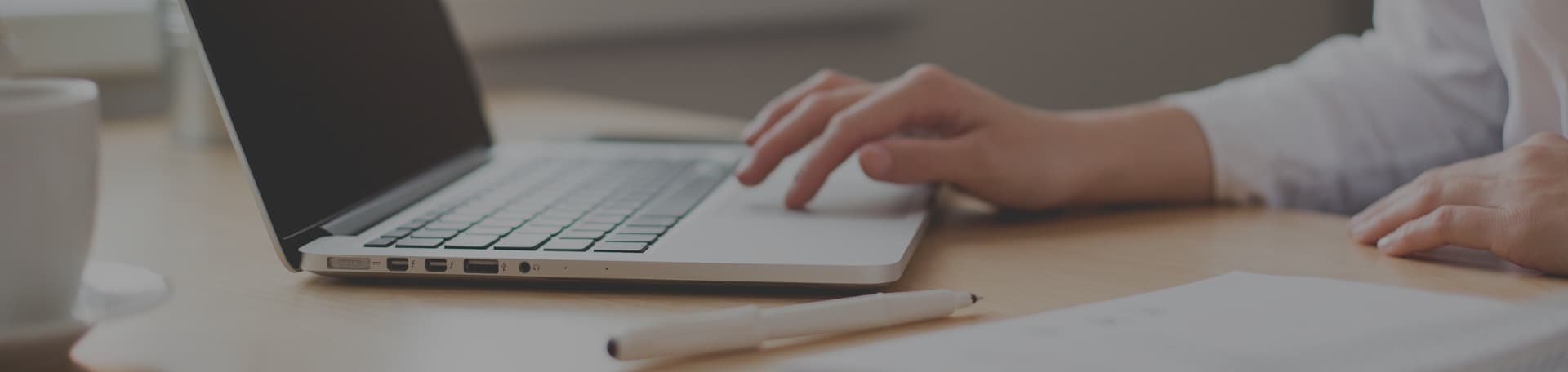
Ball Slewing Bearing: What it is and How it Works
Ball Slewing Bearing: What it is and How it Works
If you’re in the market for a high-capacity bearing that can handle a variety of loads and movements, you might want to consider a ball slewing bearing. These bearings are designed to handle both axial and radial loads, making them ideal for a wide range of applications, from cranes and excavators to wind turbines and solar panels.

One of the key advantages of ball slewing bearings is their ability to handle heavy loads with ease. Because of their design, these bearings can support both axial and radial loads, which makes them ideal for use in heavy-duty equipment that needs to move or rotate in different directions. Additionally, ball slewing bearings are known for their durability and reliability, which means you can count on them to perform well even in harsh environments.
Another advantage of ball slewing bearings is their versatility. These bearings can be customized to meet the specific needs of your application, whether you need a bearing with a particular load capacity, size, or sealing arrangement. This makes them a popular choice for a wide range of industries, from construction and mining to renewable energy and aerospace.
Fundamentals of Ball Slewing Bearings

If you are looking for a type of bearing that can handle both axial and radial loads while providing smooth rotation, then a ball slewing bearing might be the solution you need. Ball slewing bearings consist of an inner and outer ring with a set of balls in between. The balls are held in place by a cage, which allows them to roll smoothly and evenly distribute the load.
One of the main advantages of ball slewing bearings is their ability to handle a wide range of loads. They can support axial, radial, and moment loads simultaneously, which makes them ideal for applications where heavy loads are present. Additionally, they are designed to handle both static and dynamic loads, which means they can handle both stationary and moving loads.
Another advantage of ball slewing bearings is their compact design. They take up less space than other types of bearings, which makes them ideal for applications where space is limited. They are also relatively easy to install and maintain, which can save you time and money in the long run.
When selecting a ball slewing bearing, it is important to consider the load capacity, speed, and operating temperature. You should also consider the lubrication requirements, as proper lubrication is critical to the longevity and performance of the bearing. Consult the manufacturer’s specifications and guidelines to ensure that you select the right bearing for your application.
In summary, ball slewing bearings are a versatile and compact solution for applications that require smooth rotation and the ability to handle a wide range of loads. With proper selection, installation, and maintenance, they can provide reliable and efficient performance for years to come.
Design and Engineering
When it comes to ball slewing bearings, the design and engineering of these components are critical to their performance and longevity. In this section, we will explore the core components, material selection, and geometric configurations that are used in the design and engineering of ball slewing bearings.
Core Components
Ball slewing bearings consist of several core components, including the inner ring, outer ring, balls, and cage. The inner and outer rings are typically made from high-strength steel and are designed to withstand heavy loads and high speeds. The balls are made from hardened steel and are used to reduce friction between the inner and outer rings. The cage, which is also made from steel, is used to keep the balls evenly spaced and prevent them from rubbing against each other.
Material Selection
The material selection for ball slewing bearings is critical to their performance. The inner and outer rings are typically made from high-strength steel, such as 42CrMo4 or 50Mn, which provides excellent fatigue resistance and wear resistance. The balls are made from hardened steel, such as GCr15 or 100Cr6, which provides excellent hardness and wear resistance. The cage is typically made from low-carbon steel, which provides excellent strength and durability.
Geometric Configurations
Ball slewing bearings come in a variety of geometric configurations, including single-row, double-row, and three-row designs. Single-row designs are typically used in applications where space is limited, while double-row and three-row designs are used in applications where higher load capacity is required. The number of balls used in the design of a ball slewing bearing can also vary, with more balls typically providing higher load capacity and better resistance to shock and vibration.
The design and engineering of ball slewing bearings are critical to their performance and longevity. By carefully selecting the core components, materials, and geometric configurations, engineers can create ball slewing bearings that are capable of withstanding heavy loads and high speeds, while also providing excellent wear resistance and durability.
Manufacturing Processes
When it comes to ball slewing bearing production, there are several key processes involved. These processes ensure the bearings are strong, durable, and able to withstand heavy loads. In this section, we will explore the three main manufacturing processes: forging and machining, heat treatment, and quality control.
Forging and Machining
The first step in producing a ball slewing bearing is forging and machining. This process involves shaping the metal into the desired shape and size. The metal is heated to a high temperature and then hammered or pressed into shape. Once the metal has been forged, it is then machined to create the final shape and size. Machining involves using a lathe or milling machine to remove excess material and create the required dimensions.
Heat Treatment
After the forging and machining process, the ball slewing bearing is heat-treated. Heat treatment involves heating the metal to a high temperature and then cooling it rapidly. This process helps to improve the strength and durability of the metal. The heat treatment process can also be used to adjust the hardness of the metal to suit specific applications.
Quality Control
Quality control is an essential part of the ball slewing bearing manufacturing process. During this stage, the bearings are inspected to ensure they meet the required specifications. This includes checking the dimensions, surface finish, and hardness of the bearings. Quality control also involves testing the bearings to ensure they can withstand heavy loads and have a long lifespan.
In conclusion, the manufacturing process of ball slewing bearings involves forging and machining, heat treatment, and quality control. Each of these processes is essential in ensuring the bearings are strong, durable, and able to withstand heavy loads. By following these processes, manufacturers can produce high-quality ball slewing bearings that meet the needs of a wide range of industries.
Applications and Industry Use
Ball slewing bearings are versatile components that find use in a wide range of applications. Here are some of the industries that rely on ball slewing bearings and how they use them.
Heavy Machinery
Ball slewing bearings are a critical component in heavy machinery, such as excavators, cranes, and drilling rigs. These bearings are used to support heavy loads and provide smooth rotation of the machinery. Ball slewing bearings are ideal for heavy machinery because they can handle both axial and radial loads, making them suitable for high-stress applications.
Wind Turbines
Ball slewing bearings are also used in wind turbines. These bearings are used to support the rotor, which is the part of the turbine that generates electricity. The rotor is subject to high loads and must turn smoothly to generate power. Ball slewing bearings are ideal for wind turbines because they can handle both axial and radial loads and provide smooth rotation.
Medical Equipment
Ball slewing bearings are also used in medical equipment, such as CT scanners and MRI machines. These bearings are used to support the rotating parts of the equipment, which must turn smoothly to produce accurate images. Ball slewing bearings are ideal for medical equipment because they can handle both axial and radial loads and provide smooth rotation, making them suitable for high-precision applications.
Overall, ball slewing bearings are a critical component in many industries, providing support for heavy loads and smooth rotation. Whether you are building heavy machinery, wind turbines, or medical equipment, ball slewing bearings are an essential component that you can rely on.
Installation and Maintenance
Proper installation and maintenance of ball slewing bearings are crucial for their optimal performance and longevity. In this section, we will discuss the necessary steps you need to take to ensure that your ball slewing bearings are installed correctly and maintained properly throughout their lifespan.
Mounting Procedures
When mounting ball slewing bearings, it is important to follow the manufacturer’s instructions carefully. Improper mounting can lead to premature failure of the bearing. The mounting surfaces must be machined flat after all welding and stress relief treatment on the structures is complete. If subsequent welding is necessary, it must be done before the bearing is mounted.
To ensure proper mounting, you should use appropriate tools and equipment. The bearing should be lifted with eye bolts, and the eye bolts should be fully threaded into the bolt hole. Use a minimum thread engagement of 1.5 times the bolt diameter. The slewing bearings shall be mounted in an unloaded condition to avoid damaging the bearing.
Lubrication and Sealing
Proper lubrication and sealing are essential for the smooth operation of ball slewing bearings. The type and amount of lubrication required will depend on the application and the manufacturer’s recommendations. Over-lubrication can cause overheating and premature failure, while under-lubrication can cause excessive wear and damage to the bearing.
The sealing system should also be checked regularly to ensure that it is functioning properly. The seals should be kept clean and free of debris to prevent contamination and premature wear.
Inspection and Replacement
Regular inspection and maintenance of ball slewing bearings can help prevent unexpected downtime and costly repairs. The frequency of inspection will depend on the application and the manufacturer’s recommendations.
During inspections, you should check for signs of wear, damage, and contamination. If any issues are detected, the bearing should be replaced immediately. Replacement should only be done by qualified personnel using appropriate tools and equipment.
In summary, proper installation, lubrication, sealing, and inspection are necessary for the optimal performance and longevity of ball slewing bearings. By following the manufacturer’s instructions and taking the necessary steps to maintain your bearings, you can ensure that they will operate smoothly and reliably for years to come.
Market Trends and Future Outlook
The ball slewing bearing market is expected to witness steady growth in the coming years. According to a report by The Insight Partners, the global slewing bearing market is expected to grow at a CAGR of 5.4% from 2021 to 2028, reaching a value of $5,831.2 million by 2028. This growth can be attributed to the increasing concerns about national security, which has led governments across the world to allocate greater funds to strengthen their defense forces.
Moreover, with the increasing demand for renewable energy, the use of slewing bearings in wind turbines is expected to increase significantly. This is because slewing bearings are an essential component of wind turbines, helping to ensure that the blades rotate smoothly and efficiently. As a result, the growth of the wind energy sector is expected to drive the demand for slewing bearings in the coming years.
In addition, the market is witnessing a trend towards the development of lightweight and compact slewing bearings. These bearings are designed to offer high load capacity and durability while occupying minimal space. This trend is driven by the need for compact and lightweight equipment in various industries, including aerospace, defense, and robotics.
Furthermore, the market is witnessing an increasing demand for customized slewing bearings. This is because different industries have different requirements for slewing bearings, and customized bearings can help to meet these specific needs. As a result, manufacturers are increasingly focusing on developing customized solutions to cater to the specific needs of different industries.
Overall, the ball slewing bearing market is expected to witness steady growth in the coming years, driven by the increasing demand for renewable energy, the trend towards lightweight and compact bearings, and the increasing demand for customized solutions.