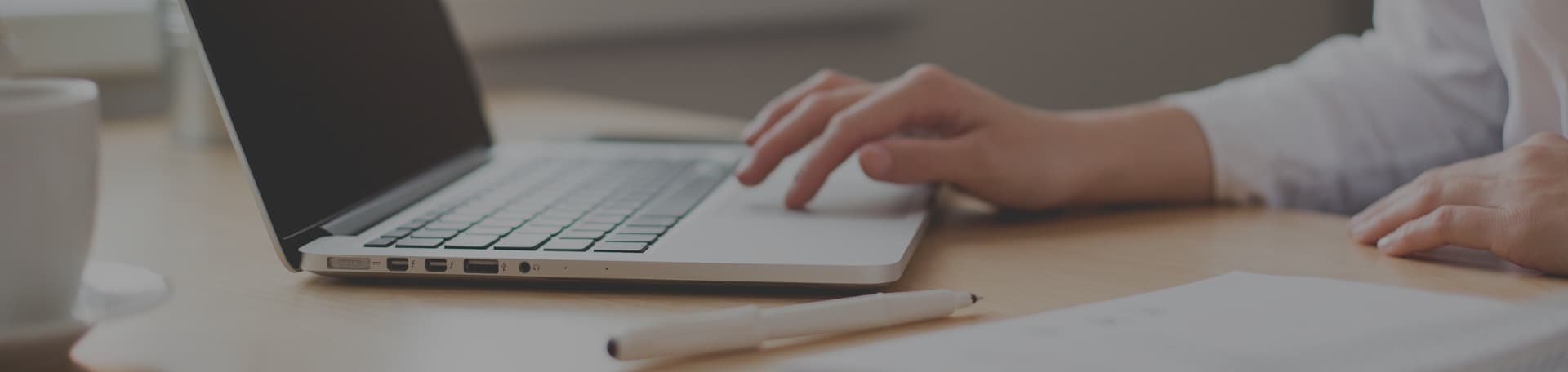
Slewing Platform Crane: A Comprehensive Overview
Slewing Platform Crane: A Comprehensive Overview
If you’re in the construction industry, you’re likely familiar with the term “slewing platform crane.” This type of crane is commonly used for heavy lifting on construction sites. Slewing platform cranes are designed to be stable, reliable, and capable of lifting heavy loads to great heights.

The slewing platform is the part of the crane that rotates and moves the load. It’s typically located at the top of the crane and is responsible for moving the load horizontally and vertically. The platform is connected to the crane’s base by a series of bearings and gears that allow it to rotate 360 degrees. This rotation is what gives the crane its versatility and allows it to reach loads in any direction.
Slewing platform cranes are used for a variety of tasks, from building skyscrapers to lifting heavy equipment. They are often used in the construction of large buildings, bridges, and other structures that require heavy lifting. The stability and versatility of the slewing platform crane make it an essential tool for any construction project that requires heavy lifting.
Design and Components

When it comes to slewing platform cranes, there are several key components that make up the design. Let’s take a closer look at each of these components and their functions.
Boom and Jib
The boom and jib are the primary components that extend out from the slewing platform and are responsible for lifting and moving heavy loads. The boom is the long, horizontal arm that extends out from the crane, while the jib is the shorter, angled arm that attaches to the end of the boom. Together, they provide the necessary reach and flexibility to maneuver loads into place.
Rotary Gear
The rotary gear is the mechanism that allows the slewing platform to rotate horizontally. It is typically located at the base of the crane and consists of a large ring gear and a pinion gear. The pinion gear is driven by a hydraulic motor, which allows for precise control of the rotation speed and direction.
Operator Cabin
The operator cabin is where the crane operator sits and controls the crane. It is typically located on the slewing platform and provides a clear view of the work area. The cabin is equipped with various controls and displays that allow the operator to monitor and adjust the crane’s movements.
Counterweights
Counterweights are used to balance the weight of the load being lifted and prevent the crane from tipping over. They are typically located at the rear of the crane and can be adjusted to match the weight of the load. The counterweights are usually made of concrete or steel and can weigh several tons.
Overall, the design and components of a slewing platform crane are carefully engineered to provide maximum lifting capacity and maneuverability while maintaining safety and stability.
Operational Principles

Slewing Mechanism
The slewing mechanism is the heart of the slewing platform crane. It allows the crane to rotate horizontally, thus expanding its reach and making it more versatile in handling different loads. The slewing mechanism consists of several components, including the slewing ring, the slew drive, and the hydraulic motor. The slewing ring is the component that supports the entire crane and allows it to rotate. The slew drive is the component that transmits the torque from the hydraulic motor to the slewing ring. The hydraulic motor is the component that provides the power to rotate the crane.
The slewing mechanism is designed to be efficient and reliable. It minimizes friction in the slewing mechanism, which results in higher slewing moment and faster operation. The crane can be used independent of the vehicle position, and load handling is possible even in tight spatial conditions. The elimination of catching and jerking during operation makes the crane operation smoother and safer.
Load Handling
The slewing platform crane is designed to handle different types of loads. It is capable of lifting heavy loads, and its versatility allows it to handle various shapes and sizes of loads. The crane can handle loads in different positions, including horizontal and vertical positions. The crane’s load capacity is determined by several factors, including the crane’s configuration, the load’s weight, and the load’s center of gravity.
The crane’s load handling is safe and efficient. The crane’s design includes safety features that prevent overloading and tipping. The crane’s load handling is also precise, thanks to the crane’s ability to rotate horizontally, which allows for accurate positioning of the load. The crane’s load handling is also smooth, thanks to the elimination of catching and jerking during operation.
In summary, the slewing platform crane’s operational principles are designed to be efficient, reliable, safe, and versatile. The crane’s slewing mechanism allows for faster and smoother operation, while the crane’s load handling is safe, precise, and smooth.
Safety Features
When it comes to operating a slewing platform crane, safety is of utmost importance. As such, these cranes come equipped with several safety features to ensure the safety of both the operator and those working in the vicinity. In this section, we will discuss two of the most important safety features of slewing platform cranes: Load Moment Indicators and Anti-Collision Systems.
Load Moment Indicators
Load Moment Indicators (LMIs) are essential safety features that help prevent crane accidents by monitoring the weight of the load being lifted and the angle and length of the boom. LMIs use sensors to measure the load and boom position, and they alert the operator when the crane is approaching its maximum capacity or when it is being operated outside of its safe operating range. This helps prevent overloading and tipping accidents, which can be catastrophic.
Anti-Collision Systems
Another important safety feature of slewing platform cranes is the Anti-Collision System (ACS). These systems use sensors to detect the presence of other cranes, buildings, or structures in the area and alert the operator if the crane is in danger of colliding with them. This helps prevent accidents caused by operator error or poor visibility, and it ensures that the crane is operated safely and efficiently.
In addition to LMIs and ACSs, slewing platform cranes also come equipped with emergency stop switches, access ladders, and other safety features designed to protect the operator and those working in the vicinity. By using these safety features in conjunction with proper training and safe operating procedures, you can ensure that your slewing platform crane is operated safely and effectively, reducing the risk of accidents and injuries.
Maintenance and Inspections
Maintaining and inspecting a slewing platform crane is crucial to ensure its safe and efficient operation. Neglecting maintenance and inspections can lead to equipment failure, damage, and even accidents.
Routine Checks
Performing routine checks is an essential part of maintaining a slewing platform crane. You should conduct daily visual inspections of the crane, which includes checking for any signs of wear and tear, damage, or loose bolts.
One of the critical components of a slewing platform crane is the slewing gear. You should inspect the slewing gear regularly for any signs of damage or wear. The bolts holding the slewing bearing parts to the crane pedestal and crane body should be periodically checked in line with the manufacturer’s recommendations.
Another routine check that you should perform is the rocking test. The rocking test is a measurement of the deflection between the crane pedestal and the slewing ring bearing. The vessel’s planned maintenance system should include a rocking test, and each crane should be tested every six months. A record of these tests must be entered into the Registry of Lifting Appliances.
Professional Inspections
Professional inspections of a slewing platform crane should be performed annually or bi-annually by a qualified and competent inspector. The professional inspection should include a thorough examination of the crane’s structural components, electrical systems, and mechanical systems.
The inspector should check for any signs of wear and tear, damage, or corrosion. They should also inspect the crane’s wire ropes, hooks, and other lifting equipment. The inspector should ensure that the crane is in compliance with all applicable regulations and standards.
In conclusion, routine checks and professional inspections are necessary to ensure the safe and efficient operation of a slewing platform crane. Neglecting maintenance and inspections can lead to equipment failure, damage, and accidents.
Applications and Use Cases
Slewing platform cranes have a wide range of applications in various industries, from construction sites to ports and shipyards.
Construction Sites
One of the most common applications of slewing platform cranes is in construction sites. These cranes are used to lift and move heavy materials, such as steel beams, concrete blocks, and pre-fabricated building components. Slewing platform cranes are particularly useful in construction sites because they can be easily maneuvered to different locations, allowing for efficient and safe material handling. Additionally, many modern slewing platform cranes are equipped with advanced safety features, such as anti-collision systems, which help prevent accidents and injuries.
Ports and Shipyards
Another major application of slewing platform cranes is in ports and shipyards. These cranes are used to load and unload cargo from ships, as well as move cargo around the port or shipyard. Slewing platform cranes used in these applications are often massive structures, capable of lifting and moving containers weighing several tons. They are also equipped with specialized features, such as spreader bars, which allow them to lift and move cargo containers safely and efficiently.
In summary, slewing platform cranes are versatile machines that are used in a variety of industries. They are particularly useful in construction sites and ports and shipyards, where they help improve efficiency, safety, and productivity.