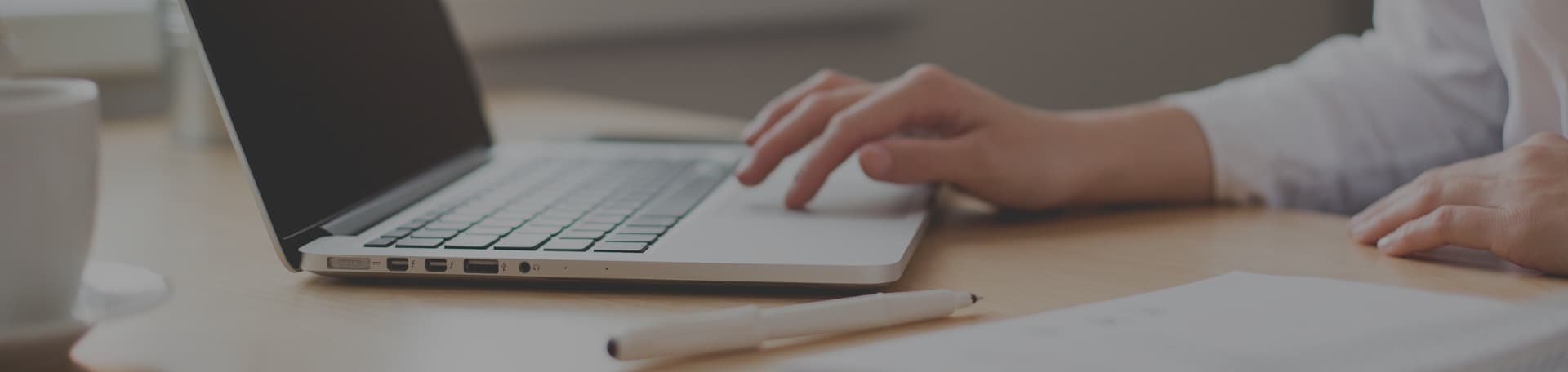
Slewing Bearing: A Comprehensive Guide
Slewing Bearing: A Comprehensive Guide
Slewing bearings are essential components in various industries that require high load carrying capacity, low friction, and stiffness. These bearings are designed to support slow-turning or slowly-oscillating heavy loads in combination, often in horizontal platforms such as cranes, wind turbines, and tunnel boring machines.

Slewing bearings are rotational rolling-element bearings that can accommodate loads in any direction and withstand extreme tilting loads. They are compact, economical, and have integral synthetic rubber seals to protect them from foreign matter and grease loss. SKF is a leading manufacturer of standard and customized slewing bearings for various industries and applications.
If you are in the market for slewing bearings, it is essential to choose a reputable manufacturer that can provide high-quality components for your project. Emerson Bearing is a trusted supplier of slewing ring bearings that support heavy loads and power transmission in all directions. They offer a wide range of slewing ring bearings for various applications and provide expert advice to help you choose the right bearing for your needs.
Fundamentals of Slewing Bearings

Slewing bearings are essential components in heavy-duty machinery and equipment. They are designed to support heavy radial, axial, and moment loads while enabling smooth and stable movement. In this section, we will discuss the design principles and core components of slewing bearings.
Design Principles
Slewing bearings are designed with a raceway and rolling elements that allow for rotation and support of heavy loads. The raceway is the path over which the rolling elements move, and it is usually made of hardened steel. The rolling elements can be balls, rollers, or cylinders, depending on the application.
The design of the slewing bearing is critical to its performance. It must be able to withstand high loads, resist wear, and operate smoothly under various conditions. The design should also consider factors such as lubrication, sealing, and mounting.
Core Components
The core components of a slewing bearing include the raceway, rolling elements, cage, seals, and mounting holes. The raceway is the most critical component, and it is usually made of two rings – an inner and an outer ring. The rolling elements are placed between the two rings and move along the raceway.
The cage is used to keep the rolling elements separated and evenly spaced. It also helps to reduce friction and wear. The seals are used to prevent contamination and retain lubrication. The mounting holes are used to secure the slewing bearing to the machine or equipment.
In summary, slewing bearings are essential components in heavy-duty machinery and equipment. They are designed to support heavy loads while enabling smooth and stable movement. The design principles and core components of slewing bearings must be carefully considered to ensure optimal performance and longevity.
Applications of Slewing Bearings

Slewing bearings are widely used in various industries due to their ability to support controlled rotation and manage heavy loads. Here are some notable applications of slewing bearings:
Industrial Machinery
Slewing bearings are commonly used in industrial machinery such as excavators, cranes, and aerial work platforms. These machines require precise and smooth rotation, and slewing bearings provide the necessary support and stability for such movements. Slewing bearings are also used in tunnel boring machines, where they support the cutter head and allow for the excavation of tunnels.
Wind Turbines
Slewing bearings play a critical role in wind turbines, where they support the rotor and allow it to rotate. The size and weight of wind turbine rotors require large and robust slewing bearings, which must withstand extreme loads and weather conditions. Slewing bearings also enable the yaw system of wind turbines, which allows the rotor to face the wind direction.
Medical Equipment
Slewing bearings are used in medical equipment such as CT scanners and MRI machines. These machines require precise and accurate rotation, and slewing bearings provide the necessary support and stability for such movements. Slewing bearings also play a critical role in robotic surgery systems, where they support the arms and allow for precise and controlled movements.
Overall, slewing bearings are essential components in various industries, providing support and stability for controlled rotation and heavy loads.
Manufacturing Processes
Slewing bearings are critical components in various types of machinery that require smooth and precise rotation. The manufacturing process of slewing bearings involves several key steps, including forging and machining, heat treatment, and quality control.
Forging and Machining
The first step in manufacturing a slewing bearing is to forge the raw material into the desired shape. The forging process involves heating the metal to a high temperature and then shaping it using a forging press. This process creates a dense and uniform structure in the metal, which makes it stronger and more resistant to wear and tear. After forging, the metal is machined to the exact specifications required for the slewing bearing.
Heat Treatment
Heat treatment is a critical step in the manufacturing process of slewing bearings. The heat treatment process involves heating the metal to a specific temperature and then cooling it down rapidly to create a specific microstructure in the metal. This process improves the strength, durability, and wear resistance of the metal.
Quality Control
Quality control is an essential part of the manufacturing process of slewing bearings. The quality control process involves checking the dimensions, surface finish, and material properties of the finished product. This process ensures that the slewing bearings meet the required specifications and are free from defects.
In summary, the manufacturing process of slewing bearings involves forging and machining, heat treatment, and quality control. Each step of the process is critical in ensuring that the finished product is strong, durable, and meets the required specifications.
Installation and Maintenance
When it comes to slewing bearings, proper installation and maintenance are crucial for optimal performance and longevity. In this section, we will cover the key procedures and guidelines to follow for installing and maintaining your slewing bearing.
Installation Procedures
Before installing your slewing bearing, it is important to ensure that it is in good condition and free from any physical damage. You should also make sure that the mounting surfaces are flat and machined properly.
When installing the slewing bearing, it should be mounted in an unloaded condition. Eye bolts should be used to lift the bearing, and they should be fully threaded into the bolt hole with a minimum thread engagement of 1.5 times the bolt diameter. The mounting bolts should also be torqued to the manufacturer’s specifications.
Maintenance Guidelines
Proper maintenance is essential for keeping your slewing bearing in good condition and preventing premature failure. One important aspect of maintenance is lubrication. The slewing bearing raceway, screw worm, and bearings should be lubricated regularly according to the manufacturer’s recommendations.
It is also important to inspect the slewing bearing regularly for any signs of wear or damage. This can include checking for any cracks or corrosion on the bearing surface, as well as any abnormal noise or vibration during operation.
Troubleshooting
If you encounter any issues with your slewing bearing, there are several troubleshooting steps you can take. One common issue is noise or vibration during operation, which can be caused by a variety of factors such as improper lubrication, misalignment, or damaged bearings.
If you suspect that your slewing bearing is damaged or worn, it is important to address the issue promptly to avoid further damage or failure. This may involve replacing the bearing or making adjustments to the installation or maintenance procedures.
By following these installation and maintenance guidelines, you can help ensure that your slewing bearing performs optimally and lasts for years to come.
Market Trends and Future Outlook
Slewing bearings are an essential component in various industrial applications, including construction, mining, aerospace, and wind turbines. The global slewing bearing market size is expected to reach US$ 5,831.2 million by 2028, growing at a CAGR of 5.4% from 2021 to 2028 The Insight Partners. The market is projected to witness a CAGR of 6.78% during the forecast period to reach a total market size of US$8.349 billion by 2026 Knowledge Sourcing.
One of the major trends in the slewing bearing market is the increasing demand for customized solutions. As customers demand more personalized products, manufacturers are offering customized solutions to meet their requirements. Additionally, the growing demand for renewable energy sources such as wind turbines is driving the market growth. Slewing bearings are used in wind turbines to support the rotor and ensure smooth rotation, and the increasing demand for wind energy is fueling the demand for slewing bearings.
The Asia-Pacific region dominates the slewing bearing market, accounting for the largest share of the market Data Bridge Market Research. The market in China is growing rapidly due to the numerous solar investments made by the government, as well as the growing medical sector. However, the high cost and lack of appropriate resources are expected to restrain the growth of the market.
In conclusion, the slewing bearing market is expected to grow steadily in the coming years, driven by the increasing demand for customized solutions and the growing demand for renewable energy sources. The Asia-Pacific region is expected to dominate the market, with China leading the growth in the region.