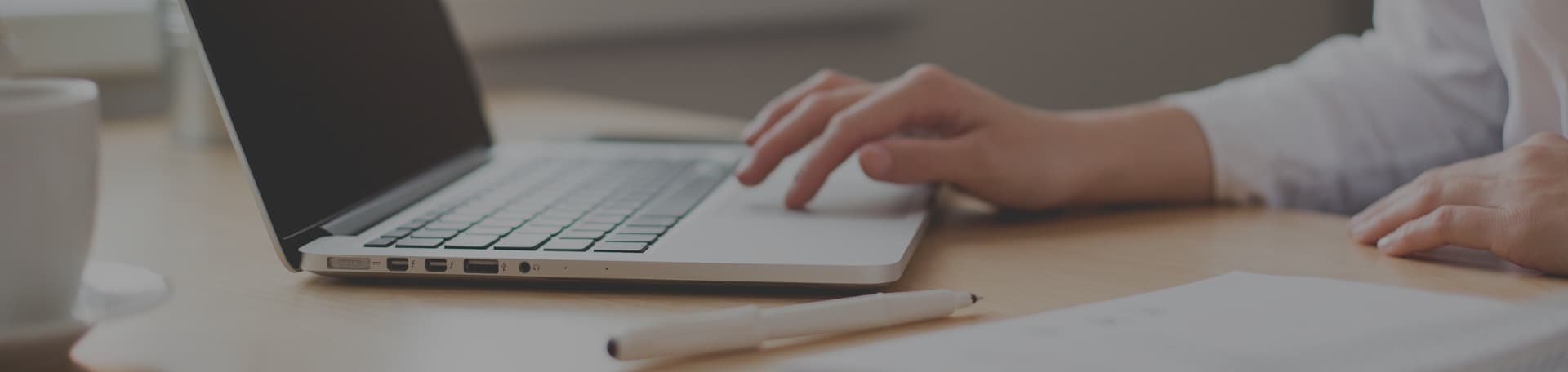
Ring Bearing Manufacturers: A Comprehensive Guide to the Top Brands in the Industry
Ring Bearing Manufacturers: A Comprehensive Guide to the Top Brands in the Industry
If you are in the market for ring bearings, you will need to find a reliable manufacturer who can provide you with high-quality products that meet your specific needs. There are many ring bearing manufacturers out there, each with their own strengths and weaknesses. Some specialize in certain types of bearings, while others offer a wide range of products to choose from.

When choosing a ring bearing manufacturer, it is important to consider factors such as the quality of their products, their reputation in the industry, and their level of customer service. You will also want to look for a manufacturer who can provide you with customized solutions that meet your specific needs. Whether you need a standard bearing or a custom design, a good manufacturer should be able to work with you to create the perfect product for your application.
Overall, finding the right ring bearing manufacturer is essential if you want to ensure that your equipment or machinery runs smoothly and efficiently. By doing your research and choosing a reputable manufacturer, you can feel confident that you are getting the best possible products and service for your money.
Overview of Ring Bearing Manufacturing

Ring bearings, also known as slewing bearings, are an essential component of many industrial machines. They allow for the smooth rotation of heavy loads and are commonly used in cranes, excavators, wind turbines, and many other applications. In this section, we will provide an overview of ring bearing manufacturing, including its history and evolution, the types of ring bearings available, and the materials used in their production.
History and Evolution
Ring bearings have been in use for centuries, with the earliest known examples dating back to ancient Greece. However, it wasn’t until the industrial revolution that ring bearings began to be mass-produced and used in a wide range of applications. Since then, they have undergone significant evolution, with new materials, designs, and manufacturing techniques continually being developed.
Types of Ring Bearings
There are several types of ring bearings available, each with its unique design and application. The most common types include four-point contact bearings, crossed roller bearings, and three-row roller bearings. Four-point contact bearings are the most commonly used type and are ideal for applications that require high load capacity and low torque. Crossed roller bearings, on the other hand, are ideal for applications that require high precision and stiffness. Three-row roller bearings are used in applications that require high load capacity and high stiffness.
Materials Used in Production
Ring bearings are typically made from high-quality steel, but other materials such as ceramics and plastics are also used. The choice of material depends on the specific application and the required performance characteristics. For example, steel bearings are ideal for applications that require high load capacity and durability, while ceramic bearings are ideal for applications that require high speed and low friction. Plastic bearings, on the other hand, are ideal for applications that require corrosion resistance and low weight.
In conclusion, ring bearings are a critical component of many industrial machines, and their manufacturing has a rich history and evolution. The type of bearing used and the materials used in its production depend on the specific application and performance requirements.
Manufacturing Processes

When it comes to producing high-quality ring bearings, manufacturers follow a strict set of processes to ensure the best possible results. These processes include design and engineering, machining and shaping, heat treatment, and assembly and testing.
Design and Engineering
The design and engineering phase is crucial to the success of the manufacturing process. During this phase, manufacturers work closely with clients to determine the specific requirements for the ring bearings. This includes factors such as load capacity, speed, and environmental conditions. Once the requirements are established, the manufacturer can begin designing the ring bearings to meet those specifications.
Machining and Shaping
Once the design is complete, the manufacturer can begin the machining and shaping process. This involves using specialized machinery and tools to shape the raw materials into the desired shape and size. The process may involve turning, grinding, and drilling the materials to achieve the final product.
Heat Treatment
After the machining and shaping process is complete, the ring bearings must undergo heat treatment. This involves heating the materials to a specific temperature and then cooling them rapidly to harden the metal. This process helps to increase the strength and durability of the ring bearings, ensuring they can withstand the demands of their intended application.
Assembly and Testing
The final step in the manufacturing process is assembly and testing. During this phase, the various components of the ring bearings are assembled and tested to ensure they meet the required specifications. This includes testing the bearings for load capacity, speed, and other factors to ensure they are suitable for their intended application.
Overall, the manufacturing process for ring bearings is a complex and intricate process that requires precision and attention to detail. By following these processes, manufacturers can produce high-quality ring bearings that meet the specific needs of their clients.
Global Market Leaders
When it comes to ring bearing manufacturers, there are a few companies that stand out as the global market leaders. These companies have established themselves as reliable and innovative suppliers of high-quality ring bearings. In this section, we will take a closer look at some of these companies and their offerings.
North America
One of the leading ring bearing manufacturers in North America is Timken Company. The company offers a wide range of bearing products, including ball bearings, cylindrical roller bearings, and tapered roller bearings. Timken has a strong reputation for quality and innovation, and their products are used in a variety of industries, including aerospace, automotive, and industrial.
Another major player in the North American market is SKF. The company offers a range of bearing products, including ball bearings, roller bearings, and plain bearings. SKF has a strong focus on research and development, and their products are known for their reliability and durability.
Europe
In Europe, one of the top ring bearing manufacturers is Schaeffler Group. The company offers a range of bearing products, including ball bearings, roller bearings, and plain bearings. Schaeffler Group has a strong focus on innovation, and their products are used in a variety of industries, including automotive, aerospace, and industrial.
Another major player in the European market is NSK Ltd. The company offers a range of bearing products, including ball bearings, roller bearings, and precision bearings. NSK has a strong reputation for quality and reliability, and their products are used in a variety of industries, including automotive, industrial, and medical.
Asia-Pacific
In the Asia-Pacific region, one of the top ring bearing manufacturers is NTN Corporation. The company offers a range of bearing products, including ball bearings, roller bearings, and precision bearings. NTN has a strong focus on research and development, and their products are known for their reliability and durability.
Another major player in the Asia-Pacific market is JTEKT Corporation. The company offers a range of bearing products, including ball bearings, roller bearings, and needle bearings. JTEKT has a strong reputation for quality and innovation, and their products are used in a variety of industries, including automotive, industrial, and aerospace.
Overall, these global market leaders are known for their quality, reliability, and innovation. Whether you are looking for ball bearings, roller bearings, or precision bearings, these companies are sure to have a product that meets your needs.
Quality Control and Standards
When it comes to ring bearing manufacturers, quality control and standards play a critical role in ensuring that the products meet the required specifications and standards. In this section, we will discuss the various certifications and regulations that ring bearing manufacturers must adhere to, as well as the testing procedures that they use to guarantee the quality of their products.
Certifications and Regulations
Ring bearing manufacturers must comply with various certifications and regulations to ensure that their products meet the required standards. Some of the most common certifications and regulations include ISO 9001:2015, RoHS, and REACH.
ISO 9001:2015 is an international standard that outlines the requirements for a quality management system. This certification ensures that the manufacturer has a robust quality management system in place to ensure that their products meet the required standards.
RoHS stands for Restriction of Hazardous Substances. This certification ensures that the manufacturer has eliminated or reduced the use of hazardous materials in their products, such as lead, cadmium, and mercury.
REACH stands for Registration, Evaluation, Authorization, and Restriction of Chemicals. This certification ensures that the manufacturer has registered all the chemicals used in their products and has taken the necessary steps to ensure that they are safe for human use.
Testing Procedures
Ring bearing manufacturers use various testing procedures to ensure that their products meet the required standards. These procedures include:
- Dimensional Inspection: This involves measuring the dimensions of the ring bearing to ensure that it meets the required specifications.
- Material Analysis: This involves analyzing the material used to make the ring bearing to ensure that it is of the required quality.
- Hardness Testing: This involves measuring the hardness of the ring bearing to ensure that it can withstand the required load.
- Friction Testing: This involves testing the friction between the ring bearing and the shaft to ensure that it meets the required standards.
In conclusion, ring bearing manufacturers must adhere to various certifications and regulations, as well as use various testing procedures to ensure that their products meet the required standards.
Future Trends in Ring Bearing Manufacturing
As the demand for bearings continues to grow, manufacturers are looking for ways to improve their production processes and create more sustainable products. Here are some of the future trends in ring bearing manufacturing that you should be aware of:
Technological Advancements
The use of advanced technologies such as artificial intelligence, machine learning, and robotics is becoming increasingly common in the manufacturing industry. These technologies can help improve the accuracy and efficiency of the production process, resulting in higher quality products and lower costs.
In addition, the use of 3D printing is also becoming more widespread in the manufacturing of ring bearings. This technology allows manufacturers to create complex designs with greater precision and accuracy, resulting in stronger and more durable products.
Sustainability and Environmental Impact
As consumers become more environmentally conscious, there is a growing demand for sustainable products. Ring bearing manufacturers are responding to this demand by adopting more sustainable practices in their production processes.
For example, some manufacturers are using recycled materials in their products, reducing waste and minimizing their environmental impact. Others are implementing energy-efficient practices in their factories, such as using renewable energy sources and optimizing their production processes to reduce energy consumption.
Overall, the future of ring bearing manufacturing is focused on improving efficiency, quality, and sustainability. By adopting advanced technologies and sustainable practices, manufacturers can meet the growing demand for high-quality, environmentally friendly products.