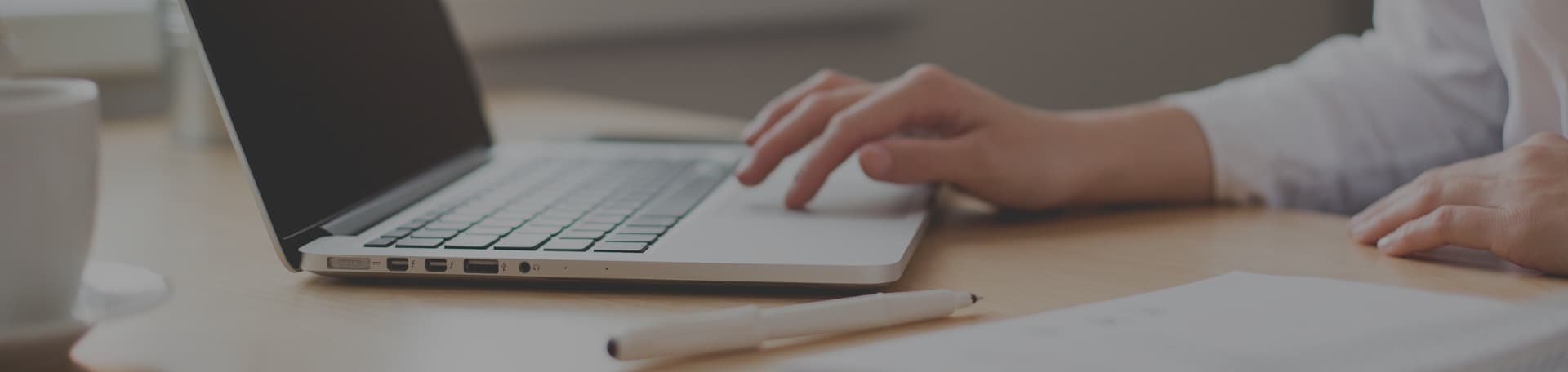
Slewing Manufacturer: A Guide to Choosing the Right One
Slewing Manufacturer: A Guide to Choosing the Right One
If you’re in the market for high-quality, custom-tailored slewing rings, drives, and gears, you’ll want to work with a reputable slewing manufacturer. These components are essential for manufacturing projects that require precise movement and positioning, and they must be manufactured to exacting standards to ensure the safety and reliability of the finished product.

A good slewing manufacturer will have the expertise and technology to produce a wide range of slewing rings, drives, and gears that can be customized to meet the specific needs of your project. They will also be able to offer guidance and support throughout the manufacturing process to ensure that your project is completed on time and within budget. Whether you need one slewing ring bearing or 100, a reputable manufacturer will be able to provide you with the precision-crafted components you need to get the job done right.
Overview of Slewing Manufacturers

Slewing bearings are critical components in various industrial applications, including cranes, excavators, wind turbines, and medical equipment. As a result, there are many manufacturers worldwide that specialize in designing, manufacturing, and supplying these components. In this section, we will provide an overview of slewing manufacturers, including their history and evolution and their global market presence.
History and Evolution
The history of slewing bearings dates back to the late 19th century, when they were first used in the construction of large telescopes. Since then, their usage has expanded to a wide range of industrial applications. Today, there are many manufacturers that specialize in the design and production of slewing bearings. Some of the most well-known manufacturers include SlewPro, Schaeffler Group USA Inc., Cone Drive, and TGB Group.
Over the years, the design and manufacturing processes for slewing bearings have evolved significantly. For example, modern slewing bearings are typically made from high-quality materials, such as alloy steels, and undergo rigorous testing to ensure their durability and performance. Additionally, manufacturers have developed specialized coatings and lubricants to improve the longevity and reliability of these components.
Global Market Presence
Slewing manufacturers have a global presence, with many companies operating in multiple countries and regions. For example, Xuzhou Wanda Slewing Bearing Co., Ltd. is a leading manufacturer of slewing bearings in China, while Triangle Manufacturing Company is a prominent manufacturer in the United States. Other manufacturers, such as igus, inc., have a global presence and supply slewing bearings to customers in various industries worldwide.
In addition to manufacturing slewing bearings, many companies also offer related services, such as repair and maintenance, engineering support, and custom design. This allows customers to work with manufacturers to develop customized solutions that meet their specific needs.
In summary, slewing manufacturers play a critical role in the design and production of slewing bearings. With a global market presence and a long history of innovation and evolution, these companies are well-positioned to meet the needs of customers in various industries worldwide.
Types of Slewing Bearings

When it comes to slewing bearings, there are several types to choose from. Each type is designed to handle different loads and provide specific benefits. In this section, we will explore the most common types of slewing bearings.
Single-Row Ball Type
Single-row ball slewing bearings are the most common type of slewing bearing. They consist of a single row of balls that are held in place by an inner and outer ring. This type of slewing bearing is ideal for lighter-duty applications and can handle both axial and radial loads. Single-row ball slewing bearings are also easy to install and maintain.
Double-Row Ball Type
Double-row ball slewing bearings have two rows of balls that are held in place by an inner and outer ring. This type of slewing bearing offers higher load capacity and stability compared to the single-row ball type. Double-row ball slewing bearings are ideal for applications that require higher loads and more stability.
Crossed Roller Type
Crossed roller slewing bearings use rollers instead of balls to handle loads. The rollers are crossed at a 90-degree angle and held in place by an inner and outer ring. This type of slewing bearing is ideal for applications that require high precision and stiffness. Crossed roller slewing bearings are commonly used in robotics, machine tools, and medical equipment.
Three-Row Roller Type
Three-row roller slewing bearings have three rows of rollers that are held in place by an inner and outer ring. This type of slewing bearing offers the highest load capacity and stiffness compared to the other types. Three-row roller slewing bearings are ideal for applications that require heavy loads and high stiffness, such as cranes, excavators, and wind turbines.
In summary, slewing bearings come in different types, each designed to handle different loads and provide specific benefits. The most common types are the single-row ball type, double-row ball type, crossed roller type, and three-row roller type. When choosing a slewing bearing, it is important to consider the application requirements and select the appropriate type.
Key Components of Slewing Systems
Slewing systems are used in a wide range of applications, from construction equipment to wind turbines. These systems consist of several key components that work together to provide smooth and efficient rotation. In this section, we will discuss the three main components of a slewing system: gear rings, sealing mechanisms, and lubrication systems.
Gear Rings
The gear ring is the most critical component of a slewing system. It is responsible for transmitting torque and providing a stable platform for the load. The gear ring is typically made of high-strength steel and is designed to withstand heavy loads and extreme temperatures.
There are two main types of gear rings: internal and external. Internal gear rings are typically used in applications where space is limited, while external gear rings are used in larger applications. Both types of gear rings can be customized to meet specific application requirements.
Sealing Mechanism
The sealing mechanism is another critical component of a slewing system. It is responsible for keeping dirt, debris, and other contaminants out of the system. The sealing mechanism also helps to prevent lubricant leakage, which can lead to premature wear and failure.
There are several types of sealing mechanisms available, including lip seals, labyrinth seals, and mechanical face seals. The type of sealing mechanism used will depend on the specific application requirements.
Lubrication Systems
The lubrication system is responsible for ensuring that the gear ring and other moving parts of the slewing system are properly lubricated. Proper lubrication is critical to the longevity and performance of the system.
There are two main types of lubrication systems: grease and oil. Grease lubrication is typically used in applications where the system is not exposed to extreme temperatures or heavy loads. Oil lubrication is used in more demanding applications, such as wind turbines and heavy construction equipment.
In conclusion, the gear ring, sealing mechanism, and lubrication system are the key components of a slewing system. Each component plays a critical role in ensuring the smooth and efficient rotation of the system. By selecting the right components for your specific application, you can ensure that your slewing system will provide reliable and long-lasting performance.
Manufacturing Processes
When it comes to manufacturing slewing bearings, there are several key processes that are involved in the production. These processes include forging and machining, heat treatment, and quality control and testing.
Forging and Machining
The first step in the manufacturing process is forging and machining. This involves creating the basic shape of the slewing bearing through the use of a forging press. This process is used to create the basic shape of the slewing bearing, which is then machined to the exact specifications required for the final product.
Heat Treatment
Once the slewing bearing has been forged and machined, it is then subjected to a heat treatment process. This involves heating the bearing to a specific temperature and holding it at that temperature for a set amount of time. The purpose of the heat treatment process is to improve the strength and durability of the bearing, making it more resistant to wear and tear.
Quality Control and Testing
The final step in the manufacturing process is quality control and testing. This involves a thorough inspection of the slewing bearing to ensure that it meets all of the required specifications and standards. The bearing is checked for any defects or imperfections, and is also subjected to a series of tests to ensure that it is capable of withstanding the stresses and strains that it will be subjected to in use.
Overall, the manufacturing of slewing bearings is a complex and intricate process that requires a high level of skill and expertise. By following these key processes, manufacturers are able to produce slewing bearings that are of the highest quality and durability, and that are capable of meeting the needs of a wide range of applications.
Applications of Slewing Bearings
Slewing bearings have a wide range of applications in various industries due to their versatile design and high load-carrying capacity. In this section, we will discuss some of the common applications of slewing bearings.
Wind Turbines
Slewing bearings are an essential component of wind turbines. They are used to support the weight of the rotor and enable it to rotate smoothly. The rotor blades are connected to the hub, which is mounted on the main shaft. The main shaft is then connected to the gearbox, which is connected to the generator. The slewing bearing enables the rotor to rotate in the wind and generate electricity.
Construction Machinery
Slewing bearings are used in construction machinery such as cranes, excavators, and loaders. They are used to support the weight of the boom and enable it to rotate. The slewing bearing also provides stability to the machinery and allows it to lift heavy loads.
Medical Equipment
Slewing bearings are used in medical equipment such as CT scanners and MRI machines. They are used to support the weight of the rotating components and enable them to rotate smoothly. The slewing bearing also provides precision and accuracy to the medical equipment, which is essential for diagnosis and treatment.
Industrial Machinery
Slewing bearings are used in various industrial machinery such as packaging machines, printing presses, and machine tools. They are used to support the weight of the rotating components and enable them to rotate smoothly. The slewing bearing also provides precision and accuracy to the machinery, which is essential for quality control and production efficiency.
In summary, slewing bearings have a wide range of applications in various industries due to their versatile design and high load-carrying capacity. They are essential components of wind turbines, construction machinery, medical equipment, and industrial machinery.
Selecting the Right Slewing Manufacturer
When it comes to selecting the right slewing manufacturer, there are several factors to consider. Choosing the right manufacturer can ensure that you receive a high-quality product that meets your specifications and requirements. Here are some key factors to consider when selecting a slewing manufacturer.
Certifications and Standards
Certifications and standards are important when selecting a slewing manufacturer. Look for manufacturers that have obtained certifications such as ISO 9001 (Quality Management) and ISO 14001 (Environmental Management). These certifications indicate that the manufacturer has implemented quality and environmental management systems that meet international standards.
Customization Capabilities
Customization capabilities are also important when selecting a slewing manufacturer. Look for manufacturers that can provide customized solutions to meet your specific needs. This may include designing and manufacturing slewing bearings that are tailored to your unique specifications and requirements.
After-Sales Support
After-sales support is another important factor to consider when selecting a slewing manufacturer. Look for manufacturers that provide comprehensive after-sales support, including technical support, training, and maintenance services. This can ensure that your slewing bearings continue to perform optimally throughout their lifespan.
In summary, when selecting a slewing manufacturer, it is important to consider factors such as certifications and standards, customization capabilities, and after-sales support. By choosing a manufacturer that meets these criteria, you can ensure that you receive a high-quality product that meets your specific needs and requirements.
Innovation in Slewing Manufacturing
When it comes to slewing manufacturing, there have been several advancements in materials and design that have led to more efficient and effective products. In this section, we will explore some of the most significant innovations in this field.
Material Advancements
One of the most significant material advancements in slewing manufacturing has been the use of high-strength steels. These materials are stronger, more durable, and can handle higher loads than traditional materials. This has led to the development of more compact and lightweight slewing bearings and drives that can handle heavier loads.
Another material advancement is the use of corrosion-resistant coatings. These coatings protect the slewing bearings and drives from harsh environments, such as saltwater and chemicals. This has led to increased durability and longer service life for these products.
Design Improvements
Design improvements have also played a significant role in the innovation of slewing manufacturing. One such improvement is the use of gearless drives. These drives eliminate the need for gears, which can be a source of wear and tear. This has led to more reliable and efficient slewing drives.
Another design improvement is the use of modular systems. These systems allow for greater flexibility in design and easier installation and maintenance. They also allow for easier customization of slewing bearings and drives to meet specific application requirements.
Overall, these material advancements and design improvements have led to more reliable, efficient, and effective slewing bearings and drives. As a result, they have become essential components in a wide range of industrial applications.
Challenges Facing Slewing Manufacturers
As a slewing manufacturer, there are several challenges that you may face in your day-to-day operations. Here are some of the most common challenges and how to overcome them.
Regulatory Compliance
Regulatory compliance is a major challenge for many slewing manufacturers. You must comply with regulations from various bodies such as OSHA, EPA, and others. Failure to comply with these regulations can result in hefty fines, lawsuits, and even shutdowns.
To overcome this challenge, you must stay up-to-date with the latest regulations and ensure that your operations are compliant. You may need to invest in training for your employees, equipment upgrades, and other measures to ensure that you are meeting all regulatory requirements.
Supply Chain Management
Supply chain management is another challenge that many slewing manufacturers face. You must ensure that you have a reliable supply chain for raw materials, components, and other supplies. Any disruptions in the supply chain can result in delays, increased costs, and other issues.
To overcome this challenge, you must have a robust supply chain management system in place. This may involve working with multiple suppliers, implementing inventory management systems, and other measures to ensure that you have a reliable supply chain.
Overall, these are just a few of the challenges that you may face as a slewing manufacturer. By staying informed, investing in the right resources, and implementing effective strategies, you can overcome these challenges and succeed in this competitive industry.