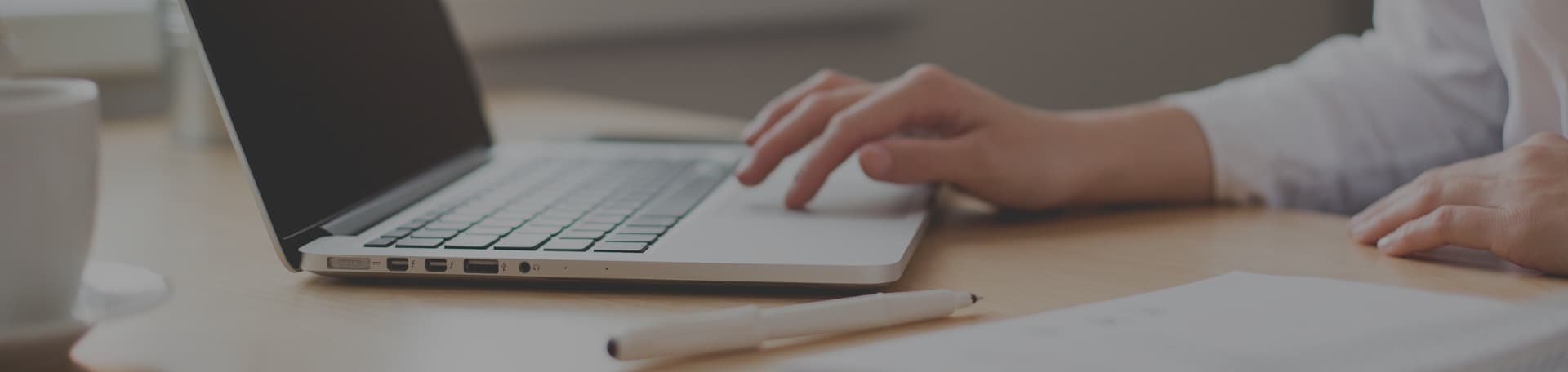
Excavator Slewing Gear: Understanding Its Function and Maintenance
Excavator Slewing Gear: Understanding Its Function and Maintenance
If you are involved in the construction industry, you have likely heard of an excavator. An excavator is a heavy-duty machine that is used to dig, move, and lift large amounts of soil, debris, and other materials. It is an essential tool for any construction project, and its functionality is dependent on various components, including the excavator slewing gear.

The excavator slewing gear is a critical component of an excavator that enables it to rotate or swing horizontally. It is a large ring-shaped gear that is mounted on the excavator’s body and allows the operator to move the arm and bucket in a full circle. The slewing gear’s design is complex and consists of several interlocking parts that work together to provide smooth, efficient movement. Its primary function is to transfer the torque generated by the excavator’s engine to the machine’s arm and bucket, allowing it to excavate and transport materials with ease.
Excavator Slewing Gear Overview

Function and Importance
The excavator slewing gear is a critical component of an excavator that enables it to rotate 360 degrees. This gear is responsible for transferring the power from the swing motor to the upper structure of the excavator, allowing it to rotate on its axis. Without the slewing gear, the excavator would be unable to perform many of its functions, such as digging, lifting, and moving materials.
Key Components
The excavator slewing gear consists of several key components that work together to enable smooth and efficient rotation. These include:
- Slewing Ring: The slewing ring is a large bearing that supports the weight of the upper structure of the excavator and enables it to rotate. It is typically made of high-strength steel and is designed to withstand heavy loads and extreme operating conditions.
- Slewing Drive: The slewing drive is a gearbox that is mounted on the excavator’s upper structure and is connected to the swing motor. It converts the rotational motion of the swing motor into the horizontal rotation of the slewing ring.
- Slewing Motor: The slewing motor is responsible for providing the rotational power that drives the slewing gear. It is typically a hydraulic motor that is controlled by the excavator’s hydraulic system.
Proper maintenance and regular inspection of the excavator slewing gear is crucial to ensure its smooth operation and longevity. Any wear or damage to the slewing ring, slewing drive, or slewing motor can result in reduced performance, increased downtime, and costly repairs.
Design and Manufacturing

Materials Used
Excavator slewing gears are usually made of high-quality steel, which is known for its durability and strength. The steel used in the manufacturing of excavator slewing gears is usually heat-treated to improve its strength and resistance to wear and tear. The heat treatment process involves heating the steel to a high temperature and then quenching it in oil or water. This process helps to harden the steel and improve its toughness.
In addition to steel, other materials such as bronze and aluminum can be used in the manufacturing of excavator slewing gears. Bronze is a popular choice for the manufacture of the bearing races, while aluminum is used for the manufacture of the gear teeth. These materials are chosen for their strength, durability, and resistance to wear and tear.
Engineering Principles
The design of excavator slewing gears is based on engineering principles that take into account the loads and stresses that the gears will be subjected to during operation. The gears must be designed to withstand the forces generated by the excavator’s weight, the weight of the load being lifted, and the torque generated by the engine.
To ensure that the gears are designed to withstand these forces, engineers use computer-aided design (CAD) software to model the gears and simulate their performance under different load conditions. The CAD software allows engineers to optimize the design of the gears and ensure that they are strong enough to withstand the loads and stresses they will be subjected to.
During the manufacturing process, the gears are machined to precise tolerances to ensure that they fit together perfectly and operate smoothly. The gears are also inspected at various stages of the manufacturing process to ensure that they meet the required quality standards.
In conclusion, the design and manufacturing of excavator slewing gears involves the use of high-quality materials and engineering principles to ensure that the gears are strong, durable, and able to withstand the loads and stresses they will be subjected to during operation.
Operation and Control
Slewing Mechanism
The slewing mechanism is an essential component of an excavator, allowing the upper structure of the machine to rotate 360 degrees. The mechanism consists of a slewing gear ring and a driving pinion, which is mounted on the output shaft of a low-speed, high-torque hydraulic motor. The slewing gear ring is supported by a rolling bearing, which enables the upper structure to rotate smoothly and efficiently.
Control Systems
Excavator slewing gear can be controlled by a variety of systems, including manual, hydraulic, and electronic controls. Manual controls are typically operated by levers or joysticks located in the operator’s cab, while hydraulic controls use hydraulic fluid to move the slewing mechanism. Electronic controls use sensors and software to monitor and control the movement of the upper structure.
The type of control system used will depend on the type of excavator and the specific application. For example, smaller excavators may have manual controls, while larger machines may use hydraulic or electronic controls for greater precision and efficiency. Regardless of the type of control system used, it is important to ensure that it is properly maintained and calibrated to ensure safe and reliable operation.
In summary, the slewing mechanism and control systems are critical components of an excavator that enable the upper structure to rotate and perform a variety of tasks. Proper maintenance and calibration of these systems is essential for safe and efficient operation of the machine.
Maintenance and Troubleshooting
Regular Maintenance Procedures
To keep your excavator slewing gear working smoothly and efficiently, it is important to perform regular maintenance procedures. Here are some key maintenance tasks to keep in mind:
- Lubrication: Regularly lubricate the slewing gear with the recommended grease. Refer to the manufacturer’s manual for the specific type of grease to use and the recommended intervals for lubrication. Over-lubrication can be just as harmful as under-lubrication, so be sure to follow the manufacturer’s guidelines.
- Inspection: Regularly inspect the slewing gear for any signs of wear or damage. Look for cracks, chips, or other signs of damage. If you notice any issues, it is important to address them promptly to prevent further damage.
- Cleaning: Keep the slewing gear clean and free of debris. Dirt and debris can cause wear and tear on the gear, so it is important to keep it clean. Use a soft-bristled brush to remove any dirt or debris.
Common Issues and Solutions
Even with regular maintenance, issues with the excavator slewing gear can still arise. Here are some common issues and solutions to keep in mind:
- Excessive Wear: If you notice excessive wear on the slewing gear, it may be due to overloading or improper lubrication. Check the manufacturer’s manual for the recommended load capacity and lubrication intervals. If the issue persists, it may be necessary to replace the slewing gear.
- Sticking or Binding: If the slewing gear is sticking or binding, it may be due to debris or lack of lubrication. Clean the gear and ensure that it is properly lubricated. If the issue persists, it may be necessary to replace the slewing gear.
- Noise: If you hear unusual noise coming from the slewing gear, it may be due to wear or damage. Inspect the gear for any signs of wear or damage and address any issues promptly. If the issue persists, it may be necessary to replace the slewing gear.
By following these regular maintenance procedures and addressing any issues promptly, you can help ensure that your excavator slewing gear operates smoothly and efficiently.
Advancements and Innovations
Excavator slewing systems have undergone significant advancements and innovations in recent years. These advancements have led to increased efficiency and productivity in the construction industry. Here are some of the notable advancements and innovations in excavator slewing gear:
1. Automated Excavation
Automated excavation is a recent innovation that has revolutionized the construction industry. With this technology, excavators can be fully automated, reducing the need for human labor. Built Robotics is one of the companies that have aftermarket solutions to fully automate 15- to 60-ton excavators. This technology has made it possible to perform heavy-duty tasks with precision and efficiency.
2. Slewing Bearings
Slewing bearings have been around for centuries, but advancements in technology have made them more precise and efficient. Slewing bearings are critical components of excavator slewing systems, responsible for the excavator’s ability to rotate its upper structure. With the evolution of technology, slewing bearings have become more durable, low in service, and fail-safe. Liebherr, for example, offers a wide range of solutions for steering with worm gear, spur gear, and belt slew drives.
3. Design
Excavator slewing systems have undergone significant design changes in recent years. The design changes have led to increased maneuverability, precision, and efficiency. The design changes have also made excavators more compact, making them ideal for use in tight spaces. The design changes have also led to the development of excavators that can perform multiple tasks, reducing the need for multiple machines.
In conclusion, excavator slewing systems have undergone significant advancements and innovations in recent years. These advancements have led to increased efficiency and productivity in the construction industry. With the continued evolution of technology, we can expect to see more innovative solutions in the future.