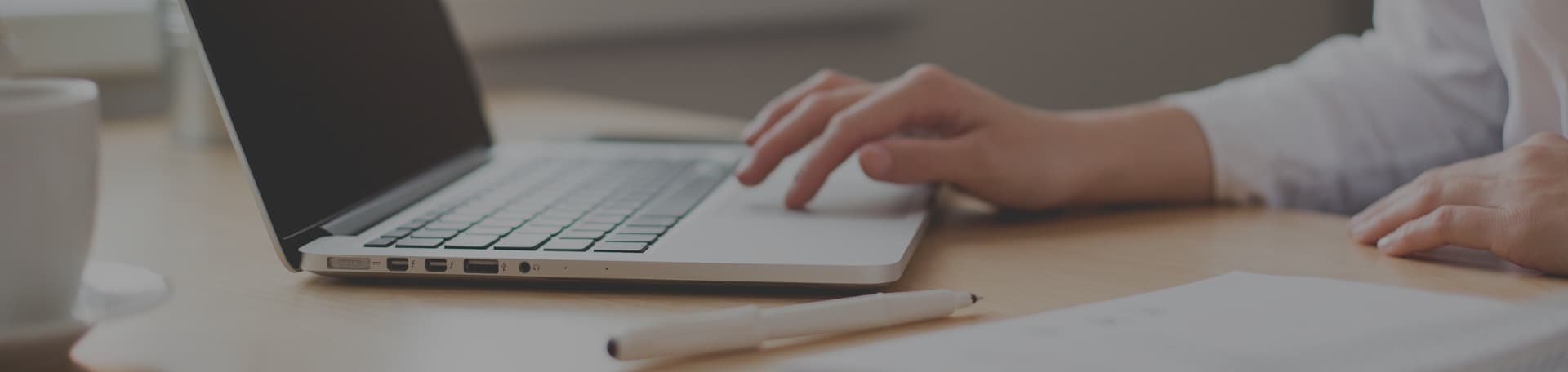
Slewing Bearings: A Comprehensive Guide to its Function and Applications
Slewing Bearings: A Comprehensive Guide to its Function and Applications
If you’re involved in the design or manufacture of large machinery, you may have heard of slewing bearings. These specialized bearings are used in a variety of applications where heavy loads need to be supported and rotated. They are commonly found in cranes, excavators, wind turbines, and other types of heavy equipment.

Slewing bearing are unique in that they can support both radial and axial loads, as well as moment loads. This makes them ideal for applications where heavy loads need to be supported and rotated, such as in a crane or excavator. They are also designed to accommodate oscillating movements, which is important when dealing with heavy loads that may shift during operation.
Overall, slewing bearings are an important component in many types of heavy machinery. They offer a unique combination of load-bearing capacity and rotational ability that makes them ideal for a variety of applications. If you’re involved in the design or manufacture of heavy equipment, it’s important to understand the role that slewing bearings play and how they can be incorporated into your designs.
Fundamentals of Slewing Bearings

Slewing bearings, also known as turntable bearings or slewing rings, are essential components in many industrial applications. They are designed to support heavy axial, radial, and moment loads while enabling smooth rotational movement between two components. In this section, we will discuss the design principles and core components of slewing bearings.
Design Principles
Slewing bearings are designed to meet specific application requirements, such as load capacity, speed, accuracy, and durability. The design principles of slewing bearings include:
- Raceway geometry: The raceway is the surface on which the rolling elements roll. It can be circular, elliptical, or any other shape that suits the application requirements.
- Rolling elements: Slewing bearings can use various types of rolling elements, such as balls, rollers, or needles. The choice of rolling elements depends on the application requirements, such as load capacity, speed, and accuracy.
- Cage: The cage holds the rolling elements in place and prevents them from colliding with each other. The cage can be made of various materials, such as steel, brass, or plastic.
- Seals: Slewing bearings can be sealed to prevent contamination and retain lubricant. The seals can be made of various materials, such as rubber, metal, or plastic.
Core Components
The core components of slewing bearings include:
- Outer ring: The outer ring is the stationary component of the slewing bearing. It is usually mounted to a fixed structure, such as a crane pedestal or a wind turbine tower.
- Inner ring: The inner ring is the rotating component of the slewing bearing. It is usually mounted to a shaft or a platform, such as a crane jib or a wind turbine nacelle.
- Rolling elements: The rolling elements are the components that roll on the raceway. They transmit the load between the outer and inner rings while enabling smooth rotational movement.
- Cage: The cage holds the rolling elements in place and prevents them from colliding with each other. It also distributes the load evenly among the rolling elements.
- Seals: The seals prevent contamination and retain lubricant. They are usually located on both sides of the slewing bearing.
In summary, slewing bearing are critical components in many industrial applications. They are designed to support heavy loads while enabling smooth rotational movement. The design principles and core components of slewing bearings are essential to ensure their performance and reliability.
Types of Slewing Bearings
When it comes to selecting a slewing bearing, there are different types to choose from depending on the specific requirements of your application. In this section, we will go over the four main types of slewing bearings: Single-Row Ball Type, Double-Row Ball Type, Crossed Roller Type, and Three-Row Roller Type.
Single-Row Ball Type
Single-Row Ball Type slewing bearings consist of a single row of balls and are ideal for lighter-duty applications. They are compact, cost-effective, and easy to install. However, they have a lower load capacity compared to other types of slewing bearings. Single-Row Ball Type slewing bearings are suitable for applications that require low torque and high precision.
Double-Row Ball Type
Double-Row Ball Type slewing bearings consist of two rows of balls and have a higher load capacity than Single-Row Ball Type. They are suitable for medium-duty applications that require moderate torque and precision. Double-Row Ball Type slewing bearings are often used in applications such as excavators, cranes, and wind turbines.
Crossed Roller Type
Crossed Roller Type slewing bearings consist of two raceways with crossed cylindrical rollers. They have a higher load capacity than both Single-Row and Double-Row Ball Type slewing bearings. Crossed Roller Type slewing bearings are suitable for applications that require high precision, such as machine tools, robotics, and medical equipment.
Three-Row Roller Type
Three-Row Roller Type slewing bearings consist of three rows of rollers and have the highest load capacity of all the types of slewing bearing. They are suitable for heavy-duty applications that require high torque and precision. Three-Row Roller Type slewing bearings are often used in applications such as cranes, excavators, and wind turbines.
In summary, the choice of slewing bearing type depends on the specific demands of the application, such as load capacity, rotational speed, and environmental factors. By understanding the different types of slewing bearing, you can select the right one for your application and ensure optimal performance.
Applications of Slewing Bearing
Slewing bearing have a wide range of applications across various industries due to their ability to support controlled rotation and manage heavy loads. Here are some notable applications:
Wind Turbines
Slewing bearings are used in wind turbines to enable the nacelle to rotate and face the wind. They are crucial for the turbine’s yaw and pitch control systems. In wind turbines, slewing bearing must withstand high loads, harsh weather conditions, and long service life.
Construction Machinery
Slewing bearings are commonly used in construction machinery such as cranes, excavators, and loaders. They enable the machinery to rotate and lift heavy loads. Slewing bearings in construction machinery must be durable, reliable, and able to withstand harsh environments.
Medical Equipment
Slewing bearings are also used in medical equipment such as CT scanners and MRI machines. They enable the equipment to rotate and scan the patient’s body. Slewing bearings in medical equipment must be precise, smooth, and able to operate quietly.
In addition to these applications, slewing bearings are also used in other industries such as aerospace, defense, and marine. Understanding their components, applications, and standards is crucial for selecting the right slewing bearing for a specific application. Ensuring proper maintenance and lubrication can also extend the service life of slewing bearings.
Installation and Maintenance
When it comes to installing and maintaining your slewing bearing, there are several things you should keep in mind to ensure optimal performance and longevity. This section will cover the main procedures you should follow, including Mounting Procedures, Lubrication and Sealing, and Inspection and Replacement.
Mounting Procedures
The first step in mounting your slewing bearing is to check it for physical damage. Lift the bearing with eye bolts, ensuring they are fully threaded into the bolt hole. Use a minimum thread engagement of 1.5 times the bolt diameter. The bearing should be mounted in an unloaded condition. Make sure the bearing mounting surfaces are machined flat after all welding and stress relief treatment on the structures is complete. If subsequent welding is necessary, it must be done before the bearing is mounted.
Lubrication and Sealing
Proper lubrication and sealing are essential to ensuring the longevity and optimal performance of your slewing bearing. The slewing ring raceway, the screw worm, and the bearings all need to be lubricated. Grease nipples are located on the bearing and should be lubricated with the recommended grease type and amount. Seals should be checked regularly for damage and replaced if necessary.
Inspection and Replacement
Regular inspection and replacement of damaged components are critical to maintaining the performance and longevity of your slewing bearing. Inspect the bearing raceway, worm gearing, and bearings regularly for signs of wear or damage. Replace any damaged components as soon as possible to avoid further damage or failure.
In summary, proper installation and maintenance of your slewing bearing is crucial to its performance and longevity. Follow the Mounting Procedures, ensure proper Lubrication and Sealing, and regularly inspect and replace damaged components to ensure optimal performance and longevity.
Performance and Specifications
When it comes to selecting a slewing bearing, there are several performance and specification factors to consider. In this section, we will cover the load ratings, accuracy and precision, and durability and lifespan of slewing bearings.
Load Ratings
One of the most important factors to consider when selecting a slewing bearing is its load rating. The load rating of a bearing is the maximum load it can support without experiencing permanent deformation or failure. Slewing bearing are designed to accommodate loads acting singly or in combination, and in any direction.
Manufacturers typically provide load rating information in their product specifications. It’s important to select a slewing bearing with a load rating that exceeds the expected load in your application.
Accuracy and Precision
Slewing bearing are designed to provide accurate and precise rotation. The accuracy of a bearing refers to its ability to maintain a consistent position during rotation. Precision refers to the ability to rotate smoothly and without vibration.
Manufacturers typically specify the accuracy and precision of their bearings in their product specifications. It’s important to select a bearing with the appropriate accuracy and precision for your application.
Durability and Lifespan
Slewing bearing are designed to provide long-lasting performance in demanding applications. The durability and lifespan of a bearing depend on several factors, including the materials used in its construction, the quality of its manufacturing, and the conditions in which it operates.
Manufacturers typically provide information on the durability and lifespan of their bearings in their product specifications. It’s important to select a bearing that can withstand the conditions in which it will operate and provide the required lifespan for your application.
In summary, when selecting a slewing bearing, it’s important to consider its load rating, accuracy and precision, and durability and lifespan. Manufacturers typically provide this information in their product specifications. Selecting the appropriate bearing for your application can help ensure reliable and long-lasting performance.