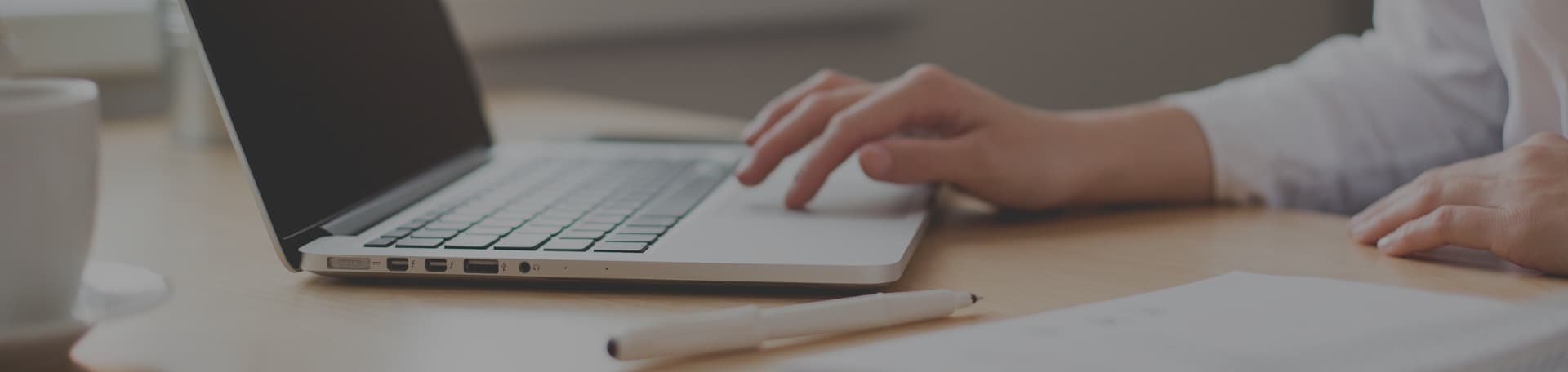
Heavy Duty Slewing Bearing: What You Need to Know
Heavy Duty Slewing Bearing: What You Need to Know
If you’re in the heavy-duty industry, you know the importance of having reliable equipment that can withstand the toughest conditions. One such component that plays a critical role in heavy-duty machinery is the slewing bearing. A slewing bearing, also known as a turntable bearing, is a large bearing that allows rotational movement of heavy equipment, such as cranes, excavators, and wind turbines.

A heavy-duty slewing bearing is designed to handle extreme stresses and forces encountered during swinging, rotating, and lifting. These bearings are available in a variety of mounting configurations and can be customized to meet specific application requirements. They are typically made of high-quality materials, such as forged steel, and are designed to provide long-lasting, reliable performance even in harsh environments. Whether you’re working in mining, construction, or other heavy-duty industries, a high-quality slewing bearing can help ensure that your equipment operates smoothly and efficiently.
Fundamentals of Heavy Duty Slewing Bearings

When it comes to heavy machinery, slewing bearings play a pivotal role in ensuring reliable and efficient operation. In this section, we will cover the design principles and load capabilities of heavy-duty slewing bearings.
Design Principles
Heavy-duty slewing bearings are designed to withstand high loads and provide stability to heavy machinery. These bearings consist of a single row or double row of balls or rollers and are available in various designs to meet the demands of particular applications.
Some of the design principles of heavy-duty slewing bearings include:
- Raceways: The bearing raceways, in conjunction with the rolling elements and cages or spacers, are designed to accommodate loads acting singly or in combination, and in any direction.
- Attachment: Slewing bearings typically include features for simple and quick attachment to those adjacent structures.
- Mechanical rotation: A feature to facilitate the mechanical rotation of one ring and its adjoining structure relative to the other.
Load Capabilities
Heavy-duty slewing bearings are capable of carrying significant loads and providing precise positioning for heavy machinery. The load capabilities of these bearings depend on various factors such as the bearing size, design, and operating conditions.
Some of the load capabilities of heavy-duty slewing bearings include:
- Axial load: The axial load capacity of a slewing bearing is the maximum load that can be applied parallel to the axis of rotation.
- Radial load: The radial load capacity of a slewing bearing is the maximum load that can be applied perpendicular to the axis of rotation.
- Tilting moment: The tilting moment capacity of a slewing bearing is the maximum moment that can be applied to the bearing without causing permanent deformation.
In summary, heavy-duty slewing bearings are essential components of heavy machinery, providing stability, load-carrying capacity, and precise positioning. The design principles and load capabilities of these bearings ensure reliable and efficient operation of heavy machinery.
Types of Heavy Duty Slewing Bearings

When it comes to heavy-duty machinery, slewing bearings play a crucial role in ensuring smooth rotation and handling extreme stresses and forces encountered during swinging, rotating, and lifting operations. There are three main types of heavy-duty slewing bearings: Single-Row Ball Type, Double-Row Ball Type, and Crossed Roller Type.
Single-Row Ball Type
Single-Row Ball Type slewing bearings are the most common type and are used in a wide range of applications. They consist of a single row of balls that are placed in a circular raceway. The balls are held in place by a cage, and the raceway is usually made of hardened steel. This type of slewing bearing is ideal for applications where low friction and high precision are required.
Double-Row Ball Type
Double-Row Ball Type slewing bearings are similar to Single-Row Ball Type bearings, but they have two rows of balls instead of one. This design allows for higher load-carrying capacity and improved stability. Double-Row Ball Type slewing bearings are commonly used in applications that require higher precision and heavier loads.
Crossed Roller Type
Crossed Roller Type slewing bearings are designed to handle both radial and axial loads. They consist of two sets of rollers that are crossed at a 90-degree angle. This design allows for high precision and rigidity, making them ideal for applications that require accurate positioning and heavy loads.
In summary, the type of heavy-duty slewing bearing you choose will depend on the specific requirements of your application. Single-Row Ball Type bearings are ideal for low friction and high precision applications, while Double-Row Ball Type bearings are better suited for heavier loads and higher precision. Crossed Roller Type bearings are designed to handle both radial and axial loads and are ideal for applications that require high precision and rigidity.
Applications and Industries
Slewing bearings are used in a wide range of industries due to their ability to support controlled rotation and manage heavy loads. Here are some of the industries and applications where heavy-duty slewing bearings are commonly used:
Construction Machinery
Slewing bearings are integral components in cranes, excavators, and concrete pumps, enabling smooth and stable movement of heavy equipment. These bearings are also used in tunnel boring machines, pile drivers, and drilling rigs. The heavy-duty machinery used in construction requires considerable load-bearing abilities and smooth rotation, which is why slewing bearings are prevalent in this industry.
Wind Turbines
Slewing bearings are critical components in wind turbines, enabling the rotation of the blades and the yaw mechanism. The yaw mechanism allows the turbine to turn and face the wind, optimizing energy production. Slewing bearings used in wind turbines are designed for extreme conditions, including high winds and harsh weather.
Marine Cranes
Slewing bearings are used in the construction of marine cranes, which are used in the shipping and offshore industries. These cranes are used for loading and unloading cargo, as well as for the installation and maintenance of offshore structures. The heavy loads and harsh marine environment require bearings that can withstand extreme conditions, making slewing bearings an ideal choice.
In summary, heavy-duty slewing bearings are used in a variety of industries and applications, including construction machinery, wind turbines, and marine cranes. These bearings are designed to support controlled rotation and manage heavy loads, making them an essential component in many heavy-duty machines and equipment.
Installation and Maintenance
When it comes to heavy-duty slewing bearings, proper installation and maintenance are crucial to ensure optimal performance and longevity. In this section, we will cover the key aspects of installing and maintaining your slewing bearings to help you get the most out of your investment.
Mounting Procedures
Mounting your slewing bearing correctly is critical to ensuring its longevity and optimal performance. Before installation, check the bearing for physical damage and ensure that it is mounted in an unloaded condition. Use eye bolts to lift the bearing, ensuring that they are fully threaded into the bolt hole and that the minimum thread engagement is 1.5 times the bolt diameter.
The bearing mounting surfaces must be machined flat after all welding and stress relief treatment on the structures is complete. If subsequent welding is necessary, it must be carried out after the bearing has been mounted. Correct alignment is also crucial to avoid excessive load on the bearing. Ensure that the slewing ring bearing is properly aligned with the mating components.
Lubrication and Care
Proper lubrication is essential to the longevity of your slewing bearing. Use the recommended lubricant and follow the manufacturer’s instructions for lubrication frequency and quantity. Over-lubrication can be just as harmful as under-lubrication, so be sure to follow the recommended guidelines.
In addition to lubrication, proper care is also important. Avoid impacts or drops during handling and always follow safe handling procedures. Keep the bearing clean and free of debris, and inspect it regularly for signs of wear or damage.
Inspection and Replacement
Regular inspection is crucial to detecting any issues with your slewing bearing before they become major problems. Inspect the bearing for wear, damage, or corrosion, and replace any damaged or worn components promptly.
When replacing components, be sure to use genuine parts from the manufacturer. Improper replacement parts can lead to premature wear and failure of the bearing.
By following these installation and maintenance procedures, you can ensure the longevity and optimal performance of your heavy-duty slewing bearing.
Selection Criteria
When selecting a heavy-duty slewing bearing, there are several factors to consider. These factors include size and torque requirements, material and coating options, and sealing solutions.
Size and Torque Requirements
The size and torque requirements of the slewing bearing are crucial to its performance. It is important to select a bearing that can handle the load and torque of the application. To determine the size and torque requirements, you should consider the weight of the load, the speed of rotation, and the forces acting on the bearing.
Material and Coating Options
The material and coating options of the slewing bearing can affect its durability and resistance to wear. Common materials for slewing bearings include steel and aluminum. Steel is a popular choice due to its strength and durability. Aluminum is a lighter option that can be used in applications where weight is a concern. Coatings such as corrosion-resistant coatings and hardening treatments can also be applied to increase the lifespan of the bearing.
Sealing Solutions
Sealing solutions are important to prevent contaminants from entering the bearing and causing damage. There are several types of sealing solutions available, including labyrinth seals, lip seals, and magnetic seals. Labyrinth seals are effective at preventing contaminants from entering the bearing, but they can create additional friction. Lip seals are a good option for low-speed applications, but they may not be as effective at preventing contaminants from entering the bearing. Magnetic seals use a magnetic field to prevent contaminants from entering the bearing, making them a good option for high-speed applications.
Overall, selecting the right heavy-duty slewing bearing requires careful consideration of the size and torque requirements, material and coating options, and sealing solutions. By taking these factors into account, you can ensure that the slewing bearing will perform optimally in your application.