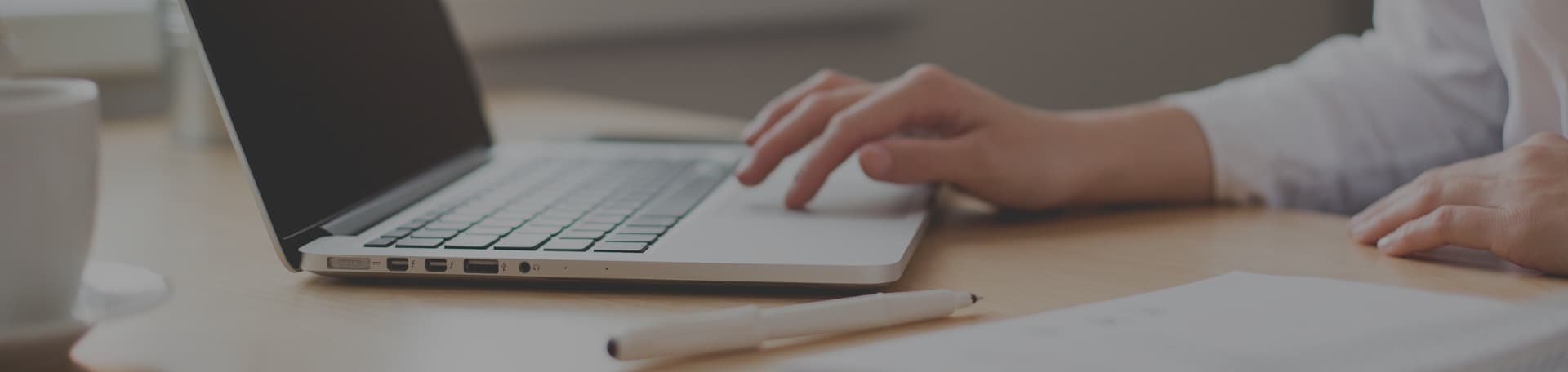
Slewing Bearing Working: Understanding the Basics
Slewing Bearing Working: Understanding the Basics
If you are interested in the mechanics of heavy machinery, you may have come across the term “slewing bearing.” A slewing bearing is a type of rolling-element bearing that supports slow-turning or slowly-oscillating loads in combination. It is commonly used in heavy machinery such as cranes, excavators, and wind turbines.

Slewing bearings are designed to support a combination of axial, radial, and moment loads. They are typically used in applications where the bearing must support an upper structure and facilitate its rotation. Slewing bearings are also used in applications where smooth and stable movement of heavy equipment is required. They are designed to be durable and long-lasting, even in harsh environments.
If you are curious about how slewing bearings work, you may be interested to know that they consist of two rings – an inner ring and an outer ring – that are connected by rolling elements. The rolling elements are usually balls or cylindrical rollers, and they are held in place by a cage. When a load is applied to the bearing, the rolling elements roll along the raceway, allowing the inner and outer rings to rotate relative to each other.
Basics of Slewing Bearings

Slewing bearings are large-sized bearings that can handle axial, radial, and moment loads. They enable rotational movement between two components while supporting heavy loads and providing stability. In this section, we will discuss the design principles and core components of slewing bearings.
Design Principles
Slewing bearings are designed to have a compact structure, high rigidity, and good load-carrying capacity. They consist of an inner and outer ring, with rolling elements (such as balls or rollers) in between. The outer ring is mounted to the machine’s structure, while the inner ring is attached to the rotating component. The bearing has a set of gears on its outer ring that mesh with a smaller set of gears on the inner ring, enabling the rotational motion of the component.
Slewing bearings are crucial for machines that require a large range of motion, such as cranes, excavators, and wind turbines. They allow smooth and stable movement of heavy construction equipment and support the rotation of wind turbine blades, allowing them to face the wind for maximum energy generation.
Core Components
The core components of a slewing bearing are the inner ring, outer ring, rolling elements, and gears. The inner and outer rings are made of high-strength steel and are designed to withstand heavy loads. The rolling elements are usually balls or rollers, which reduce friction and allow for smooth movement. The gears are designed to mesh with each other and transmit torque from the outer ring to the inner ring.
Slewing bearings come in different designs, such as single-row, double-row, and three-row designs. The choice of design depends on the specific application and the loads that the bearing will be subjected to.
In summary, slewing bearings are essential components in many machines that require a large range of motion. They are designed to have a compact structure, high rigidity, and good load-carrying capacity. The core components of a slewing bearing are the inner and outer rings, rolling elements, and gears.
Operational Mechanics
Slewing bearings are designed to handle a range of loads and provide rotational movement. Understanding the operational mechanics of slewing bearings is crucial to ensure their proper functioning. In this section, we’ll explore the load handling and rotational movement of slewing bearings.
Load Handling
Slewing bearings are designed to handle a range of loads, including axial, radial, and moment loads. Axial loads are parallel to the axis of rotation, while radial loads are perpendicular to the axis of rotation. Moment loads are a combination of axial and radial loads.
The load handling capacity of a slewing bearing depends on its design, size, and materials used. Slewing bearings are typically made of high-strength steel and are designed to withstand heavy loads. The load capacity of a slewing bearing can be determined by calculating the maximum axial and radial loads it can handle.
Rotational Movement
Slewing bearings provide rotational movement between two objects. The outer ring of the slewing bearing is fixed to a motionless surface, while the inner ring is fixed to a turning object. The balls, caging, and raceways of the slewing bearing allow for smooth and precise rotation.
The rotational movement of a slewing bearing depends on its design and lubrication. Slewing bearings can be designed for single or double-row ball or roller configurations. The type of lubrication used can also affect the rotational movement of the slewing bearing. Proper lubrication is essential to ensure smooth and efficient rotation.
In summary, slewing bearings are designed to handle a range of loads and provide rotational movement. The load handling capacity of a slewing bearing depends on its design, size, and materials used. The rotational movement of a slewing bearing depends on its design and lubrication. Proper maintenance and lubrication are crucial to ensure the proper functioning of slewing bearings.
Installation and Maintenance
When it comes to working with slewing bearings, proper installation and maintenance are crucial for optimal performance and longevity. In this section, we will cover the necessary steps for mounting and caring for your slewing bearing.
Mounting Procedures
Before mounting the slewing bearing, it is important to check for any physical damage. Once you have ensured that the bearing is in good condition, lift it with eye bolts and make sure they are fully threaded into the bolt hole. Use a minimum thread engagement of 1.5 times the bolt diameter. The slew bearings should be mounted in an unloaded condition. Refer to the Slew Bearing Installation and Maintenance Manual for more detailed instructions.
Lubrication and Care
Proper lubrication is a critical aspect of maintaining your slewing bearing. Ensure that the slewing ring raceway, screw worm, and bearings are properly lubricated. Refer to the manufacturer’s instructions for specific lubrication requirements. For example, some slewing bearings may require periodic greasing, while others may require oil lubrication.
In addition to lubrication, it is important to regularly inspect your slewing bearing for any signs of wear or damage. This can include checking for cracks, corrosion, or any abnormalities in the bearing’s movement. Address any issues as soon as possible to prevent further damage.
Taking the time to properly install and maintain your slewing bearing can help ensure its longevity and optimal performance. By following the recommended mounting procedures and lubrication guidelines, you can help prevent premature wear and damage to your bearing.
Common Applications
Slewing bearings are used in a wide range of applications, from industrial machinery to renewable energy systems. Here are some of the most common applications of slewing bearings:
Industrial Machinery
Slewing bearings are commonly used in industrial machinery such as cranes, excavators, and material handling equipment. In these applications, slewing bearings are used to support and facilitate the rotation of the upper structure of the equipment. Slewing bearings are also used in conveyor systems, where they are used to support the conveyor belt and facilitate its movement.
Renewable Energy Systems
Slewing bearings are also used in renewable energy systems such as wind turbines and solar trackers. In wind turbines, slewing bearings are used to support the rotor and facilitate its rotation. In solar trackers, slewing bearings are used to support the solar panels and facilitate their movement to track the sun.
In both of these applications, slewing bearings are subjected to high loads and must be able to withstand harsh environmental conditions. As a result, slewing bearings used in renewable energy systems are typically designed to be highly durable and resistant to corrosion.
Overall, slewing bearings are an essential component in a wide range of applications, providing reliable support and controlled rotation. Whether you are designing industrial machinery or renewable energy systems, selecting the right slewing bearing is critical to ensuring the long-term performance and reliability of your equipment.
Troubleshooting and Failure Analysis
Slewing bearings are critical components in many heavy-duty applications. They are designed to withstand high loads and extreme conditions, but like any mechanical component, they can fail. When a slewing bearing fails, it can cause significant damage to the equipment and put operators at risk. Therefore, it is essential to perform regular maintenance and inspections to prevent failures and troubleshoot any issues that arise.
Common Causes of Failure
There are several common causes of slewing bearing failure, including:
- Overloading: Exceeding the maximum load capacity of the bearing can cause it to fail.
- Misalignment: If the bearing is not aligned correctly, it can cause excessive wear and tear, leading to failure.
- Improper Lubrication: If the bearing is not lubricated correctly, it can cause excessive wear and tear, leading to failure.
- Contamination: Dirt, debris, and other contaminants can cause damage to the bearing, leading to failure.
Troubleshooting
If you suspect that your slewing bearing is failing, there are several things you can do to troubleshoot the issue. Here are a few steps to follow:
- Inspect the bearing for signs of wear and damage. Look for cracks, pitting, and other signs of wear.
- Check the alignment of the bearing. If it is misaligned, it can cause excessive wear and tear, leading to failure.
- Check the lubrication of the bearing. If it is not lubricated correctly, it can cause excessive wear and tear, leading to failure.
- Check for contamination. Dirt, debris, and other contaminants can cause damage to the bearing, leading to failure.
Failure Analysis
If your slewing bearing has failed, it is essential to perform a failure analysis to determine the root cause of the failure. Here are a few steps to follow:
- Inspect the bearing for signs of wear and damage. Look for cracks, pitting, and other signs of wear.
- Analyze the operating conditions of the bearing. Look at factors such as load, speed, and temperature.
- Check the lubrication of the bearing. If it is not lubricated correctly, it can cause excessive wear and tear, leading to failure.
- Check for contamination. Dirt, debris, and other contaminants can cause damage to the bearing, leading to failure.
By performing regular maintenance and inspections, troubleshooting issues when they arise, and performing failure analysis when necessary, you can prevent slewing bearing failure and ensure the safe and reliable operation of your equipment.