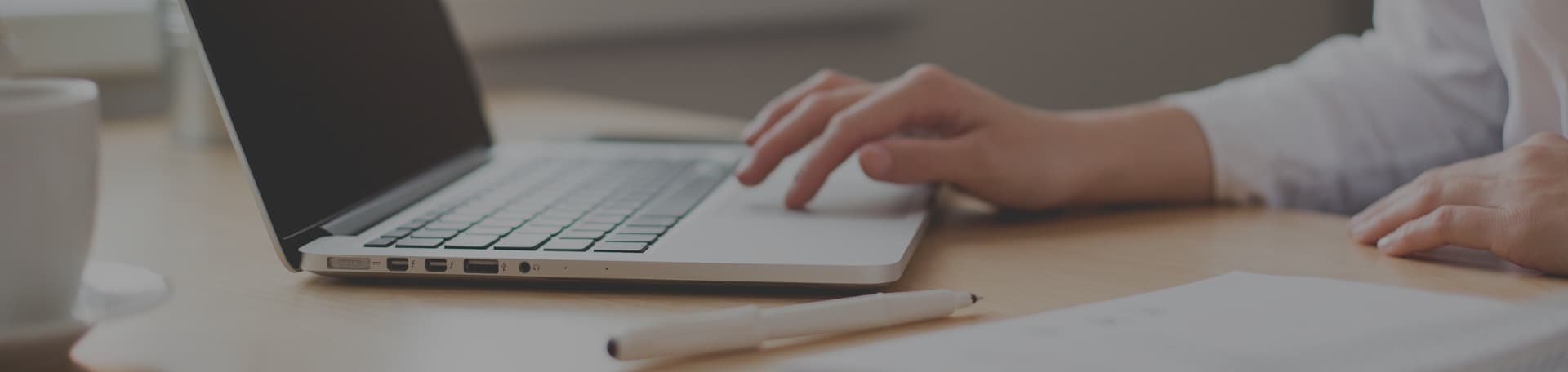
Crane Hook Thrust Bearing: What You Need to Know
Crane Hook Thrust Bearing: What You Need to Know
If you work in the construction or shipping industry, you may be familiar with crane hook thrust bearing. These bearings are designed to handle heavy thrust loads and low speeds of rotation, making them ideal for crane hook applications. They are also commonly used in primary metals, material handling, and shipping ports.

Crane hook thrust bearings are available in various types, including the CT and WCT types. Both types have weather shields for bearing protection, but the WCT type also has a grease fitting for lubrication. These bearings can handle shank diameters up to 10 inches and are ideal for applications experiencing heavy axial loads, such as mill stands, screw-down systems, and piercing mills.
If you’re in the market for crane hook thrust bearings, it’s important to choose a reputable supplier who can provide high-quality bearings that meet your specific needs. With the right bearings, you can ensure the safe and efficient operation of your crane or other heavy equipment.
Crane Hook Thrust Bearing Overview

Function and Importance
Crane hook thrust bearings are essential components in the primary metals, material handling, and shipping port industries. These bearings are designed to withstand the heavy thrust loads and low speeds of rotation encountered in crane hook applications. The bearing is placed between the crane hook and the load, allowing for smooth and efficient lifting and lowering of heavy loads.
Crane hook thrust bearings are critical to the safety and efficiency of crane operations. Without the proper thrust bearings, the crane hook may not be able to support the weight of the load, leading to equipment failure and potential injury to personnel. Additionally, the bearings must be designed to withstand harsh operating conditions, including extreme temperatures, high humidity, and exposure to corrosive materials.
Design Principles
Crane hook thrust bearings are typically cylindrical roller bearings, which consist of a cylindrical inner ring, a set of rollers, and a cylindrical outer ring. The rollers are arranged in a cage, which keeps them evenly spaced and prevents them from coming into contact with each other. This design allows for high radial and axial load-carrying capacity, making it ideal for crane hook applications.
The design of the crane hook thrust bearing must take into account several factors, including the load capacity, speed of rotation, and operating conditions. The bearing must be able to handle the weight of the load and provide smooth and efficient operation at low speeds. It must also be designed to withstand the harsh operating conditions, including exposure to moisture, dust, and other contaminants.
In summary, crane hook thrust bearings are critical components in crane operations, providing the necessary support and efficiency for lifting and lowering heavy loads. These bearings must be designed to withstand the harsh operating conditions encountered in crane applications and must be able to handle the weight of the load while providing smooth and efficient operation.
Types of Thrust Bearings

When it comes to crane hook thrust bearings, there are two main types: tapered roller bearings and spherical roller bearings.
Tapered Roller Bearings
Tapered roller bearings are designed to handle both thrust and radial loads. They consist of tapered inner and outer raceways with tapered rollers arranged between them. The angle of the taper determines the bearing’s load capacity; a steeper angle means a higher load capacity. Tapered roller bearings are commonly used in heavy machinery and equipment, including crane hooks.
Spherical Roller Bearings
Spherical roller bearings can handle high radial loads and moderate thrust loads. They have two rows of symmetrical spherical rollers, which align themselves with the outer ring raceway. This design allows for misalignment and reduces stress on the bearing. Spherical roller bearings are commonly used in applications where misalignment is expected, such as in crane hooks.
Both types of thrust bearings have their advantages and disadvantages, and the choice between them depends on the specific application requirements. Tapered roller bearings have higher load capacities but may not be suitable for misaligned loads, while spherical roller bearings can handle misalignment but have lower load capacities.
Material and Manufacturing
Material Selection
When it comes to crane hook thrust bearings, the selection of materials is crucial. The materials used must be able to withstand heavy loads and extreme temperatures. Common materials used for thrust bearings include steel, bronze, and brass. Steel is the most commonly used material due to its high strength and durability. Bronze and brass are also used, but they are not as strong as steel.
The type of steel used for thrust bearings is typically high-carbon steel or alloy steel. These materials have high tensile strength and can withstand high loads. Bronze and brass are used for applications where the load is not as heavy. These materials are softer than steel, which allows for better lubrication and less wear on the bearing.
Manufacturing Processes
The manufacturing process for crane hook thrust bearings is critical to ensure the bearings are of high quality and can withstand the heavy loads they will be subjected to. The manufacturing process involves several steps, including forging, machining, and heat treatment.
Forging is the process of shaping the metal into the desired shape. This is typically done using a hammer or press. Once the metal has been forged into the desired shape, it is then machined to achieve the final dimensions and tolerances.
Heat treatment is a critical step in the manufacturing process. The heat treatment process involves heating the metal to a specific temperature and then cooling it at a specific rate. This process helps to improve the strength and durability of the metal.
Once the bearings have been forged, machined, and heat-treated, they are inspected to ensure they meet the required specifications. This includes checking for dimensional accuracy, surface finish, and material properties.
In summary, the selection of materials and the manufacturing process are critical to ensuring the quality and durability of crane hook thrust bearings. Steel is the most commonly used material due to its high strength and durability, while bronze and brass are used for applications where the load is not as heavy. The manufacturing process involves several steps, including forging, machining, and heat treatment, and the bearings are inspected to ensure they meet the required specifications.
Installation and Maintenance
Installation Procedures
When installing a crane hook thrust bearing, it is important to follow the manufacturer’s instructions carefully. The installation process typically involves the following steps:
- Clean the mounting surfaces thoroughly to remove any dirt, debris, or old lubricant.
- Apply a thin layer of high-quality lubricant to the mounting surfaces and the bearing itself.
- Carefully align the bearing with the mounting surfaces and press it into place.
- Tighten the mounting bolts to the manufacturer’s recommended torque specification.
- Verify that the bearing is properly aligned and seated.
It is important to note that improper installation can result in premature bearing failure, so it is crucial to follow the manufacturer’s instructions closely.
Maintenance and Lubrication
Proper maintenance and lubrication are essential for ensuring the longevity and optimal performance of a crane hook thrust bearing. The following maintenance and lubrication procedures are recommended:
- Regularly inspect the bearing for signs of wear or damage, such as cracks, corrosion, or pitting.
- Clean the bearing and surrounding area regularly to remove any debris or contaminants that could cause damage.
- Apply a high-quality lubricant to the bearing according to the manufacturer’s recommended schedule.
- Monitor the bearing’s temperature during operation to ensure that it is operating within the manufacturer’s recommended range.
- Replace the bearing if it shows signs of significant wear or damage.
By following these procedures, you can help ensure that your crane hook thrust bearing operates smoothly and reliably for years to come.
Performance and Testing
When it comes to crane hook thrust bearings, performance and testing are critical factors to consider. The load capacity testing and durability assessments are two essential aspects of the performance and testing process.
Load Capacity Testing
Load capacity testing is the process of determining the maximum weight that a crane hook thrust bearing can handle. The load capacity of the bearing depends on various factors such as the size and shape of the bearing, the material used to manufacture the bearing, and the design of the crane hook.
During load capacity testing, the bearing is subjected to a range of weight loads to determine its maximum capacity. The test results are then used to determine the safe working load limit (SWL) of the bearing. The SWL is the maximum weight that the bearing can safely handle without failing.
Durability Assessments
Durability assessments are essential to ensure that the crane hook thrust bearing can withstand harsh operating conditions. These assessments involve subjecting the bearing to various environmental factors such as temperature, humidity, and vibration.
The durability assessments also involve subjecting the bearing to simulated operating conditions to determine its lifespan. The test results are then used to determine the expected lifespan of the bearing and the maintenance requirements to keep it in optimal condition.
In conclusion, performance and testing are critical factors to consider when selecting a crane hook thrust bearing. Load capacity testing and durability assessments are two essential aspects of the performance and testing process that should be carefully considered to ensure that the bearing can withstand harsh operating conditions and safely handle the load capacity required.