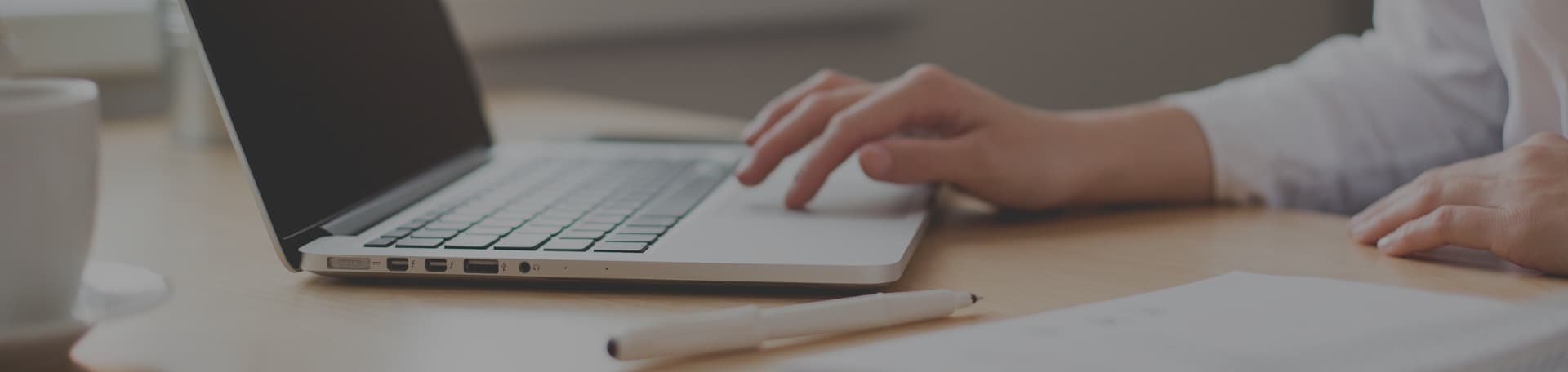
Plain Bearing Turntable: A Guide to its Function and Benefits
Plain Bearing Turntable: A Guide to its Function and Benefits
If you’re in the market for a turntable bearing, you’ll likely come across two types: plain bearing and ball bearing. In this article, we’ll focus on plain bearing turntables and discuss their installation, maintenance, and advantages.

Plain bearing turntables, also known as sleeve bearing turntables, use a cylindrical sleeve instead of balls to support the rotating platform. The sleeve is made of a self-lubricating material such as oil-impregnated bronze or plastic, which reduces friction and wear. Plain bearing turntables are often used in low-speed applications where precision is not critical, such as in lazy susans or display cases.
One of the main advantages of plain bearing turntables is their simplicity. They have fewer parts than ball bearing turntables, which means they are easier to install and maintain. In addition, they are often less expensive than ball bearing turntables, making them a cost-effective solution for many applications. However, it’s important to note that plain bearing turntables are not suitable for high-speed or high-precision applications.
Fundamentals of Plain Bearing Turntables

If you’re looking for a turntable that is simple, reliable, and cost-effective, then a plain bearing turntable might be the right choice for you. Plain bearing turntables are designed to handle axial and radial loads, and they are typically used in low-speed applications that require controlled rotation.
One of the key benefits of plain bearing turntables is their simplicity. Unlike other types of bearings, plain bearings do not have rolling elements, which means there are fewer parts that can wear out or fail. This makes plain bearing turntables easy to maintain and repair, and it also makes them less expensive than other types of bearings.
Another benefit of plain bearing turntables is their versatility. Because they do not have rolling elements, plain bearings can be made from a wide range of materials, including metals, plastics, and composites. This means that plain bearing turntables can be used in a variety of environments, from clean rooms to harsh outdoor conditions.
However, there are some limitations to plain bearing turntables. Because they do not have rolling elements, plain bearings have higher friction than other types of bearings, which can result in increased wear and reduced efficiency. Additionally, plain bearings require lubrication to reduce friction and prevent wear, which can be a maintenance challenge.
Overall, plain bearing turntables are a simple, reliable, and cost-effective choice for low-speed applications that require controlled rotation. If you’re looking for a turntable that is easy to maintain and repair, and that can be used in a variety of environments, then a plain bearing turntable might be the right choice for you.
Design and Material Considerations

When designing a plain bearing turntable, there are several key considerations to keep in mind. These include the choice of materials and design features that will be used to ensure the bearing operates effectively and efficiently.
Material Types
The choice of materials for a plain bearing turntable is critical to its performance. The most common materials used for plain bearings include bronze, steel, and plastic. Bronze is a popular choice due to its high strength and resistance to wear, but it is also more expensive than other materials. Steel is another popular choice due to its strength and durability, but it can be prone to corrosion if not properly protected. Plastic bearings are also an option, and they are often chosen for their low cost and resistance to corrosion. However, they may not be as durable as other materials and may be prone to wear.
Design Features
In addition to material selection, there are several key design features that should be considered when designing a plain bearing turntable. These include the bearing’s size, shape, and the type of lubrication used. The size of the bearing will depend on the size of the turntable and the load it will be carrying. The shape of the bearing can also impact its performance, with some shapes offering better load distribution and reduced friction. Lubrication is also critical to the performance of a plain bearing turntable. Proper lubrication can reduce friction and wear, prolonging the life of the bearing. The type of lubrication used will depend on the specific application and the materials used in the bearing.
Overall, when designing a plain bearing turntable, it is important to consider both the materials used and the design features of the bearing. By selecting the right materials and incorporating key design features, you can ensure that your plain bearing turntable operates effectively and efficiently.
Manufacturing Processes
When it comes to manufacturing plain bearing turntables, there are several processes involved. These processes are designed to ensure that the final product is of the highest quality and meets the required specifications. Here are some of the manufacturing processes involved in producing plain bearing turntables:
1. Material Selection
The first step in the manufacturing process is to select the appropriate materials. Plain bearing turntables are usually made from materials such as steel, bronze, and plastic. The material used depends on the application and the load capacity required. For example, steel is a popular choice for heavy-duty applications, while plastic is often used for lighter loads.
2. Machining
After the materials have been selected, the next step is machining. This involves cutting, drilling, and shaping the materials to the required dimensions. Machining is a critical process that requires precision and accuracy to ensure that the turntable bearing operates smoothly.
3. Heat Treatment
Heat treatment is another important process in the manufacturing of plain bearing turntables. This process involves heating the materials to a specific temperature and then cooling them down slowly. Heat treatment improves the strength and durability of the materials, making them more resistant to wear and tear.
4. Assembly
Once the machining and heat treatment processes are complete, the next step is assembly. This involves putting together the various components of the plain bearing turntable, such as the inner and outer rings, the balls or rollers, and the cage. Assembly is a delicate process that requires precision and care to ensure that the turntable bearing operates smoothly.
Overall, the manufacturing of plain bearing turntables is a complex process that requires expertise and attention to detail. By following these processes, manufacturers can produce high-quality turntable bearings that meet the required specifications and provide reliable performance.
Applications and Uses
Plain bearing turntables have a wide range of applications in various industries and consumer products. Here are some of the most common uses of plain bearing turntables:
Industrial Applications
Plain bearing turntables are widely used in industrial applications that require controlled rotation and distribution of heavy loads while maintaining stability and reliability. Some of the most common industrial applications of plain bearing turntables include:
- Robotics: Plain bearing turntables are used in industrial robots to provide smooth and precise rotation of the robot arm.
- Construction: Plain bearing turntables are used in construction equipment such as cranes, excavators, and backhoes to provide smooth rotation of the equipment.
- Manufacturing: Plain bearing turntables are used in manufacturing equipment such as assembly lines, conveyor systems, and packaging machines to provide controlled rotation and distribution of heavy loads.
Consumer Products
Plain bearing turntables are also used in various consumer products that require controlled rotation and stability. Some of the most common consumer products that use plain bearing turntables include:
- Microwave ovens: Plain bearing turntables are used in microwave ovens to provide smooth and even rotation of the food being cooked.
- Lazy Susans: Plain bearing turntables are used in Lazy Susans to provide smooth and easy rotation of the items placed on them.
- Display cases: Plain bearing turntables are used in display cases to provide smooth and controlled rotation of the items being displayed.
In summary, plain bearing turntables have a wide range of applications in various industries and consumer products. They provide controlled rotation and distribution of heavy loads while maintaining stability and reliability.
Maintenance and Lubrication
Maintaining and lubricating your plain bearing turntable is essential for ensuring its longevity and optimal performance. Proper maintenance and lubrication can prevent wear and tear on the bearing, reduce friction, and keep your turntable running smoothly.
To maintain your turntable, it is recommended to clean the bearing regularly. Use a soft cloth to wipe away any dust or debris that may have accumulated on the bearing. Avoid using any harsh chemicals or abrasive materials that could damage the bearing.
Lubricating your turntable bearing is also crucial for its smooth operation. It is recommended to use a high-quality oil or grease specifically designed for turntable bearings. Pro-Ject Audio Systems recommends checking the oil film on the bearing from time to time to ensure it is sufficient. If the oil film is insufficient, it is recommended to apply a thin layer of oil or grease to the bearing.
It is important to note that over-lubricating the bearing can be just as detrimental as under-lubricating it. Too much oil or grease can cause excess friction, leading to premature wear and tear on the bearing. Therefore, it is important to apply only a thin layer of oil or grease to the bearing.
In summary, proper maintenance and lubrication are crucial for the optimal performance and longevity of your plain bearing turntable. Clean the bearing regularly and use a high-quality oil or grease specifically designed for turntable bearings. By following these simple steps, you can ensure that your turntable operates smoothly and lasts for years to come.
Selection and Sizing Criteria
When selecting plain bearing turntables, there are several criteria that you should consider to ensure that you get the right product for your application. Here are some of the most important factors to keep in mind:
Load Capacity
The load capacity of the turntable is the maximum amount of weight that it can support. This is a critical factor to consider when selecting a turntable for your application. You should ensure that the turntable you choose can handle the weight of your load.
Size
The size of the turntable is another important factor to consider. You should choose a turntable that is the right size for your application. If the turntable is too small, it may not be able to support your load. If it is too large, it may take up more space than necessary.
Material
The material of the turntable is also important. You should choose a turntable that is made of a material that is appropriate for your application. For example, if you are using the turntable in a corrosive environment, you may need a turntable that is made of a corrosion-resistant material.
Lubrication
Lubrication is critical for the proper operation of plain bearing turntables. You should ensure that the turntable is properly lubricated to ensure that it operates smoothly and efficiently. You should also consider the type of lubrication that is appropriate for your application. For example, if you are using the turntable in a food processing application, you may need to use food-grade lubricants.
Operating Environment
The operating environment is also an important factor to consider. You should choose a turntable that is appropriate for the environment in which it will be used. For example, if the turntable will be used outdoors, you may need a turntable that is designed to withstand exposure to the elements.
By considering these factors when selecting and sizing plain bearing turntables, you can ensure that you get the right product for your application.