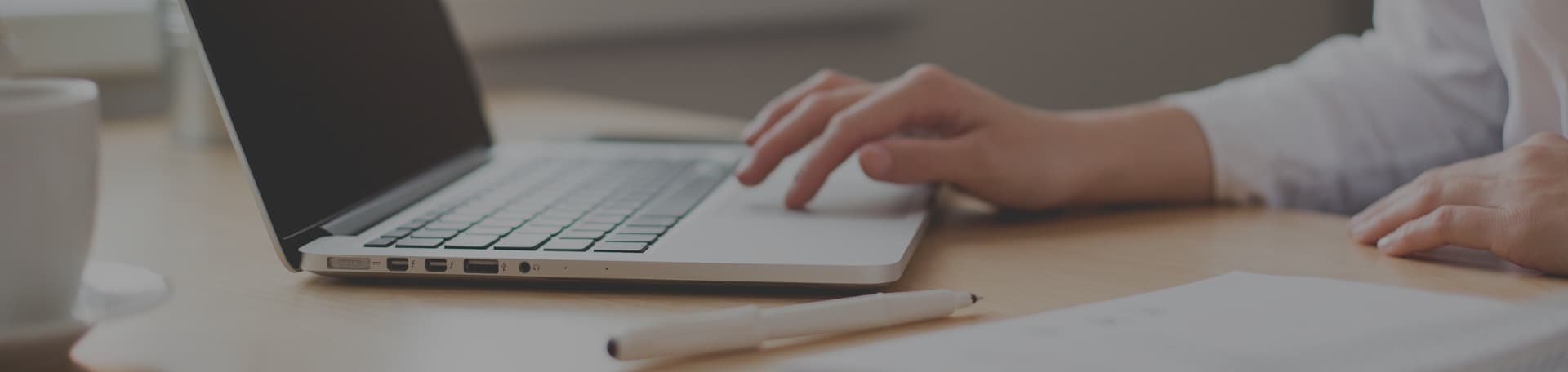
Slewing Ring Repair: Expert Tips and Cost-effective Solutions
Slewing Ring Repair: Expert Tips and Cost-effective Solutions
If you need a slewing ring repair, you’re likely dealing with a large piece of machinery that is essential to your business operations. A slewing ring, also known as a turntable bearing, is a critical component in heavy equipment such as cranes, excavators, and wind turbines. It allows the equipment to rotate horizontally and vertically, making it possible to lift and move heavy loads.

Over time, slewing rings can experience wear and tear, leading to malfunctions that can bring your operations to a halt. Fortunately, there are companies that specialize in slewing ring repair and remanufacturing. These companies can diagnose the issue and provide solutions to get your equipment back up and running as quickly as possible. In some cases, it may be more cost-effective to have your slewing ring remanufactured rather than replaced entirely. This involves disassembling the bearing, cleaning and inspecting the components, and replacing any damaged or worn parts. By choosing to remanufacture your slewing ring, you can save money and extend the life of your equipment.
Understanding Slewing Rings

Design and Functionality
Slewing rings, also known as slewing bearings or turntable bearings, are an essential component of heavy machinery that allows the machine’s superstructure to rotate. They are typically used in construction equipment, cranes, wind turbines, and other industrial applications.
Slewing rings consist of two rings, the inner ring, and the outer ring. The inner ring is the stationary part of the slewing bearing and connects to the machinery’s structure. It acts as a fixed base for the bearing system and provides a pivot point for controlled rotation. The outer ring is the part of the slewing bearing that rotates, and it carries the load.
Slewing rings are designed to handle axial, radial, and moment loads, making them ideal for applications that require high load capacity and low friction. They can also handle tilting moments, which are moments that occur when the load is not evenly distributed across the bearing’s surface.
Common Failures
Slewing rings are designed to last for a long time, but they can fail due to various reasons. The most common causes of slewing ring failure are improper installation, overloading, and lack of maintenance.
Improper installation can cause misalignment, which can lead to premature wear and tear of the slewing ring. Overloading can cause excessive stress on the bearing, leading to cracks, and ultimately, failure. Lack of maintenance can cause corrosion, which can weaken the bearing’s structure and lead to failure.
Regular maintenance is crucial to prevent slewing ring failure. The maintenance schedule should include regular inspections, lubrication, and cleaning. Inspections should be done to check for signs of wear and tear, such as cracks, corrosion, or pitting. Lubrication is essential to reduce friction and wear between the bearing’s surfaces. Cleaning is necessary to remove debris and contaminants that can cause damage to the bearing’s surface.
In conclusion, understanding the design and functionality of slewing rings and common failures is crucial to prevent premature failure and ensure the smooth operation of heavy machinery. Regular maintenance and inspections are necessary to identify and address any issues before they cause significant damage to the bearing.
Inspection Procedures
When repairing a slewing ring bearing, it is important to conduct a thorough inspection to identify any damage or wear that may affect the bearing’s performance. The inspection process should include visual inspection, dimensional verification, and non-destructive testing.
Visual Inspection
The first step in the inspection process is a visual inspection. This involves examining the bearing for any visible signs of damage, such as cracks, corrosion, or wear. You should also check for any signs of misalignment or improper installation, such as bent bolts or uneven wear patterns.
Dimensional Verification
Dimensional verification is the next step in the inspection process. This involves measuring the bearing’s dimensions to ensure that it is within the manufacturer’s specifications. You should check the bearing’s inner and outer diameters, as well as its width and height. You should also check the dimensions of any mating components, such as the housing or shaft, to ensure that they are within tolerance.
Non-Destructive Testing
Non-destructive testing is the final step in the inspection process. This involves testing the bearing for any hidden defects or damage that may not be visible to the naked eye. There are several non-destructive testing methods available, including magnetic particle inspection, ultrasonic testing, and dye penetrant inspection. You should select the method that is most appropriate for the type of damage or wear that you suspect.
In summary, the inspection process is a critical step in the slewing ring bearing repair process. By conducting a thorough inspection, you can identify any damage or wear that may affect the bearing’s performance and take appropriate corrective action.
Repair Techniques
When it comes to repairing slewing rings, there are a few different techniques that can be used depending on the extent of the damage. Here are some common repair techniques:
Welding and Machining
If the slewing ring has minor damage, such as a crack or a small dent, welding and machining may be a viable option. This technique involves welding the damaged area and then machining it down to the correct dimensions. It is important to note that this technique should only be used for minor damage, as welding can weaken the metal and compromise the integrity of the slewing ring.
Bearing Replacement
If the damage to the slewing ring is more severe, such as a complete failure of the bearing, then bearing replacement may be necessary. This involves removing the old bearing and installing a new one. It is important to ensure that the new bearing is the correct size and type for the slewing ring.
Surface Treatments
Another technique that can be used to repair slewing rings is surface treatments. This involves treating the surface of the slewing ring to improve its performance. For example, a surface treatment may be used to improve the wear resistance or corrosion resistance of the slewing ring. Common surface treatments include hard chrome plating, nitriding, and thermal spraying.
In conclusion, there are a few different techniques that can be used to repair slewing rings, depending on the extent of the damage. Welding and machining may be used for minor damage, while bearing replacement may be necessary for more severe damage. Surface treatments can also be used to improve the performance of the slewing ring. It is important to choose the right technique for the job to ensure that the slewing ring is repaired properly and functions correctly.
Reassembly and Testing
Now that you have disassembled and repaired the slewing ring bearing, it’s time to reassemble and test it. Here are the steps you need to follow:
Precision Installation
- Clean the bearing components thoroughly with a solvent and dry them with compressed air.
- Apply a thin layer of lubricant to the raceways and gear teeth of the slewing ring bearing.
- Install the slewing ring bearing onto the mounting surface, making sure that it is properly aligned with the mating components.
- Tighten the bolts in a cross pattern to the specified torque. Refer to the manufacturer’s instructions for the correct torque values and tightening sequence.
- Install the seals, gaskets, and other components as necessary.
Performance Testing
After the slewing ring bearing has been reassembled, it’s important to test its performance to ensure that it is functioning properly. Here are the steps you need to follow:
- Perform a visual inspection of the slewing ring bearing to ensure that it is properly installed and aligned.
- Check the bearing for smooth rotation and proper clearance. If there is any binding or resistance, disassemble and inspect the bearing for any defects or misalignment.
- Perform a load test on the bearing to ensure that it can handle the required loads. Refer to the manufacturer’s instructions for the correct load testing procedure.
- Perform a leak test on the seals and gaskets to ensure that there are no leaks.
- Record the test results and compare them to the manufacturer’s specifications.
By following these steps, you can ensure that your repaired slewing ring bearing is functioning properly and will provide reliable performance.
Maintenance Best Practices
Maintaining your slewing ring is crucial to ensure that it operates smoothly and efficiently. Here are some best practices that you should follow to keep your slewing ring in top condition:
Regular Inspection
Inspect your slewing ring regularly to identify any signs of wear or damage. Look for signs of corrosion, cracks, or deformation. Pay attention to the bolts and connections for looseness or wobbling. If you notice any issues, address them promptly to prevent further damage.
Lubrication
Proper lubrication is essential to keep your slewing ring operating smoothly. Follow the manufacturer’s instructions for lubrication intervals and use the recommended type of grease. Over-greasing can cause damage, so be careful not to overdo it.
Handling
Slewing ring bearings are large and heavy, so proper handling is crucial to avoid damage during installation. Use lifting equipment and follow safe handling procedures to prevent drops or impacts.
Alignment
Ensure that the slewing ring bearing is properly aligned with the mating components to avoid excessive load. Incorrect alignment can cause damage to the slewing ring and other components.
By following these maintenance best practices, you can ensure that your slewing ring operates smoothly and efficiently, reducing the risk of downtime and costly repairs.