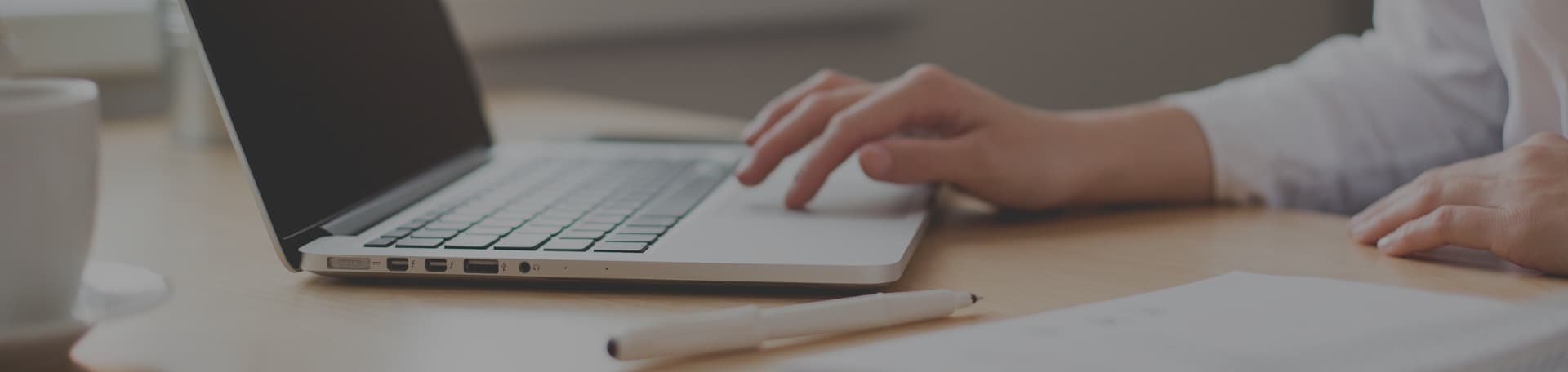
Slewing Bearing Ring: Understanding Its Function and Applications
Slewing Bearing Ring: Understanding Its Function and Applications
If you work with heavy machinery, you have probably heard of slewing bearing rings. These bearings are essential components in many types of equipment, from cranes and excavators to wind turbines and medical scanners. In simple terms, a slewing bearing ring is a large bearing that supports axial and radial loads while also enabling rotation.

Slewing bearing rings come in many different sizes and designs, depending on the specific application. Some are designed to handle high loads, while others are optimized for speed or precision. Some have internal or external gears for driving the rotation, while others are gearless. The most common types of slewing bearing rings are ball and roller bearings, which use balls or rollers to reduce friction and support the load.
Slewing bearing rings are critical components in many industries, and they must be designed and manufactured to the highest standards to ensure safety and reliability. In this article, we will explore the different types of slewing bearing rings, their applications, and how they work. We will also discuss the factors that affect their performance, such as load capacity, speed, and accuracy. Whether you are an engineer, a technician, or a machine operator, understanding slewing bearing rings is essential for maintaining and optimizing your equipment.
Design and Engineering

Slewing bearings are essential components in many applications, including cranes, excavators, wind turbines, and radar systems. They allow for smooth rotation and movement of heavy loads, making them critical for the efficient operation of machinery. In this section, we will discuss the design and engineering of slewing bearings.
Types of Slewing Bearings
There are several types of slewing bearings available, including four-point contact bearings, double-row ball bearings, and cross roller bearings. Four-point contact bearings are the most commonly used type of slewing bearing due to their versatility and cost-effectiveness. Double-row ball bearings are ideal for applications requiring high axial and radial loads, while cross roller bearings are best suited for applications requiring high precision and rigidity.
Material Specifications
The material used in the construction of slewing bearings is critical to their performance and longevity. Slewing bearings are typically made from high-quality steel, which is hardened and tempered to withstand the stresses of heavy loads and high speeds. The raceways of the bearings are usually induction hardened to improve wear resistance and reduce friction. Other materials, such as aluminum and plastics, may also be used in the construction of slewing bearings for specific applications.
Structural Features
Slewing bearings have several structural features that contribute to their performance. The most important of these features is the raceway, which is a groove or channel in which the balls or rollers of the bearing roll. The raceway must be precisely machined and hardened to ensure smooth rotation and reduce wear. Other structural features include the cage, which holds the balls or rollers in place, and the seals, which prevent contamination and retain lubrication.
In conclusion, the design and engineering of slewing bearings are critical to their performance and longevity. The type of bearing, material specifications, and structural features all play a significant role in determining the suitability of a slewing bearing for a particular application. By understanding these factors, you can select the right slewing bearing for your machinery and ensure its efficient operation.
Manufacturing Process
Slewing bearing rings are complex components that require a precise manufacturing process to ensure their functionality and durability. The manufacturing process of slewing bearing rings involves several key steps, including forging and machining, heat treatment, and quality control.
Forging and Machining
The first step in the manufacturing process of slewing bearing rings is forging and machining. The raw material used for slewing bearing rings is typically high-strength steel, which is forged into the desired shape using a hydraulic press. After forging, the rough shape of the slewing bearing ring is machined to the required dimensions using CNC machines. This step is critical to ensure the accuracy and precision of the slewing bearing ring.
Heat Treatment
Heat treatment is another crucial step in the manufacturing process of slewing bearing rings. The heat treatment process involves heating the slewing bearing ring to a specific temperature and then cooling it down slowly to achieve the desired mechanical properties. This process helps to increase the strength and hardness of the slewing bearing ring, making it more durable and resistant to wear and tear.
Quality Control
Quality control is an essential part of the manufacturing process of slewing bearing rings. Each step of the manufacturing process is carefully monitored to ensure that the slewing bearing ring meets the required specifications and standards. The finished slewing bearing ring is subjected to rigorous testing and inspection to ensure that it is free from defects and meets the required quality standards.
In summary, the manufacturing process of slewing bearing rings is a complex and precise process that requires careful attention to detail and quality control. The process involves several key steps, including forging and machining, heat treatment, and quality control, which are critical to ensuring the functionality and durability of the finished product.
Applications
Slewing ring bearings are used in a variety of industries and applications. In this section, we will discuss some of the most common applications of slewing ring bearings.
Construction Machinery
Slewing ring bearings are commonly used in construction machinery, such as cranes, excavators, and backhoes. These machines require bearings that can support heavy loads and withstand harsh operating conditions. Slewing ring bearings provide the necessary load capacity and durability for these applications.
Wind Turbines
Slewing ring bearings are also used in wind turbines to support the rotor and allow it to rotate. The bearings must be able to handle large loads and operate in harsh environments, including extreme temperatures and high winds. Slewing ring bearings are ideal for these applications due to their high load capacity and durability.
Medical Equipment
Slewing ring bearings are used in medical equipment, such as CT scanners and MRI machines. These machines require bearings that can support heavy loads and operate with high precision. Slewing ring bearings provide the necessary load capacity and precision for these applications.
In summary, slewing ring bearings are used in a variety of industries and applications, including construction machinery, wind turbines, and medical equipment. These bearings provide the necessary load capacity, durability, and precision for these demanding applications.
Installation and Maintenance
When installing and maintaining a slewing bearing ring, there are several guidelines that you should follow to ensure that it operates effectively and efficiently. These guidelines include installation, lubrication and sealing, and inspection and replacement.
Installation Guidelines
When installing a slewing bearing ring, it is important to ensure that the bearing mounting surfaces are machined flat after all welding and stress relief treatment on the structures is complete. If subsequent welding is necessary, it must be performed without damaging the bearing mounting surfaces.
Before mounting the slewing bearing ring, check for physical damage, and lift the bearing with eye bolts, ensuring that the eye bolts are fully threaded into the bolt hole. Use a minimum thread engagement of 1.5 times the bolt diameter. The slew bearings shall be mounted in an unloaded condition.
Lubrication and Sealing
Lubrication and sealing are essential for the proper functioning of a slewing bearing ring. Lubrication helps to reduce friction and wear, while sealing helps to prevent contamination and corrosion.
When lubricating the slewing bearing ring, ensure that the gear tooth surface is clean. It is recommended to brush the grease on the gear with a clean brush. Use the appropriate lubricant for the operating conditions and follow the manufacturer’s recommendations for lubrication intervals.
Sealing is also important to prevent contamination and corrosion. Ensure that the sealing system is installed correctly and that the seals are in good condition. Replace any damaged or worn seals immediately.
Inspection and Replacement
Regular inspection and maintenance are essential to ensure the long-term performance of a slewing bearing ring. Inspect the bearing regularly for signs of wear, damage, or corrosion. Check the bolt preload torque for the first time using 100 working hours.
If any signs of wear, damage, or corrosion are detected, replace the bearing immediately. Use only genuine replacement parts and follow the manufacturer’s recommendations for replacement intervals.
By following these guidelines for installation, lubrication and sealing, and inspection and replacement, you can ensure the long-term performance and reliability of your slewing bearing ring.
Market Analysis
Industry Demand
Slewing ring bearings are large-sized bearings that are used in a wide range of applications such as cranes, excavators, wind turbines, and medical equipment. According to a report by Maximize Market Research, the global slewing ring bearings market is expected to reach nearly US$ 8.64 Bn by 2029 with a CAGR of 6.12% during the forecast period. The report suggests that the growing demand for renewable energy and the expansion of the infrastructure sector are driving the market expansion for slewing ring bearings.
Another report by Transparency Market Research states that the global market for slewing ring bearings was valued at US$ 4.4 Bn in 2021 and is estimated to grow at a CAGR of 4.4% from 2022 to 2031, reaching US$ 6.7 Bn by the end of 2031. The report highlights that the rise in adoption of renewable energy and expansion in the infrastructure sector are driving the market expansion for slewing ring bearings.
Future Trends
The Allied Market Research report suggests that the market for slewing bearings in China has been increasing rapidly due to the numerous solar investments made by the government as well as the growing medical sector. The report highlights that higher cost and lack of inappropriate resources restrain the growth of the market.
The Insight Partners report states that the slewing bearing market is expected to grow from US$ 4,025.1 million in 2021 to US$ 5,831.2 million by 2028, estimated to grow at a CAGR of 5.4% from 2021 to 2028. The report emphasizes that owing to the increasing concerns about national security, governments across the world are allocating greater funds to strengthen their defense forces.
In conclusion, the slewing ring bearings market is expected to grow significantly in the coming years due to the increasing demand for renewable energy and expansion in the infrastructure sector. The market is also expected to grow in China due to the numerous solar investments made by the government and the growing medical sector.