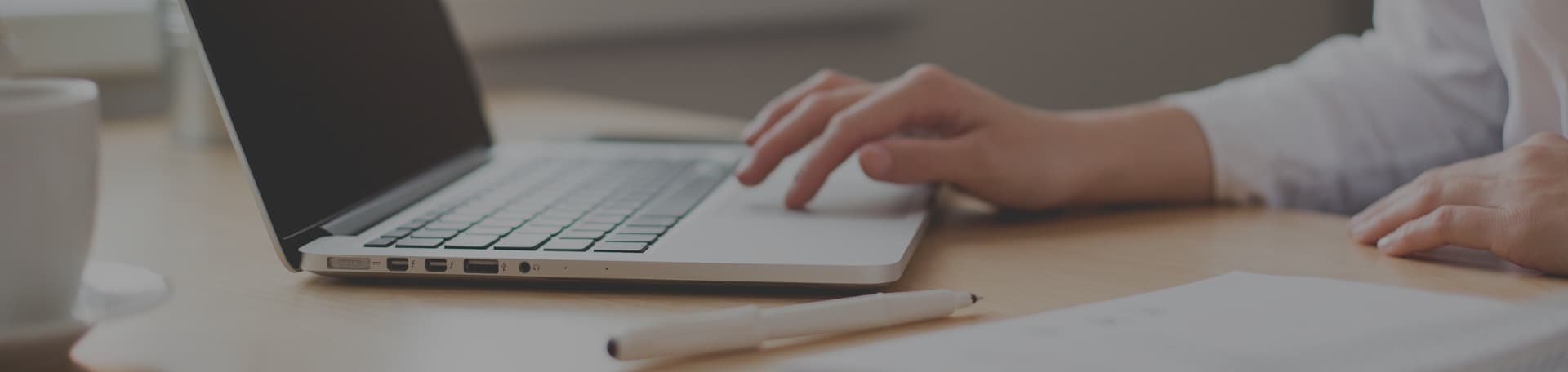
Ring Bearing Application: Understanding the Basics
Ring Bearing Application: Understanding the Basics
If you are looking to optimize power transmission, you may be interested in learning more about ring bearing applications. Slewing ring bearings, also known as turntable bearings, are ball or roller-style bearings that are composed of two concentric rings, either of which may include a gear. These bearings enhance load support and power transmission in all directions, and they are typically employed to support heavy loads for slow applications and large equipment such as earth movers, cranes, excavators, and wind turbines.
Slewing ring bearings are versatile and can be used in a wide range of applications. They can be customized to meet the demands of particular applications, with outside diameters ranging from 0.1 to 18 meters. SKF manufactures standard and customized slewing bearings in various designs to accommodate loads acting singly or in combination, and in any direction. Generally, slewing ring bearings are used where rotational speed is slow, intermittent, and oscillatory. The permissible speed limits for various Kaydon slewing ring bearings are shown on page 20 of their catalog.
Fundamentals of Ring Bearing Design

If you’re designing a machine that involves rotating shafts, you’ll need to select the right type of bearing to support the load. One of the most common types of bearings is the ring bearing, which is used in a wide range of applications, from electric motors to automotive engines.
Ring bearings are designed to support radial loads, which are forces that act perpendicular to the axis of rotation. They consist of two main parts: an outer ring and an inner ring, with rolling elements (such as balls or rollers) between them. The rolling elements reduce friction between the rings, allowing the shaft to rotate smoothly.
When selecting a ring bearing, there are several factors to consider, including load capacity, speed, and operating conditions. The load capacity of a bearing is determined by its size, geometry, and material. For example, larger bearings can support higher loads, while bearings made from high-strength materials can withstand heavier loads.
Speed is another important factor to consider, as higher speeds can cause increased friction and wear on the bearing. To minimize these effects, bearings are often designed with special materials and lubricants that can withstand high temperatures and speeds.
In addition to load capacity and speed, operating conditions are also important to consider when selecting a ring bearing. Factors such as temperature, moisture, and chemical exposure can all affect the performance and lifespan of a bearing. Therefore, it’s important to select a bearing that is designed to withstand the specific conditions of your application.
In summary, the design of a ring bearing is critical to the performance and reliability of your machine. By considering factors such as load capacity, speed, and operating conditions, you can select the right bearing for your application and ensure long-lasting, trouble-free operation.
Materials and Fabrication

Material Selection
The selection of materials for ring bearing applications is a critical factor in determining the performance and longevity of the bearing. The most common materials used for ring bearings are steel and ceramic. Steel is the most popular material due to its high strength, durability, and low cost. Ceramic bearings, on the other hand, offer superior performance in terms of speed, temperature resistance, and corrosion resistance. However, they are more expensive than steel bearings.
When selecting the material for a ring bearing, you should consider the load capacity, the operating temperature, the speed, and the environment in which the bearing will operate. For example, if the bearing will operate in a high-temperature environment, you should consider using a ceramic material. If the bearing will be exposed to corrosive chemicals, you should consider using a stainless steel material.
Manufacturing Processes
The manufacturing process of ring bearings involves several steps, including forging, turning, heat treatment, grinding, and assembly. The process begins with the forging of the raw material into the desired shape of the bearing. The next step is turning, which involves the machining of the bearing to the desired dimensions.
Heat treatment is a critical step in the manufacturing process as it determines the hardness, strength, and toughness of the bearing. The heat treatment process involves heating the bearing to a specific temperature and then cooling it at a specific rate. This process is repeated several times to achieve the desired properties.
Grinding is the final step in the manufacturing process and involves the precision grinding of the bearing surfaces to ensure a smooth and accurate finish. The bearing is then assembled by fitting the inner and outer rings, the rolling elements, and the cage together.
Overall, the material selection and manufacturing process are critical factors in determining the performance and longevity of a ring bearing. By selecting the right material and following the correct manufacturing process, you can ensure that your ring bearings will perform optimally and have a long service life.
Ring Bearing Applications
Ring bearings, also known as slewing bearings, are versatile components that are used in a wide range of applications. These bearings are capable of supporting heavy loads and facilitating smooth, precise motion in all directions. Here are some of the most common applications of ring bearings:
Industrial Machinery
Ring bearings are used extensively in industrial machinery applications, where they provide reliable support for heavy loads. These bearings are commonly used in cranes, excavators, and other types of heavy equipment. They are also used in conveyor systems, where they facilitate smooth, efficient movement of materials.
Automotive Systems
Ring bearings are used in a variety of automotive systems, including steering and suspension systems. These bearings are designed to provide stable support for heavy loads, while also allowing for smooth, precise motion. In addition, ring bearings are used in the construction of wind turbines, where they facilitate the smooth rotation of the blades.
Aerospace Components
Ring bearings are also used in a variety of aerospace applications, including satellite systems and space exploration vehicles. These bearings are designed to provide reliable support for heavy loads, while also withstanding the extreme temperatures and pressures of space travel. In addition, ring bearings are used in the construction of aircraft landing gear, where they provide stable support for heavy loads during takeoff and landing.
Overall, ring bearings are essential components in a wide range of applications, from industrial machinery to aerospace systems. Their ability to support heavy loads and facilitate smooth, precise motion makes them a critical component in many different types of equipment.
Performance and Lifespan
When it comes to ring bearing applications, performance and lifespan are two of the most important factors to consider. Understanding the load capacity and maintenance requirements of your bearing can help ensure optimal performance and a longer lifespan.
Load Capacity
The load capacity of a bearing refers to the amount of weight or force it can withstand without failure. It is important to choose a bearing with a load capacity that matches the requirements of your application. Overloading a bearing can cause premature wear and failure, while underloading a bearing can lead to poor performance and premature wear as well.
To determine the load capacity of a bearing, you need to consider the type of load it will be subjected to, such as radial or axial loads, and the direction and magnitude of the load. You can then use manufacturer-provided load ratings and calculations to select a bearing with the appropriate load capacity.
Maintenance and Reliability
Proper maintenance is essential for ensuring the reliability and longevity of ring bearings. Regular inspections and lubrication can help prevent premature wear and failure. It is important to follow the manufacturer’s recommended maintenance schedule and use the appropriate lubrication for your application.
In addition to regular maintenance, selecting a bearing with a proven track record of reliability can help ensure optimal performance and a longer lifespan. Look for bearings from reputable manufacturers with a history of producing high-quality products.
Overall, understanding the load capacity and maintenance requirements of your ring bearing application can help ensure optimal performance and a longer lifespan. By selecting a bearing with the appropriate load capacity and following the manufacturer’s recommended maintenance schedule, you can help prevent premature wear and failure and ensure reliable operation.
Installation and Alignment
When it comes to ring bearing application, proper installation and alignment are crucial for ensuring optimal performance and longevity. In this section, we will cover the two main aspects of installation and alignment: mounting techniques and alignment procedures.
Mounting Techniques
Ring bearings can be mounted in a variety of ways, including press fitting, shrink fitting, and adhesive bonding. The choice of mounting technique will depend on factors such as the size and type of bearing, the application, and the operating conditions.
Press fitting involves using a hydraulic press to apply force to the inner or outer ring of the bearing until it is securely seated on the shaft or housing. Shrink fitting involves heating the bearing and/or the shaft/housing to expand them and then allowing them to cool and contract, creating a tight fit. Adhesive bonding involves applying a special adhesive to the bearing and/or the shaft/housing and allowing it to cure, creating a strong bond.
Whichever mounting technique is used, it is important to follow the manufacturer’s instructions and use the correct tools and equipment to avoid damaging the bearing or the mounting surface.
Alignment Procedures
Proper alignment is essential for ensuring that the bearing operates smoothly and efficiently, and that it does not wear prematurely. There are several alignment procedures that can be used, including visual alignment, laser alignment, and dial indicator alignment.
Visual alignment involves visually inspecting the bearing and the mating components to ensure that they are properly aligned. Laser alignment uses a laser beam to measure the alignment of the bearing and the mating components. Dial indicator alignment uses a dial gauge to measure the alignment of the bearing and the mating components.
Whichever alignment procedure is used, it is important to ensure that the bearing is properly aligned in all directions (axial, radial, and angular) and that any misalignment is corrected before the bearing is put into service.
In conclusion, proper installation and alignment are critical for ensuring the optimal performance and longevity of ring bearings. By following the manufacturer’s instructions and using the correct tools and equipment, you can ensure that your bearings are installed and aligned correctly and will provide reliable service for years to come.