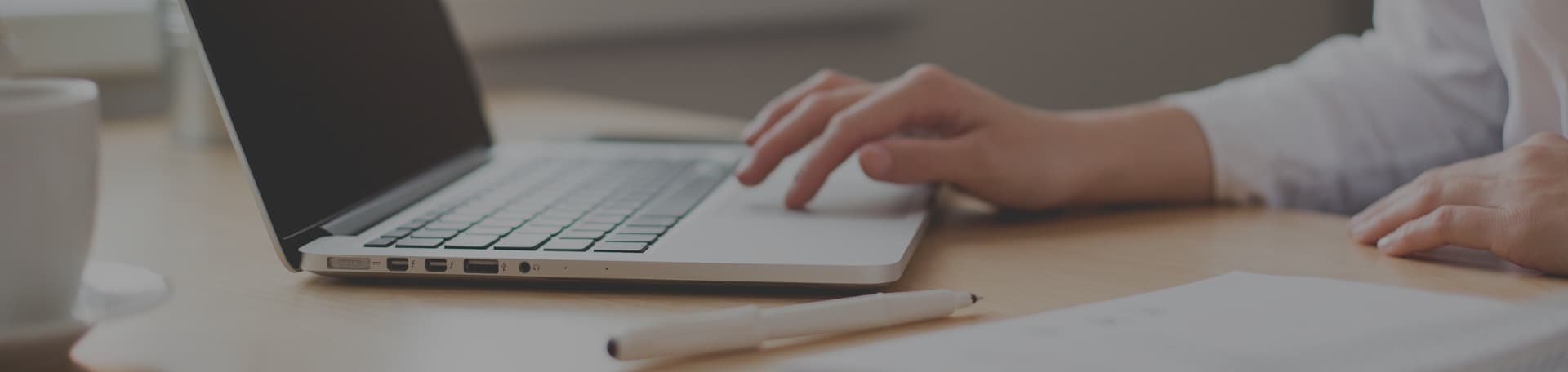
Precision Turntable Bearing: A Guide to Choosing the Right One
Precision Turntable Bearing: A Guide to Choosing the Right One
If you’re in the market for high-precision turntable bearings, you’ve come to the right place. Precision turntable bearings are designed to handle both radial and axial loads while maintaining stability and reliability. They play a vital role in applications that require controlled rotation and the distribution of heavy loads.

One of the most important factors to consider when selecting a precision turntable bearing is its load capacity. This refers to the maximum amount of weight that the bearing can support without breaking down or failing. Other important factors to consider include the bearing’s diameter, precision, and profile. Some precision turntable bearings are designed to accommodate miniature applications, while others are designed for heavy-duty industrial applications.
Whether you’re looking for a miniature high-precision turntable bearing or an industrial turntable bearing, there are many options available on the market. It’s important to choose a bearing that is designed to meet your specific needs and requirements. By taking the time to research your options and select a high-quality precision turntable bearing, you can ensure that your application runs smoothly and efficiently.
Fundamentals of Precision Turntable Bearings

Precision turntable bearings are designed to provide precise rotation and positioning capabilities while supporting high axial and radial loads. These bearings are widely used in various industrial applications, including machine tools, robotics, and medical equipment. In this section, we will discuss the design principles and material selection considerations for precision turntable bearings.
Design Principles
Precision turntable bearings consist of an inner and outer ring, rolling elements, a cage, and seals. The design of these bearings is critical to their performance, and several factors must be considered during the design process.
One of the critical design principles is the selection of the bearing type, which depends on the application requirements, load capacity, and accuracy. There are several types of precision turntable bearings, including crossed roller bearings, four-point contact ball bearings, and three-row roller bearings. Each type has its unique advantages and disadvantages, and the selection depends on the specific application needs.
Another critical design principle is the selection of the bearing size, which depends on the load capacity, rotational speed, and accuracy requirements. The bearing size should be selected to ensure that the bearing can withstand the applied loads without deformation or failure.
Material Selection
The material selection is another critical aspect of the design of precision turntable bearings. The materials used for the inner and outer rings, rolling elements, cage, and seals must be carefully selected to ensure optimal performance and durability.
The material selection depends on several factors, including the application requirements, operating conditions, and cost. For example, high-carbon chrome bearing steel is commonly used for the inner and outer rings of precision turntable bearings because of its high strength and durability. The rolling elements are typically made of ceramic or steel, depending on the application requirements.
The cage material is also critical, as it affects the bearing’s speed, noise, and temperature. Phenolic resin cages are commonly used for high-speed applications due to their low friction and high-temperature resistance. Alternatively, brass cages are used for applications requiring high load capacity and low noise.
In summary, the design principles and material selection are critical aspects of the design of precision turntable bearings. By carefully considering these factors, engineers can ensure that the bearings meet the application requirements and provide optimal performance and durability.
Types of Precision Turntable Bearings
When it comes to precision turntable bearings, there are two main types: ball bearing turntables and roller bearing turntables. Each type has its own unique advantages and disadvantages, and the choice between the two will depend on the specific application and requirements.
Ball Bearing Turntables
Ball bearing turntables are the most common type of precision turntable bearing. They consist of a series of balls that run along a track, allowing for smooth and precise rotation. Ball bearings are ideal for applications that require high-speed rotation and low friction. They are also relatively low cost and easy to maintain.
One advantage of ball bearing turntables is their ability to handle both radial and axial loads. This makes them versatile and suitable for a wide range of applications. However, they are not as durable as roller bearings and may wear out more quickly over time.
Roller Bearing Turntables
Roller bearing turntables use cylindrical rollers instead of balls to support the load and allow for rotation. Roller bearings are ideal for applications that require high load capacity and durability. They are also able to handle shock and vibration better than ball bearings.
One advantage of roller bearing turntables is their ability to handle heavier loads than ball bearings. They are also more durable and can last longer in harsh environments. However, they are typically more expensive than ball bearings and may require more maintenance.
In summary, ball bearing turntables are ideal for applications that require high-speed rotation and low friction, while roller bearing turntables are better suited for applications that require high load capacity and durability. The choice between the two will depend on the specific requirements of your application.
Applications and Uses
Precision turntable bearings have a wide range of applications across various industries. Here are some of the most common uses of precision turntable bearings.
High-Fidelity Audio Equipment
If you are an audiophile, you know how important precision is when it comes to audio equipment. Precision turntable bearings are used in high-end turntables to ensure smooth and accurate rotation of the platter. This results in better sound quality and reduced distortion. The bearings are designed to handle both radial and axial loads, which makes them ideal for use in turntables.
Industrial Machinery
Precision turntable bearings are also used in industrial machinery. They are commonly found in machines that require controlled rotation and the distribution of heavy loads. These bearings are ideal for applications that require high precision and low profile. They are also versatile and can be used in a wide range of industrial applications.
Precision turntable bearings are used in a variety of industrial machinery, including:
- Machine tools: The table on milling machines, lathes, grinders, etc. use rotary bearings to position workpieces.
- Robotics: Robot joints utilize rotary bearings for smooth rotation.
- Medical equipment: Precision turntable bearings are used in medical equipment that requires precise movement and control.
In summary, precision turntable bearings are essential components in a wide range of applications across various industries. They are designed to handle heavy loads while maintaining stability and reliability. Whether you are an audiophile or an industrial engineer, precision turntable bearings can help you achieve the precision and accuracy you need.
Maintenance and Care
Lubrication and Cleaning
Proper lubrication is essential for the longevity and performance of precision turntable bearings. You should lubricate your bearings regularly, as specified by the manufacturer. Over-lubrication can cause overheating, while under-lubrication can cause premature wear and tear. You can use either oil or grease for lubrication, depending on the type of bearing and the manufacturer’s recommendations.
Cleaning is also important for maintaining your turntable bearings. You should clean your bearings regularly to remove any dirt, dust, or debris that may have accumulated. Use a clean cloth or brush to wipe the bearing surface and remove any particles that may have stuck to it. Avoid using water or solvents for cleaning, as they can damage the bearing surface and cause corrosion.
Regular Inspection
Regular inspection is crucial for detecting any potential problems with your turntable bearings before they become serious. You should inspect your bearings regularly, as specified by the manufacturer. Look for signs of wear and tear, such as cracks, corrosion, or deformation. Check for any unusual noise or vibration, which may indicate a problem with the bearing.
You should also check the mounting bolts and fasteners regularly to ensure that they are tight and secure. Loose bolts or fasteners can cause misalignment and premature wear and tear. Use a torque wrench to tighten the bolts and fasteners to the manufacturer’s recommended torque values.
In conclusion, proper maintenance and care are essential for the longevity and performance of your precision turntable bearings. Regular lubrication, cleaning, and inspection can help prevent premature wear and tear and ensure that your bearings operate smoothly and efficiently.