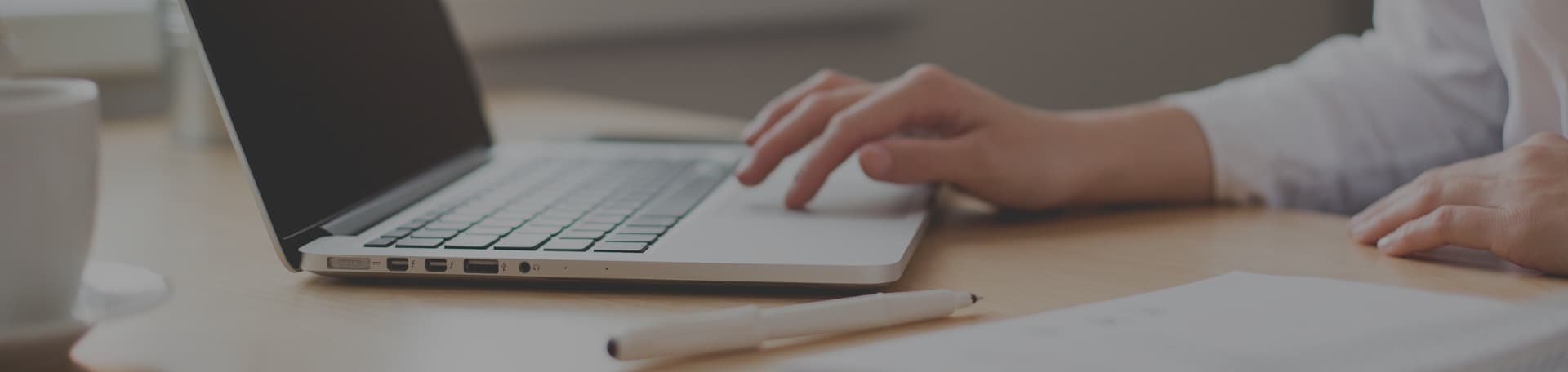
Slew Bearing Failure: Causes and Prevention
Slew Bearing Failure: Causes and Prevention
Slew bearing failure can be a significant issue for heavy machinery operators. Slew bearings are specialized bearings that are designed to handle high loads and rotational forces. They are commonly used in applications such as cranes, excavators, and wind turbines. When a slew bearing fails, it can cause significant damage to the machinery and potentially lead to downtime and lost productivity.
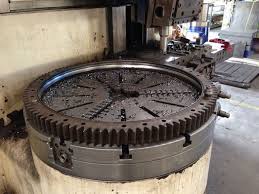
There are several common causes of slew bearing failure. One of the most common causes is inadequate lubrication. Slew bearings require proper lubrication to function correctly, and if they are not adequately lubricated, it can lead to premature wear and failure. Other common causes of slew bearing failure include corrosion, contamination, and improper installation. It is essential to understand the potential causes of slew bearing failure to prevent issues from occurring and ensure that machinery operates safely and efficiently.
Fundamentals of Slew Bearing Design
Slew bearings, also known as slewing rings, are essential components in many industrial applications. They are designed to support radial, axial, and moment loads simultaneously, making them ideal for applications that require high load capacity and rigidity. Slew bearings have a unique design that allows them to rotate continuously in a full circle or a partial arc.
The design of a slew bearing is critical to its performance and longevity. Slew bearings are designed to withstand high loads, but they also need to be lightweight and compact to fit into tight spaces. Therefore, manufacturers use advanced materials and manufacturing techniques to produce high-quality bearings that meet the demands of modern applications.
Slew bearings come in various designs, including four-point contact, cross roller, and three-row roller. Each design has its advantages and disadvantages, and the choice of design depends on the specific application requirements. For example, four-point contact bearings are suitable for applications that require high moment capacity and rigidity, while cross roller bearings are ideal for applications that require high axial and radial capacity.
In addition to the design, the selection of the right lubrication and sealing system is critical to the performance and longevity of a slew bearing. Lubrication prevents metal-to-metal contact between the rolling elements and the raceway, reducing wear and extending the life of the bearing. Sealing systems protect the bearing from contaminants and prevent lubricant leakage.
Overall, the design of a slew bearing is a complex process that requires expertise and knowledge in materials science, mechanical engineering, and manufacturing. By selecting the right design, lubrication, and sealing system, you can ensure the longevity and reliability of your slew bearing.
Common Causes of Slew Bearing Failure
Slew bearings are an essential component of many types of machinery, including cranes, excavators, wind turbines, and more. They are designed to handle heavy loads and provide smooth rotation. However, like any other mechanical component, slew bearings can fail due to a variety of reasons.
Here are some of the most common causes of slew bearing failure:
Material Defects
One of the primary reasons for slew bearing failure is material defects. If the bearing is made of poor quality material or has a defect in its structure, it can fail prematurely. The most common material defects include inclusions, voids, and cracks. These defects can cause stress concentrations, leading to premature fatigue failure of the bearing.
Manufacturing Errors
Manufacturing errors can also cause slew bearing failure. If the bearing is not manufactured to the correct specifications or is not properly heat-treated, it can lead to premature failure. For example, if the bearing is not hardened enough, it can wear out quickly or become damaged due to the heavy loads it is subjected to.
Improper Mounting Practices
Improper mounting practices can also contribute to slew bearing failure. If the bearing is not installed correctly or is not aligned properly, it can cause excessive stress on the bearing. This can cause the bearing to wear out quickly or even seize up, leading to catastrophic failure.
Lack of Maintenance
Finally, lack of maintenance is another common cause of slew bearing failure. If the bearing is not lubricated regularly or is not inspected for signs of wear and tear, it can fail prematurely. Regular maintenance, including cleaning, lubrication, and inspection, can help extend the life of the bearing and prevent premature failure.
In summary, slew bearing failure can be caused by a variety of factors, including material defects, manufacturing errors, improper mounting practices, and lack of maintenance. By understanding these common causes of failure, you can take steps to prevent premature failure and ensure the longevity of your machinery.
Symptoms and Detection of Slew Bearing Failure
Detecting slew bearing failure is essential to prevent catastrophic equipment failure and costly downtime. There are several ways to identify the symptoms of a failing slew bearing. In this section, we will discuss the visual inspection signs, audible indicators, and performance irregularities that can help detect slew bearing failure.
Visual Inspection Signs
Visual inspection is the easiest way to detect slew bearing failure. Look for the following signs:
- Discoloration or burn marks on the bearing raceways or balls
- Pitting or spalling on the bearing surfaces
- Cracks or fractures on the bearing components
- Wear or corrosion on the bearing surfaces
- Abnormal looseness or tightness in the bearing
Audible Indicators
Abnormal sounds can also indicate slew bearing failure. Listen for the following audible indicators:
- Grinding or scraping noises coming from the bearing
- Clicking or popping sounds when the bearing rotates
- Whining or humming sounds when the bearing is under load
Performance Irregularities
Performance irregularities can also indicate slew bearing failure. Look for the following performance irregularities:
- Vibration or shaking in the equipment
- Reduced or uneven speed of rotation
- Difficulty in turning or moving the equipment
- Increased energy consumption or power usage
If you notice any of these symptoms, it is essential to take immediate action to prevent further damage. Regular inspection and maintenance can help prevent slew bearing failure and ensure the longevity of your equipment.
Impact of Slew Bearing Failure
When a slew bearing fails, it can have serious consequences for your operations, safety, and finances. Understanding the impact of slew bearing failure is crucial to preventing and mitigating these risks.
Operational Downtime
Slew bearings play a critical role in many types of equipment, including cranes, excavators, and wind turbines. When a slew bearing fails, it can cause significant operational downtime. Your equipment may be out of commission for days or even weeks while repairs are made. This can result in lost productivity, missed deadlines, and dissatisfied customers.
Safety Hazards
Slew bearing failure can also pose serious safety hazards. If a bearing fails while equipment is in use, it can cause the equipment to malfunction or even collapse, potentially injuring or killing workers. In addition, if equipment is not properly maintained and inspected, it can increase the risk of bearing failure and other safety hazards.
Financial Consequences
The financial consequences of slew bearing failure can be significant. In addition to the costs associated with repairs and replacement parts, there may be additional costs associated with operational downtime, lost productivity, and missed deadlines. In some cases, equipment may need to be replaced entirely, which can be a major expense.
To minimize the impact of slew bearing failure, it is important to ensure proper maintenance and inspection of equipment, including regular lubrication and monitoring of bearing wear. If you suspect a bearing may be failing, it is important to take action immediately to prevent further damage. By taking proactive steps to prevent and mitigate slew bearing failure, you can help ensure the safety of your workers, protect your equipment, and minimize the financial impact of downtime and repairs.
Preventative Measures and Maintenance
Slew bearing failure can be costly and time-consuming to fix. However, by taking preventative measures and performing regular maintenance, you can extend the life of your bearings and prevent failure. Here are some important steps you can take to maintain your slew bearings.
Regular Inspection Protocols
Regular inspections are critical to identifying potential issues before they become major problems. You should inspect your slew bearings regularly, including checking for signs of wear, corrosion, and damage. You should also check for proper alignment and make sure there are no loose bolts or other fasteners.
Lubrication and Cleaning Procedures
Proper lubrication is essential to the longevity of your slew bearings. You should follow the manufacturer’s recommended lubrication schedule and use the appropriate lubricant. Over-lubrication can be just as damaging as under-lubrication, so be sure to use the correct amount. Additionally, cleaning your bearings regularly can help prevent the buildup of dirt and debris, which can cause damage over time.
Load Management
Proper load management is also important to prevent slew bearing failure. Overloading your bearings can cause premature wear and damage. Be sure to follow the manufacturer’s recommended load limits and avoid sudden or excessive loads. Additionally, be sure to distribute the load evenly across the bearing to prevent localized wear.
By following these preventative measures and maintenance procedures, you can help extend the life of your slew bearings and prevent costly failures. Regular inspections, proper lubrication and cleaning, and careful load management are all critical to maintaining the health of your bearings.