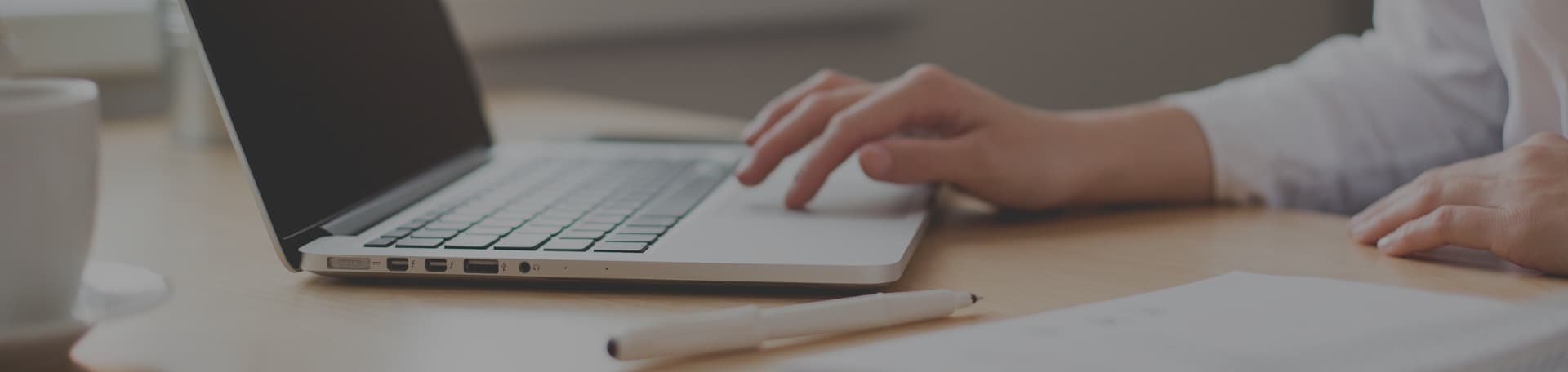
Cross Roller Bearing Design: A Comprehensive Guide
Cross Roller Bearing Design: A Comprehensive Guide
Cross roller bearing design is a crucial aspect of many mechanical systems. These bearings are used to support high loads and offer high levels of rotational accuracy and rigidity. They are designed to conserve space and save material costs.

The design of a cross roller bearing is unique in that it combines two sets of races and rollers, brought together at right angles with alternate rollers facing in opposite directions. This design allows for just one bearing to receive loads in all directions, including radial, axial, and moment loads. The rollers are held in place with a cage, preventing roller-to-roller contact, which increases friction and wear.
Cross roller bearings are commonly used in motion control applications that require fast acceleration and deceleration. They are a popular choice for robotics, machine tools, and other high-precision applications. The design of these bearings allows for high load capacity and accuracy while minimizing the space required for the bearing.
Fundamentals of Cross Roller Bearings

Cross roller bearings are a type of rolling-element bearing that has cylindrical rollers arranged perpendicular to each other in a cross pattern. These bearings are known for their high rigidity, accuracy, and load-bearing capacity. In this section, we will discuss the design principles, roller characteristics, and material selection of cross roller bearings.
Design Principles
Cross roller bearings are designed to handle both radial and axial loads simultaneously. They achieve this by having the rollers placed in a cross pattern, which allows for a large number of rollers to be used in a compact space. The rollers are held in place by a cage or separator that keeps them evenly spaced and prevents them from touching each other.
The design of cross roller bearings also allows for high precision and accuracy. The rollers are ground to very tight tolerances, and the bearing itself is designed to minimize any play or deflection. This makes cross roller bearings ideal for use in applications that require precise positioning or motion control.
Roller Characteristics
The rollers used in cross roller bearings are typically cylindrical in shape, with a length that is greater than their diameter. The rollers are ground to very tight tolerances, which ensures that they are all the same size and shape. This is important because any variation in the size or shape of the rollers can cause uneven loading and premature wear.
The rollers in cross roller bearings are also designed to have a large contact area with the raceway. This allows them to distribute the load over a larger area, which reduces stress and wear. The rollers are typically made from high-quality bearing steel, which provides excellent hardness and wear resistance.
Material Selection
The materials used in the construction of cross roller bearings are critical to their performance and longevity. The raceways are typically made from high-quality bearing steel, which provides excellent hardness, wear resistance, and fatigue strength. The rollers are also made from high-quality bearing steel, as well as other materials such as ceramics or polymers in some cases.
The cage or separator that holds the rollers in place is typically made from a lightweight and durable material such as brass or synthetic resin. The choice of material for the cage or separator is important because it affects the overall weight and stiffness of the bearing.
In summary, cross roller bearings are designed to handle both radial and axial loads simultaneously and achieve high precision and accuracy. The rollers used in these bearings are cylindrical in shape, ground to tight tolerances, and have a large contact area with the raceway. The materials used in the construction of cross roller bearings are critical to their performance and longevity.
Load Distribution and Performance

Dynamic and Static Load Ratings
Cross-roller bearings are designed to withstand both dynamic and static loads. The dynamic load rating (C) is the load capacity that the bearing can withstand for a specific duration of time without experiencing any permanent deformation. On the other hand, the static load rating (Co) is the maximum load that the bearing can withstand without undergoing any significant deformation. It is essential to note that the load ratings are affected by various factors such as the bearing’s size, material, and operating conditions.
Stress Analysis
To ensure that cross roller bearings can withstand the required loads, stress analysis is performed. Stress analysis involves calculating the stresses and deformations that the bearing undergoes when subjected to different loads. The results of the stress analysis are then used to optimize the bearing’s design to ensure that it can withstand the required loads without undergoing any permanent deformation.
Load Distribution
Load distribution is a critical factor that affects the performance and lifespan of cross roller bearings. The load distribution in cross roller bearings is affected by various factors such as the bearing’s size, material, and operating conditions. To ensure that the load distribution is optimal, the bearing’s design is optimized using various techniques such as finite element analysis (FEA) and experimental testing.
In conclusion, cross roller bearings are designed to withstand both dynamic and static loads. Stress analysis is performed to ensure that the bearing can withstand the required loads without undergoing any permanent deformation. Load distribution is a critical factor that affects the performance and lifespan of cross roller bearings, and the bearing’s design is optimized to ensure that the load distribution is optimal.
Precision and Accuracy
Cross roller bearings are designed to provide high precision and accuracy in linear motion applications. The following subsections discuss key factors that contribute to the precision and accuracy of cross roller bearings.
Manufacturing Tolerances
The manufacturing tolerances of cross roller bearings are critical to achieving high precision and accuracy. The bearing components must be manufactured to tight tolerances to ensure that they fit together perfectly. For example, the rollers and raceways must be ground to precise dimensions and surface finishes to minimize friction and wear. The bearing rings must also be machined to precise dimensions and roundness to ensure proper alignment and load distribution.
Preload and Rigidity
Preload is the amount of internal clearance that is eliminated from the bearing when it is assembled. Preloading cross roller bearings increases their rigidity and reduces their deflection under load, which improves their precision and accuracy. The amount of preload required depends on the application requirements and the bearing size. Manufacturers typically provide preload values for their bearings based on the expected operating conditions.
Running Accuracy
Running accuracy refers to the ability of cross roller bearings to maintain their precision and accuracy over time. Factors that affect running accuracy include bearing wear, lubrication, and temperature. Proper lubrication is critical to reducing friction and wear, which can degrade the running accuracy of the bearing. Temperature also affects the running accuracy of cross roller bearings, as thermal expansion can cause changes in the bearing dimensions and internal clearances.
In summary, the precision and accuracy of cross roller bearings are critical to their performance in linear motion applications. Manufacturing tolerances, preload, and running accuracy are key factors that contribute to the precision and accuracy of these bearings. By understanding these factors, you can select the right cross roller bearing for your application and ensure that it performs reliably and accurately over time.
Mounting and Installation
When it comes to mounting and installing cross roller bearings, there are a few important factors to consider. In this section, we will discuss fitting practices, alignment, lubrication, and sealing.
Fitting Practices
Proper fitting practices are essential for ensuring that cross roller bearings operate as intended. Before installation, it is important to ensure that the shaft and housing are clean and free from any burrs or nicks. Additionally, the bearing should be inspected for any damage or wear.
When fitting the bearing onto the shaft or into the housing, it is important to use the appropriate tools and techniques to avoid damaging the bearing or the mating surfaces. A press or hydraulic fitting tool is often used to apply a controlled force to the bearing, ensuring that it is seated properly.
Alignment
Proper alignment is critical for ensuring that cross roller bearings operate smoothly and efficiently. Misalignment can lead to increased wear and premature failure of the bearing.
To ensure proper alignment, it is important to use the appropriate mounting method and to follow the manufacturer’s recommendations. Additionally, it is important to verify the alignment using a dial indicator or other appropriate measuring tool.
Lubrication and Sealing
Proper lubrication and sealing are essential for ensuring that cross roller bearings operate smoothly and efficiently. The appropriate lubricant should be selected based on the operating conditions and the manufacturer’s recommendations.
Additionally, the bearing should be properly sealed to prevent contamination and to retain the lubricant. Sealing options include shields, seals, and integrated sealing systems.
In summary, proper fitting practices, alignment, lubrication, and sealing are essential for ensuring that cross roller bearings operate smoothly and efficiently. By following the manufacturer’s recommendations and using appropriate tools and techniques, you can ensure that your bearings provide reliable performance over their service life.
Applications and Case Studies
Industrial Applications
Cross roller bearings are widely used in various industrial applications due to their high load capacity and precise motion control. They are commonly used in machine tools, robotics, and medical equipment. In machine tools, they are used in spindles, rotary tables, and other rotating components. In robotics, they are used in joints and other motion control components. In medical equipment, they are used in imaging devices, surgical robots, and other precision instruments.
Cross roller bearings are also used in the aerospace industry, where they are used in aircraft engines, landing gear, and other critical components. They are preferred over other types of bearings due to their high stiffness, low friction, and high accuracy. They are also used in the defense industry, where they are used in missile guidance systems, radar antennas, and other applications that require precise motion control.
Innovative Uses
Cross roller bearings have also found innovative uses in various fields. For example, they are used in the design of telescopes, where they are used to support the primary mirror. They are also used in the design of wind turbines, where they are used to support the rotor blades. In addition, they are used in the design of solar trackers, where they are used to support the solar panels and track the movement of the sun.
Cross roller bearings are also used in the design of high-speed trains, where they are used to support the wheels and provide a smooth ride. They are also used in the design of amusement park rides, where they are used to provide precise motion control and ensure rider safety.
Case Study Examples
One example of the use of cross roller bearings is in the design of surgical robots. Surgical robots are used in minimally invasive surgery, where they provide precise motion control and reduce the risk of complications. Cross roller bearings are used in the joints of the robot, where they provide high stiffness and accuracy. They are also used in the end-effectors, where they provide precise motion control and reduce the risk of tissue damage.
Another example of the use of cross roller bearings is in the design of machine tools. Machine tools are used in the manufacturing industry, where they are used to produce precision parts. Cross roller bearings are used in the spindles and rotary tables of the machine tools, where they provide high stiffness and accuracy. They are also used in the linear guides, where they provide smooth and precise motion control.
Overall, cross roller bearings are versatile components that can be used in a wide range of applications. They provide high load capacity, precise motion control, and low friction, making them ideal for use in various industrial and innovative applications.