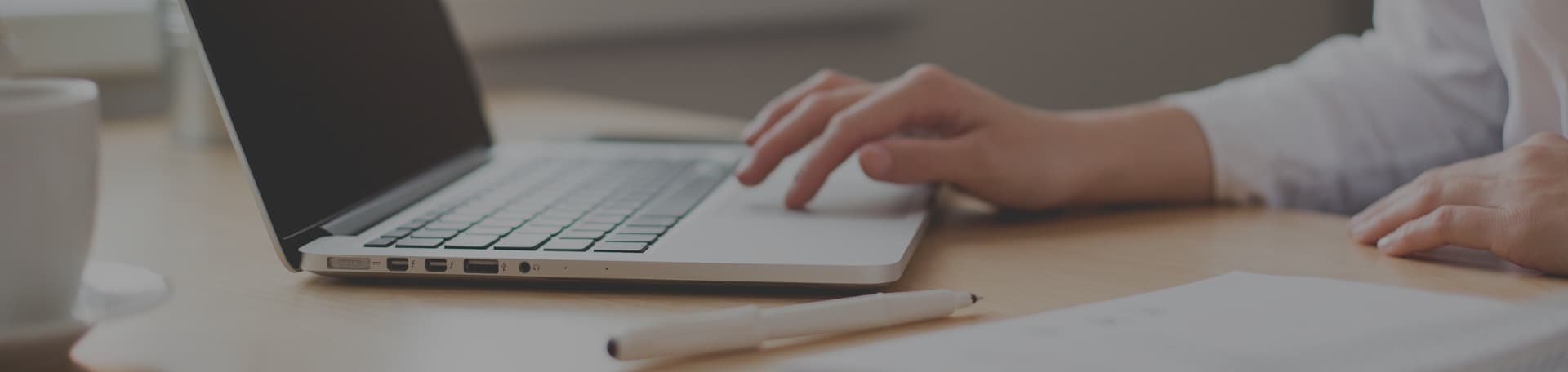
Slewing Bearing Calculation: A Comprehensive Guide
Slewing Bearing Calculation: A Comprehensive Guide
Calculating the performance of slewing bearings is a critical aspect of their design and operation. Slewing bearings are utilized in various applications, including cranes, excavators, wind turbines, and other heavy machinery. These bearings are designed to handle high axial, radial, and moment loads, making them ideal for applications that require smooth rotation under heavy loads.

The calculation of slewing bearings involves determining critical parameters, such as load capacity, friction torque, and bearing life. The load capacity of a slewing bearing is determined by the size and number of rolling elements, as well as the material properties of the bearing and the applied loads. Friction torque is a measure of the resistance experienced by the bearing when rotating, and it is influenced by factors such as bearing design, lubrication, and operating conditions. Bearing life is a measure of the expected lifespan of the bearing, and it is determined by factors such as load, speed, and operating temperature.
Overall, the calculation of slewing bearings is a complex process that requires a deep understanding of bearing design, material science, and mechanical engineering principles. Accurate calculations are essential for ensuring the optimal performance and longevity of these critical components. In the following sections, we will explore the key factors involved in slewing bearing calculation, including load capacity, friction torque, and bearing life, and provide insights into best practices for ensuring accurate and reliable calculations.
Fundamentals of Slewing Bearings

Slewing bearings are large bearings that can handle axial, radial, and moment loads simultaneously. They are used in a variety of applications, such as cranes, excavators, wind turbines, and medical equipment. In this section, we will discuss the design principles and load types and distribution of slewing bearings.
Design Principles
Slewing bearings are designed with various parameters in mind, such as the diameter, height, number of rolling elements, and contact angle. The diameter of the bearing determines the load capacity and stiffness. The height of the bearing affects the moment capacity and the contact angle influences the frictional torque. The number of rolling elements impacts the load distribution and fatigue life. The design of the raceway and rolling elements must also consider the types of loads and operating conditions.
Load Types and Distribution
Slewing bearings are subjected to various types of loads, such as axial, radial, and moment loads. The axial load is perpendicular to the axis of rotation and is caused by the weight of the equipment or external forces. The radial load is parallel to the axis of rotation and is caused by wind or centrifugal forces. The moment load is a combination of axial and radial loads and is caused by the weight of the equipment and its movement.
The load distribution in slewing bearings is non-uniform due to the curvature of the raceway and the number of rolling elements. The load capacity of the bearing is affected by the load distribution and the contact stresses between the rolling elements and raceway. The load distribution can be improved by optimizing the number and size of rolling elements, the contact angle, and the raceway profile.
In summary, slewing bearings are complex bearings that require careful consideration of the design principles and load types and distribution. The proper selection and calculation of slewing bearings are crucial for the safe and efficient operation of equipment.
Calculation Methodology

When it comes to calculating the carrying capacity of a slewing bearing, there are several factors that need to be taken into consideration. In this section, we will discuss the methodology used to calculate the static and dynamic load capacities of slewing bearings, as well as the estimation of service life.
Static Load Capacity
The static load capacity of a slewing bearing refers to the maximum load that it can support without experiencing permanent deformation or failure. To calculate the static load capacity, you need to consider the bearing’s geometry, material properties, and the loads acting on it. The most common method used to calculate the static load capacity of a slewing bearing is the Finite Element Method (FEM). FEM involves creating a 3D model of the bearing and analyzing its response to different loads.
Dynamic Load Capacity
The dynamic load capacity of a slewing bearing refers to the maximum load that it can support while rotating at a constant speed without experiencing fatigue failure. To calculate the dynamic load capacity, you need to consider the bearing’s geometry, material properties, and the loads acting on it. The most common method used to calculate the dynamic load capacity of a slewing bearing is the ISO 281 standard. The ISO 281 standard provides a formula for calculating the basic dynamic load rating of a bearing based on its size, geometry, and material properties.
Service Life Estimation
The service life of a slewing bearing refers to the amount of time it can operate without experiencing failure or significant wear. To estimate the service life of a slewing bearing, you need to consider the bearing’s load, speed, lubrication, and operating conditions. The most common method used to estimate the service life of a slewing bearing is the ISO 281 standard. The ISO 281 standard provides a formula for calculating the basic rating life of a bearing based on its size, geometry, and material properties. The basic rating life is an estimate of the number of revolutions that a bearing can withstand before fatigue failure occurs.
Bearing Selection Criteria
When selecting a slewing bearing, there are several criteria to consider. These include material considerations and geometric parameters.
Material Considerations
The material used for the bearing can greatly affect its performance and durability. Common materials for slewing bearings include chrome steel, stainless steel, and plastic. Chrome steel is the most commonly used material due to its high strength and durability. Stainless steel is often used in applications where corrosion resistance is important. Plastic bearings are lightweight and have low friction, but are not as durable as metal bearings.
Geometric Parameters
The geometric parameters of a slewing bearing include its inner and outer diameter, height, and weight. These parameters are important to consider when selecting a bearing that can handle the load and fit within the available space. The load carrying capacity of a bearing is determined by its diameter and the number and size of its rolling elements. The height of the bearing affects its stability and rigidity. The weight of the bearing is important to consider when designing the supporting structure.
When selecting a slewing bearing, it is important to consider both material considerations and geometric parameters to ensure optimal performance and durability.
Mounting and Installation Considerations
When it comes to mounting and installation of slewing bearings, there are a few important considerations that must be taken into account to ensure optimal performance and longevity.
Bolt Connection Calculations
The first consideration is the bolt connection calculations. It is crucial to ensure that the bolts used to connect the bearing to the surrounding structure are strong enough to handle the loads and stresses that will be placed upon them. This requires careful calculation of the bolt size, material, and torque values, taking into account factors such as the bearing’s load capacity, operating speed, and temperature range.
Structural Support Requirements
Another important consideration is the structural support requirements. Slewing bearings are designed to be mounted onto a sturdy support structure that can withstand the loads and stresses generated during operation. It is important to ensure that the support structure is designed and constructed to meet the specific requirements of the bearing, taking into account factors such as the bearing’s weight, size, and operating conditions.
To ensure proper installation, it is recommended to follow the manufacturer’s installation instructions carefully and to use the recommended tools and equipment. It is also important to perform regular maintenance and inspections to ensure that the bearing and its surrounding structure are in good condition and functioning properly. By taking these factors into account, you can ensure optimal performance and longevity of your slewing bearing.
Maintenance and Inspection
Slewing bearings are critical components in many applications, and proper maintenance and inspection are essential to ensure their reliable operation. Here are some key considerations for maintaining and inspecting your slewing bearings.
Lubrication Requirements
Proper lubrication is critical for the long-term performance of slewing bearings. Without adequate lubrication, the bearings can experience excessive wear, corrosion, and ultimately failure. Therefore, it is important to follow the manufacturer’s recommendations for lubrication type, quantity, and frequency.
Slewing bearings typically require periodic lubrication, and the frequency of lubrication depends on factors such as the bearing size, operating conditions, and application requirements. Some bearings may require daily lubrication, while others may only need lubrication every few months or years.
Wear and Failure Detection
Regular inspection of slewing bearings can help detect wear and potential failure before they become serious problems. Some common indicators of wear and failure include:
- Abnormal noise or vibration
- Excessive play or movement
- Abnormal temperature rise
- Lubrication leaks or contamination
- Visual signs of wear, such as scoring or pitting
To detect wear and failure, it is important to follow the manufacturer’s recommendations for inspection frequency and methods. Some common inspection methods include visual inspection, measurement of bearing play or clearance, and monitoring of temperature and vibration.
In conclusion, proper maintenance and inspection of slewing bearings is essential for their reliable operation. By following the manufacturer’s recommendations for lubrication and inspection, you can help ensure the long-term performance of your bearings and avoid costly downtime and repairs.