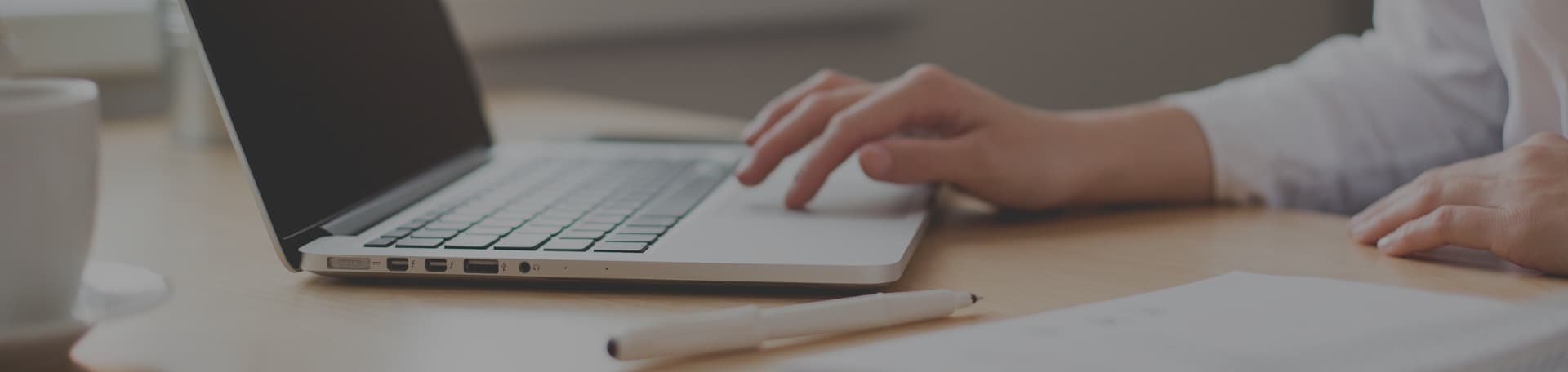
Turntable Bearing Grease: Everything You Need to Know
Turntable Bearing Grease: Everything You Need to Know
If you’re a turntable enthusiast, you know that regular maintenance is essential for optimal performance. One of the most crucial components of a turntable is the bearing. The bearing is responsible for supporting the weight of the platter and ensuring that it spins smoothly and evenly. Over time, the bearing can become dirty or worn, leading to poor performance and potential damage to your records.

This is where turntable bearing grease comes in. Grease is a lubricant that helps reduce friction between moving parts, keeping them running smoothly and preventing wear and tear. Applying grease to the bearing of your turntable can help extend its lifespan and improve its overall performance. But what kind of grease should you use, and how should you apply it?
Types of Turntable Bearing Grease

When it comes to selecting the right grease for your turntable, you have several options to choose from. Each type of grease has its own unique properties that make it suitable for different turntable components. In this section, we will discuss the three most common types of turntable bearing grease: Lithium-Based, Silicone-Based, and Graphite-Based.
Lithium-Based Grease
Lithium-based grease is a popular choice for turntable lubrication. It is a general-purpose grease that is commonly used in automotive and industrial applications. Lithium-based grease is known for its excellent water resistance and high-temperature stability. It is also resistant to oxidation and corrosion, making it ideal for protecting your turntable’s bearings from wear and tear.
Silicone-Based Grease
Silicone-based grease is another popular option for turntable lubrication. It is a synthetic grease that is highly resistant to water, heat, and oxidation. It offers excellent thermal stability and a wide temperature operating range. Silicone grease is particularly well-suited for the lubrication of bearings and spindle points in a record player.
Graphite-Based Grease
Graphite-based grease is a specialized type of grease that contains graphite particles. It is commonly used in applications where high temperatures and heavy loads are present. Graphite-based grease is known for its excellent lubrication properties and its ability to reduce friction and wear. It is ideal for use in turntable bearings and other high-load applications.
In summary, when selecting turntable bearing grease, you have several options to choose from, including Lithium-Based, Silicone-Based, and Graphite-Based. Each type of grease has its own unique properties that make it suitable for different turntable components. By selecting the right grease for your turntable, you can ensure that it operates smoothly and reliably for years to come.
Application of Turntable Bearing Grease

When it comes to turntable maintenance, one of the most important aspects is the application of bearing grease. Properly lubricated bearings ensure smooth rotation and prevent unnecessary wear and tear on your turntable. In this section, we will discuss two methods for applying turntable bearing grease: manual application and automatic lubrication systems.
Manual Application
Manual application of turntable bearing grease involves physically applying the grease to the bearings using a grease gun or other applicator. This method is typically used for smaller turntables or for those that require less frequent maintenance.
To manually apply turntable bearing grease, first, remove the platter and clean the bearing surfaces thoroughly. Next, apply a small amount of grease to the bearing surfaces using a grease gun or other applicator. Be sure to use the appropriate type of grease for your turntable, as different types of turntables require different types of grease.
Automatic Lubrication Systems
For larger turntables or those that require more frequent maintenance, automatic lubrication systems may be used. These systems typically use a pump or other mechanism to automatically apply grease to the bearings on a regular basis.
Automatic lubrication systems are typically more expensive than manual application methods, but they can save time and effort in the long run. They also ensure that the turntable is properly lubricated at all times, which can help to extend the life of the turntable and prevent unnecessary wear and tear.
In summary, the application of turntable bearing grease is an important aspect of turntable maintenance. Whether you choose to manually apply grease or use an automatic lubrication system, be sure to use the appropriate type of grease for your turntable and follow proper maintenance procedures to ensure smooth rotation and prevent unnecessary wear and tear.
Maintenance and Grease Replacement
Proper maintenance of your turntable bearing is essential to ensure optimal performance and longevity. In this section, we will discuss the recommended inspection intervals, cleaning procedures, and grease replenishment.
Inspection Intervals
Regular inspection of the turntable bearing is critical to detect any signs of wear or damage. You should inspect the bearing at least once a year or more frequently if you use your turntable frequently. Signs of wear and tear include excessive noise, vibration, and irregular platter rotation. If you notice any of these signs, it is recommended to inspect the bearing immediately.
Cleaning Procedures
Before you begin any maintenance procedures, make sure to disconnect the turntable from the power source. To clean the bearing, remove the platter and clean the spindle and bearing housing thoroughly with a soft, lint-free cloth. Avoid using any abrasive materials or solvents that can damage the bearing or spindle.
Grease Replenishment
The turntable bearing requires a specific type of grease to function correctly. Over time, the grease may dry out or become contaminated, leading to increased friction and wear. It is recommended to replenish the grease every two to three years or sooner if the bearing shows signs of wear.
To replenish the grease, you will need to remove the platter and spindle, clean the bearing housing, and apply a small amount of new grease to the bearing. Use a high-quality, lithium-based grease designed for turntable bearings. Avoid over-greasing the bearing, as this can lead to excess friction and damage to the spindle.
In conclusion, regular maintenance and grease replenishment are essential to ensure optimal performance and longevity of your turntable bearing. By following the recommended inspection intervals, cleaning procedures, and grease replenishment, you can enjoy high-quality sound and smooth operation from your turntable for years to come.
Performance Factors of Grease
When choosing the best grease for your turntable, there are several performance factors that you should consider. These factors can affect the overall sound quality, longevity, and performance of your turntable.
Viscosity
Viscosity is the measure of a fluid’s resistance to flow. In the case of turntable bearing grease, a higher viscosity means that the grease is thicker and will stay in place better. This is important because turntable bearings require a grease that will stay in place and not migrate out of the bearing over time.
Temperature Stability
Temperature stability is another important factor to consider when choosing a turntable bearing grease. Turntables can generate a lot of heat during use, and a grease that can’t handle high temperatures can break down quickly, leading to poor performance and potential damage to your turntable.
Load-Bearing Capacity
Load-bearing capacity is the amount of weight or pressure that a grease can handle without breaking down. Turntable bearings require a grease that can handle the weight of the platter and tonearm without breaking down over time.
When choosing a turntable bearing grease, be sure to consider these performance factors to ensure that you get the best possible performance and longevity out of your turntable.
Safety and Environmental Considerations
Toxicity and Handling
When handling turntable bearing grease, it is important to take safety precautions to avoid any potential hazards. Turntable bearing grease may contain toxic substances such as lead, copper, and zinc, which can cause harm if ingested or inhaled. Therefore, it is important to wear protective gear such as gloves and masks when handling the grease to avoid any direct contact with the skin or inhalation of the fumes.
Additionally, it is important to store turntable bearing grease in a cool, dry, and well-ventilated area to prevent any potential hazards. Exposure to high temperatures or direct sunlight can cause the grease to deteriorate and become hazardous.
Disposal and Recycling
Proper disposal and recycling of turntable bearing grease is essential to prevent environmental pollution. It is important to dispose of used grease in accordance with local regulations and guidelines. Used grease can be recycled through various methods such as re-refining or reprocessing.
When disposing of used grease, it is important to avoid pouring it down the drain or disposing of it in the trash as it can cause blockages and environmental pollution. Instead, it can be collected and sent to a recycling facility or disposed of through a licensed waste disposal service.
In conclusion, handling and disposing of turntable bearing grease requires proper safety precautions and adherence to environmental regulations to avoid any potential hazards and environmental pollution.