ability to handle high speeds and provide low friction.

One of the key benefits of ball bearing slewing rings is their ability to handle both axial and radial loads. This means that they can support weight in both the vertical and horizontal directions, making them ideal for applications where heavy loads need to be lifted or rotated. Additionally, ball bearing slewing rings are designed to provide low friction, which helps to reduce wear and tear on the bearings and extend their lifespan.
Another advantage of ball bearing slewing rings is their ability to handle high speeds. This makes them ideal for applications where a high rate of rotation is required, such as wind turbines or amusement park rides. Additionally, ball bearing slewing rings are designed to be compact, which helps to reduce the overall size and weight of the equipment they are used in.
Fundamentals of Ball Bearing Slewing Rings

If you’re looking for a reliable and robust solution to support heavy loads and enable rotational motion, ball bearing slewing rings are the way to go. These bearings are designed to handle axial, radial, and moment loads, making them ideal for a wide range of applications.
Ball bearing slewing rings are essentially large bearings that consist of an inner ring, outer ring, and a set of rolling elements. The rolling elements are typically balls, but they can also be rollers or cylinders. The rings are designed to rotate around a central axis, allowing for smooth and precise movement.
One of the main advantages of ball bearing slewing rings is their ability to handle heavy loads. Because they are designed to support both axial and radial loads, they can handle a wide range of applications, from large cranes and excavators to wind turbines and solar trackers.
Another advantage of ball bearing slewing rings is their durability. These bearings are designed to withstand harsh environments and extreme temperatures, making them ideal for use in a variety of industries. They are also designed to require minimal maintenance, reducing downtime and increasing productivity.
Overall, ball bearing slewing rings are an excellent choice for applications that require precise and reliable rotational motion. Whether you’re working with heavy loads or extreme temperatures, these bearings are designed to handle the toughest conditions and provide long-lasting performance.
Design and Manufacturing
Materials and Engineering
Ball bearing slewing rings are typically made from high-quality materials, such as chrome steel or stainless steel, to ensure maximum durability and performance. The bearing raceways, in conjunction with the rolling elements and cages or spacers, are designed to accommodate loads acting singly or in combination, and in any direction. The design of the slewing ring bearings can be customized to meet the demands of particular applications, with outside diameters ranging from 0.1 to 18 meters.
In addition to the materials used, the engineering of ball bearing slewing rings is critical to their performance. The design must take into account factors such as load capacity, stiffness, and rotational speed. Engineers use advanced software and modeling techniques to optimize the design of the bearings for specific applications.
Production Processes
The production processes for ball bearing slewing rings involve a number of steps to ensure the highest quality and performance. The manufacturing process typically includes the following steps:
- Raw material selection – The raw materials used in the production of ball bearing slewing rings are carefully selected to ensure they meet the required specifications for strength and durability.
- Forging – The raw materials are heated to a high temperature and then forged into the desired shape using a press or hammer.
- Machining – The forged rings are then machined to the required dimensions and tolerances. This involves cutting, drilling, and grinding the rings to the correct shape and size.
- Heat treatment – The rings are then heat-treated to improve their strength and durability. This involves heating the rings to a high temperature and then cooling them rapidly to harden the material.
- Assembly – The final step in the production process is the assembly of the bearing. This involves fitting the rolling elements, cages, and spacers into the bearing raceways and then securing them in place.
Overall, the design and manufacturing of ball bearing slewing rings is a complex process that requires a high level of expertise and attention to detail. By using high-quality materials and advanced engineering techniques, manufacturers can produce bearings that are optimized for specific applications and offer exceptional performance and durability.
Types and Variations
If you are looking for a reliable and efficient way to support heavy loads and rotation, ball bearing slewing rings are a great option. These rings come in different types and variations depending on the load capacity, speed, and other factors. In this section, we will cover the three main types of ball bearing slewing rings: single-row, double-row, and crossed roller rings.
Single-Row Ball Bearing Slewing Rings
Single-row ball bearing slewing rings are the most common type of slewing rings. They have a single row of balls and a standard bearing raceway. They offer four points of contact between the balls and the raceway, which allows them to handle both axial and radial loads. Single-row rings are suitable for applications that require moderate load capacity and low-speed rotation. They are also relatively easy to install and maintain.
Double-Row Ball Bearing Slewing Rings
Double-row ball bearing slewing rings have two rows of balls and two raceways, which provide eight points of contact for each ball. This design allows them to handle higher loads and faster rotation speeds than single-row rings. Double-row rings are suitable for applications that require high load capacity and moderate to high-speed rotation. They are commonly used in cranes, excavators, and other heavy-duty equipment.
Crossed Roller Slewing Rings
Crossed roller slewing rings have a different design than ball bearing rings. They use rollers instead of balls, which allows them to handle higher loads and provide more precise rotation. Crossed roller rings have a crossed arrangement of rollers that provides two points of contact for each roller. This design allows them to handle both axial and radial loads and provide smooth and accurate rotation. Crossed roller rings are suitable for applications that require high precision, such as machine tools, robotics, and medical equipment.
In summary, ball bearing slewing rings come in different types and variations that can handle different loads, speeds, and precision requirements. Choosing the right type of slewing ring depends on your specific application needs.
Applications and Industry Use
Ball bearing slewing rings are versatile and can be used in a variety of applications across different industries. Here are a few examples of industries and applications where ball bearing slewing rings are commonly used.
Construction Machinery
Ball-bearing slewing rings are widely used in construction machinery such as cranes, excavators, and loaders. They help to support the weight of the machinery, enable smooth rotation, and provide stability. The four-point contact design of ball-bearing slewing ring allows them to handle both axial and radial loads, making them ideal for use in construction machinery.
Medical Equipment
Ball-bearing slewing ring are also used in medical equipment such as CT scanners and X-ray machines. They help to support the weight of the equipment and enable smooth rotation, which is important for accurate imaging. The high precision and reliability of ball-bearing slewing ring make them ideal for use in medical equipment where accuracy and reliability are critical.
Renewable Energy
Ball-bearing slewing rings are also used in renewable energy applications such as wind turbines and solar trackers. They help to support the weight of the equipment and enable smooth rotation, which is important for efficient energy generation. The high load carrying capacity and durability of ball-bearing slewing ring make them ideal for use in renewable energy applications where reliability and efficiency are critical.
In summary, ball-bearing slewing ring are versatile and can be used in a variety of applications across different industries. Their ability to support heavy loads, handle both axial and radial loads, and enable smooth rotation makes them ideal for use in construction machinery, medical equipment, and renewable energy applications.
Installation and Maintenance
When it comes to installing and maintaining ball-bearing slewing ring, there are a few key procedures that you need to keep in mind. In this section, we will cover the mounting procedures, lubrication and care, and troubleshooting that you need to be aware of to keep your ball-bearing slewing ring operating smoothly.
Mounting Procedures
Proper mounting procedures are essential for ensuring that your ball-bearing slewing ring operate correctly. Before mounting the bearing, it is important to ensure that the mounting surface is clean and free of any debris or contaminants. This will help to prevent damage to the bearing and ensure that it operates smoothly.
When mounting the bearing, it is important to follow the manufacturer’s instructions carefully. This will ensure that the bearing is mounted correctly and that it operates smoothly. In addition, it is important to ensure that the bearing is properly aligned and that the mounting bolts are tightened to the correct torque.
Lubrication and Care
Proper lubrication and care are essential for ensuring that your ball bearing slewing ring operate smoothly and last a long time. It is important to use the correct lubricant for your bearing and to apply it in the correct amount and at the correct intervals.
In addition, it is important to regularly inspect the bearing for signs of wear or damage. This will help to identify any problems early and prevent them from becoming more serious. If you notice any signs of wear or damage, it is important to take corrective action immediately.
Troubleshooting
Even with proper installation and maintenance, problems can still occur with ball bearing slewing ring. Some common problems include noise, vibration, and overheating. If you experience any of these problems, it is important to identify the cause and take corrective action.
One common cause of noise and vibration is misalignment. If you notice any noise or vibration, it is important to check the alignment of the bearing and take corrective action if necessary. Overheating can be caused by a lack of lubrication or by excessive loading. If you notice any overheating, it is important to identify the cause and take corrective action immediately.
Proper installation and maintenance are essential for ensuring that your ball bearing slewing ring operate smoothly and last a long time. By following the procedures outlined in this section, you can help to ensure that your bearings operate correctly and avoid costly downtime.
Performance and Testing
When it comes to ball bearing slewing ring, performance and testing are crucial factors that determine their suitability for various applications. Here are some key aspects of performance and testing that you should be aware of:
Load Capacity Testing
Load capacity testing is a critical aspect of ball bearing slewing ring performance. The load capacity of a slewing ring refers to the maximum load that it can support without failure. This value is typically determined by testing the slewing ring under different loads and measuring the resulting deformation.
During load capacity testing, the slewing ring is subjected to a range of loads and stresses that simulate real-world operating conditions. This testing is typically conducted in a laboratory setting, using specialized equipment and software that can accurately measure the load and deformation of the slewing ring.
Lifecycle and Reliability
Lifecycle and reliability testing are also important aspects of ball bearing slewing ring performance. These tests are designed to evaluate the durability and longevity of the slewing ring under different operating conditions.
During lifecycle testing, the slewing ring is subjected to a range of loads and stresses that simulate the expected lifespan of the product. This testing is typically conducted over an extended period of time, during which the slewing ring is monitored for signs of wear and tear.
Reliability testing, on the other hand, is focused on evaluating the probability of failure of the slewing ring under different conditions. This testing is typically conducted using statistical methods that take into account the expected lifespan of the product, as well as the likelihood of different types of failure.
In conclusion, load capacity testing, lifecycle testing, and reliability testing are all important aspects of ball bearing slewing ring performance. By understanding these factors, you can make informed decisions about which slewing rings are best suited for your specific applications.